what is a disperser | YUANYANG Expert Guide
- What is a Disperser and How Does It Work?
- How Does a Disperser Differ from a Mixer or Homogenizer?
- What are the Main Types of Industrial Dispersers?
- What Industries and Applications Benefit from Dispersers?
- What Key Factors Should I Consider When Purchasing an Industrial Disperser?
- YUANYANG Brand Advantages
What is a Disperser and How Does It Work?
At its core, an industrial disperser is a high-speed, high-shear mixing machine designed to de-agglomerate solid particles into a liquid phase, achieving a homogeneous and stable dispersion. Unlike conventional agitators that primarily blend, a disperser utilizes a high-velocity rotating impeller (often a Cowles blade or saw-tooth disc) to create intense turbulent flow, generating high shear forces and cavitation. This mechanical action breaks down aggregates of particles, reducing their size and distributing them uniformly throughout the liquid. The tip speed of a disperser blade can typically range from 18 to 30 meters per second (m/s), creating the necessary energy input for effective de-agglomeration.
How Does a Disperser Differ from a Mixer or Homogenizer?
While often used interchangeably in layman's terms, 'mixer,' 'disperser,' and 'homogenizer' refer to distinct categories of industrial equipment with specific functionalities and shear capabilities:
- Mixer (Agitator): Generally refers to low-shear equipment, such as propeller mixers or paddle agitators, used for simple blending, dissolving, or maintaining suspension. They create bulk flow but lack the intense shear required for de-agglomeration or fine particle size reduction. Typical applications include chemical blending or wastewater treatment.
- Disperser: Operates at medium to high shear, specifically designed for breaking down soft to medium-hard agglomerates into primary particles or fine dispersions. Its primary function is particle size reduction and uniform distribution in a liquid medium. Common in paint, ink, and coating industries where particle de-agglomeration is key.
- Homogenizer: Represents the highest level of shear, often operating under very high pressures (e.g., 1000-10,000 psi or 70-700 bar for high-pressure homogenizers). They create extremely fine emulsions or dispersions, often reducing particle sizes into the sub-micron or nanometer range. Used extensively in food (e.g., milk, mayonnaise), pharmaceutical, and cosmetic industries for ultra-fine emulsions and stable suspensions.
What are the Main Types of Industrial Dispersers?
The choice of disperser type depends heavily on the viscosity of the material, desired particle size, and batch volume. Key types include:
- High-Speed Dispersers (Cowles Dispersers): The most common type, featuring a single, high-speed rotating saw-tooth disc. Ideal for materials up to 50,000 centipoise (cP) viscosity. They are excellent for initial breakdown and dispersion of pigments in paints, inks, and coatings.
- Basket Mill Dispersers: Combine dispersion and milling in one unit. The dispersing blade is contained within a screen basket filled with grinding media (e.g., ceramic or zirconia beads). This allows for finer particle size reduction, often down to a few microns, in a single pass. Suitable for medium to high viscosity products.
- Vacuum Dispersers: Equipped with a vacuum system to remove air and volatiles during the dispersion process. This is crucial for products where air entrapment is detrimental, such as certain adhesives, sealants, or highly sensitive chemical formulations. It also helps prevent foaming and ensures product stability.
- Dual-Shaft Dispersers: Feature two co-axial shafts, often one with a high-speed disperser blade and the other with a low-speed anchor or scraper blade. This configuration is ideal for highly viscous materials (up to 1,000,000 cP or more) where the anchor blade ensures proper material flow to the high-shear disperser blade.
What Industries and Applications Benefit from Dispersers?
Industrial dispersers are workhorses across numerous manufacturing sectors where uniform particle distribution and consistency are critical. Some prominent industries and applications include:
- Paints and Coatings: Pigment dispersion for automotive paints, architectural coatings, industrial finishes, and decorative paints. Ensures color strength, gloss, and stability.
- Inks: Dispersion of pigments for printing inks (flexographic, gravure, offset), ensuring color intensity and print quality.
- Adhesives and Sealants: Dispersion of fillers and rheology modifiers to achieve desired bond strength, viscosity, and application properties.
- Chemicals: Production of various chemical slurries, suspensions, and emulsions; dispersion of active ingredients in agrochemicals.
- Cosmetics and Personal Care: Dispersion of powders in creams, lotions, and makeup products for smooth texture and consistent formulation.
- Pharmaceuticals: Wetting and de-agglomeration of active pharmaceutical ingredients (APIs) in liquid formulations (though often requiring specific sanitary designs and higher-level homogenization for final products).
What Key Factors Should I Consider When Purchasing an Industrial Disperser?
