what is sealing machine | YUANYANG Expert Guide
- Understanding Sealing Machines: A Comprehensive Guide for Industrial Buyers
- What are the different types of sealing machines?
- What factors should I consider when choosing a sealing machine?
- What are some common problems with sealing machines and how can I prevent them?
- How can I improve the efficiency of my sealing process?
- What are the latest innovations in sealing machine technology?
Understanding Sealing Machines: A Comprehensive Guide for Industrial Buyers
In the industrial sector, sealing machines are critical for packaging and preserving a vast array of products. Choosing the right sealing machine can significantly impact production efficiency, product integrity, and overall cost-effectiveness. This guide addresses common questions and provides essential knowledge for industrial buyers looking to invest in or upgrade their sealing equipment.
What are the different types of sealing machines?
Sealing machines come in various forms, each designed for specific applications. Some of the most common types include:
- Heat Sealers: These machines use heat to melt and fuse thermoplastic materials together. They are widely used for sealing bags, pouches, and blister packs. Heat sealers can be further categorized into:
- Impulse Sealers: Use a short burst of heat and are suitable for low-volume applications.
- Direct Heat Sealers: Maintain a constant temperature and are ideal for thicker materials.
- Induction Sealers: Utilize electromagnetic induction to heat a foil liner inside a cap or closure, creating a hermetic seal. They are commonly used in the food, beverage, and pharmaceutical industries.
- Vacuum Sealers: Remove air from the packaging before sealing, extending the shelf life of perishable goods. These are extensively used in food processing and packaging.
- Ultrasonic Sealers: Employ high-frequency sound waves to create a bond, often used for sealing rigid containers and plastics.
- Form-Fill-Seal (FFS) Machines: Automate the entire packaging process, from forming the container to filling it with product and sealing it. These are commonly found in high-volume production lines.
The selection of the appropriate sealing machine type depends heavily on the materials being sealed, the production volume, and the desired seal quality.
What factors should I consider when choosing a sealing machine?
Several factors must be considered to ensure you select the most suitable sealing machine for your needs:
- Material Compatibility: Ensure the machine is compatible with the materials you intend to seal (e.g., polyethylene, polypropylene, laminates).
- Production Volume: Determine the required throughput to select a machine with appropriate speed and automation capabilities. Manual sealers are suitable for low volumes, while automated systems are ideal for high-speed production.
- Seal Quality: Consider the required seal integrity and appearance. Hermetic seals are necessary for products requiring extended shelf life or protection from contaminants.
- Maintenance Requirements: Evaluate the ease of maintenance and availability of spare parts. Machines with readily available parts and simple maintenance procedures can minimize downtime.
- Cost: Balance the initial investment cost with the long-term operational costs, including energy consumption, maintenance, and potential downtime.
- Footprint: Consider the available space in your facility, as some industrial sealing machines can be quite large.
What are some common problems with sealing machines and how can I prevent them?
Common issues with sealing machines include inconsistent seals, machine downtime, and material waste. Preventive measures include:
- Regular Maintenance: Implement a routine maintenance schedule to inspect and replace worn parts.
- Proper Training: Ensure operators are properly trained on the machine's operation and troubleshooting procedures.
- Material Handling: Use high-quality packaging materials and ensure they are stored properly to prevent damage or contamination.
- Temperature Control: Regularly calibrate and monitor temperature settings to ensure consistent sealing.
- Cleanliness: Keep the machine clean and free of debris to prevent jams and malfunctions.
How can I improve the efficiency of my sealing process?
To optimize the efficiency of your sealing process, consider the following strategies:
- Automation: Integrate automated feeding and sealing systems to increase throughput and reduce labor costs. FFS machines are a great example of this. They can significantly reduce manpower and increase overall efficiency.
- Process Optimization: Fine-tune machine settings and processes to minimize material waste and improve seal quality.
- Ergonomics: Design the workstation to be ergonomic and comfortable for operators, reducing fatigue and improving productivity.