Selecting the right disperser is a strategic investment that impacts productivity, product quality, and operational efficiency. Consider these crucial factors:
- Process Requirements:
- Product Viscosity Range: Does your product range from low (water-like) to very high (putty-like) viscosity? This dictates the motor power, blade type, and whether a dual-shaft system is needed.
- Target Particle Size: What is the desired final particle size? This determines the required shear intensity and potentially the need for a basket mill over a standard high-speed disperser.
- Batch Volume: Match the disperser's capacity to your typical batch size to ensure efficient processing and prevent under- or overloading.
- Material Compatibility and Construction:
- Materials of Construction: For corrosive or abrasive products, consider stainless steel grades like SS316L. For sanitary applications (food, pharma), ensure polished surfaces and hygienic design.
- Sealing Systems: Choose appropriate shaft seals (e.g., mechanical seals, stuffing box) based on product characteristics and operating conditions to prevent leaks and contamination.
- Safety and Regulatory Compliance:
- Explosion-Proof (Ex-proof) Design: If processing flammable solvents or materials, an ATEX or equivalent explosion-proof rating is mandatory to prevent ignition.
- Interlocks and Safety Features: Ensure the machine has safety interlocks to prevent operation when covers are open or the mixing shaft is not properly seated.
- Compliance: Check for local and international standards (e.g., CE, UL, FDA for specific industries).
- Energy Efficiency and Control:
- Motor and VFD: Look for energy-efficient motors and Variable Frequency Drives (VFDs) for precise speed control, which saves energy and allows process optimization.
- Automation: Consider options for automated lift, vacuum control, or temperature monitoring for consistent batch quality and reduced manual labor.
- Maintenance and Serviceability:
- Ease of Cleaning: Design features that facilitate quick and thorough cleaning are essential, especially when changing products.
- Durability and Longevity: Evaluate the build quality, bearing life, and availability of spare parts.
- Supplier Support: A reputable supplier offers excellent after-sales service, technical support, and readily available spare parts.
Choosing the right industrial disperser is a critical decision that impacts product quality, operational efficiency, and long-term cost of ownership. By thoroughly evaluating your specific process requirements, material characteristics, and safety considerations, you can make an informed investment that yields significant returns.
YUANYANG Brand Advantages
As a leading manufacturer in industrial mixing equipment, YUANYANG offers robust and innovative disperser solutions tailored to your needs. Our advantages include:
- Robust Engineering & Durability: YUANYANG dispersers are built with high-quality materials and precision engineering, ensuring long operational life and minimal downtime even in demanding industrial environments.
- Customization Capabilities: We understand that every process is unique. YUANYANG offers extensive customization options, including specific material grades (e.g., SS316L for corrosive media), vacuum capabilities, explosion-proof designs, and various motor powers and blade configurations to perfectly match your application.
- Advanced Control Systems: Our equipment integrates modern VFDs and intuitive control panels, providing precise speed control, energy efficiency, and ease of operation.
- Comprehensive After-Sales Support: YUANYANG is committed to customer satisfaction, offering expert technical consultation, installation support, operator training, and readily available spare parts to ensure your operations run smoothly.
- Industry Expertise: With years of experience serving diverse industries from paints and inks to chemicals and pharmaceuticals, YUANYANG possesses deep application knowledge to guide you in selecting the most effective and efficient disperser solution.