- Data Analysis: Collect and analyze data on machine performance to identify areas for improvement.
What are the latest innovations in sealing machine technology?
The sealing machine industry is continuously evolving, with innovations focused on improving efficiency, sustainability, and product safety. Recent advancements include:
- Smart Sealing Machines: Equipped with sensors and data analytics capabilities to monitor performance, predict maintenance needs, and optimize sealing parameters.
- Sustainable Packaging Solutions: Designed to work with eco-friendly packaging materials, such as biodegradable films and recycled plastics.
- Advanced Sealing Techniques: Utilizing technologies like laser sealing and cold sealing to improve seal integrity and reduce energy consumption.
- Robotics Integration: Integrating robotic arms for automated material handling and packaging, leading to increased efficiency and reduced labor costs.
By staying informed about these advancements, industrial buyers can make strategic decisions to invest in sealing machines that meet their current and future needs.
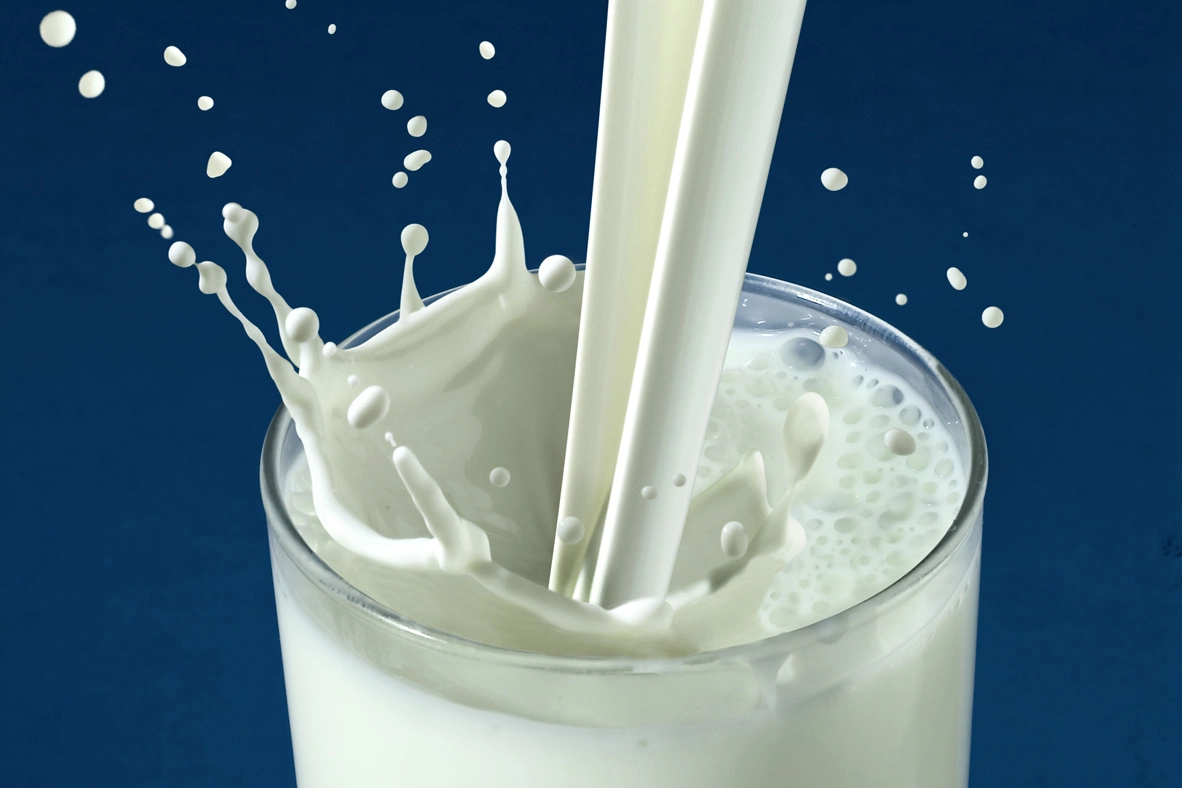
Milk Homogenization Process: Everything You Need to Know About How It Works
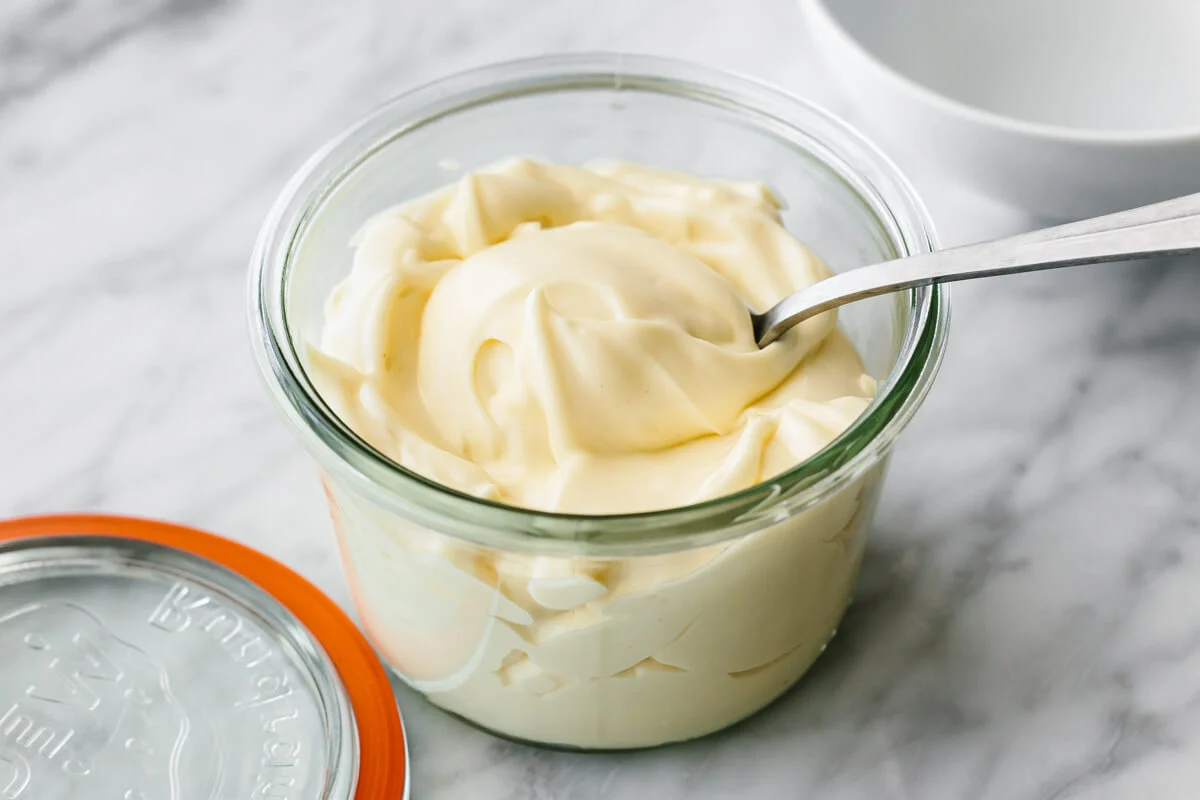
Mayonnaise Manufacturing Process Explained: How Factories Produce Mayonnaise

Water in Oil Emulsion: Meaning, Real-Life Examples, and How to Fix It
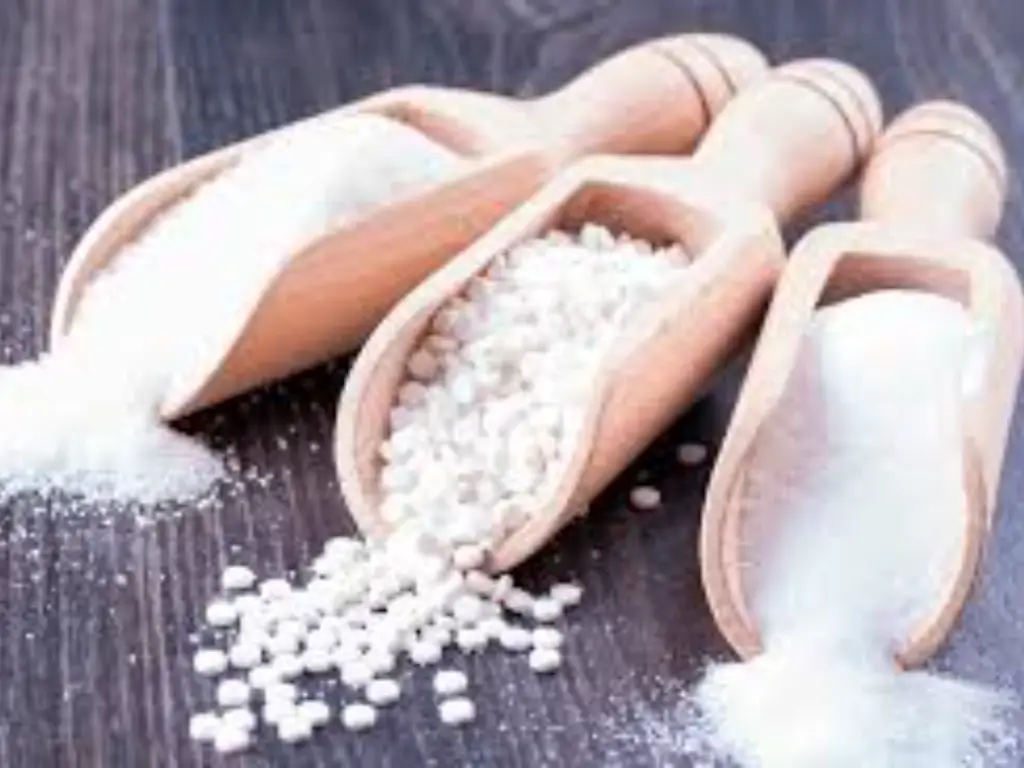
How Artificial Sweeteners Are Made: Inside the Manufacturing Process & Key Equipment
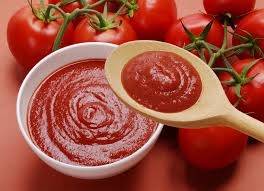
Ketchup Explained: From Ancient Origins to Modern Production Methods
Food
Do you support international shipping and installation?
Yes, we provide global delivery services and offer international installation and commissioning services to ensure you can smoothly use the equipment for production.
Automatic Screw Capping Machine
What minimum and maximum caps size can the bottle capper machine be suit for?
The cap diameter of standard 4 wheels capping machine is 20-75mm, but can be slightly customized according real cases.
Vacuum Homogneizer
Can you explain the difference between homogenizer mixing tank and agitator mixing tank?
Homogenizer mixer is also called high shear mixer, whose core function is micronization and homogenization. The homogenization process enables the dispersion size in the suspension or emulsion to be micron fine particles by mechanical force of rotor and stator, thereby improving the stability and uniformity of the product.
The agitator mixing tank is just with normal blending function, just mix different materials together, but can’t mix two incompatible liquids together.
One Stage Water Treatment
What type of water can we use for this pure water filter ?
The raw quality (conductivity) should be ≤300μs/cm), such as city tap water, lake water, underground water, river water...
Desktop Labeling Machine
What types bottles are suitable for this automatic labeling machine?
The automatic labeling machine for bottles is suitable for round bottles, jars, cans, bucket. It is a round bottle labeling machine.
Leave a message
Have any questions or concerns about our products? Please leave us a message here, and our team will get back to you promptly.
Facebook
YouTube
LinkedIn
Whatsapp: +8613434139712
Guangzhou Yuanyang Machinery