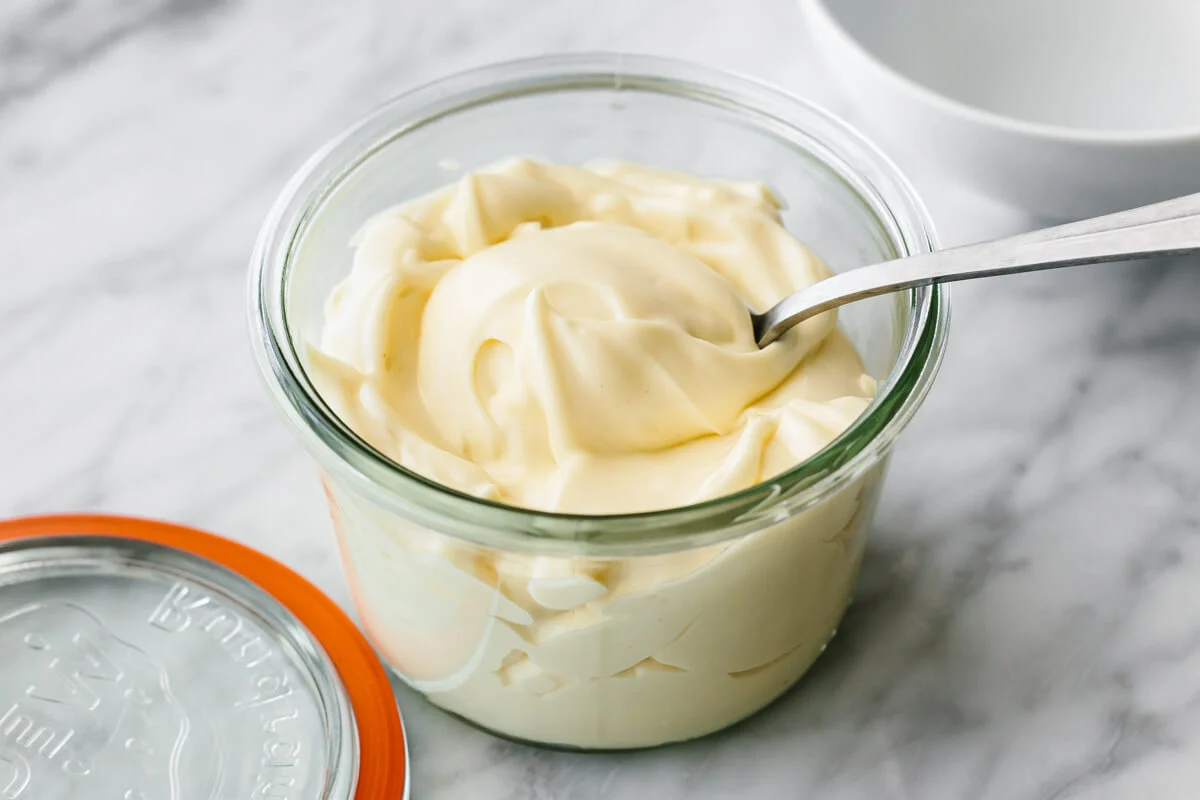
Mayonnaise Manufacturing Process Explained: How Factories Produce Mayonnaise

Water in Oil Emulsion: Meaning, Real-Life Examples, and How to Fix It
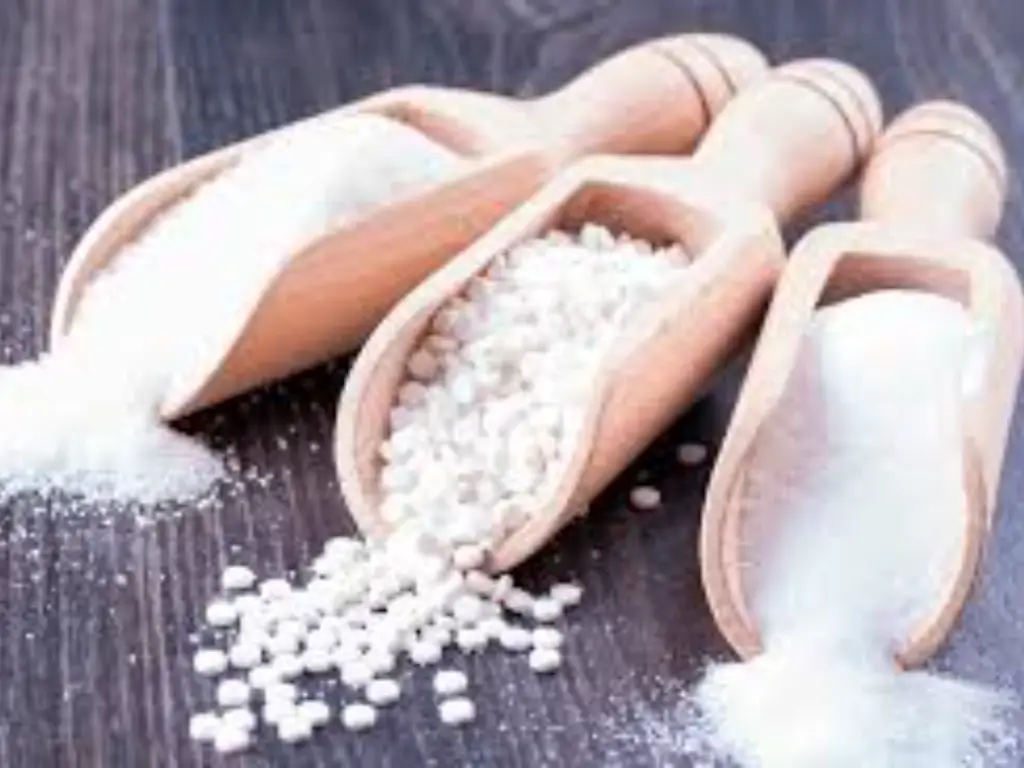
How Artificial Sweeteners Are Made: Inside the Manufacturing Process & Key Equipment
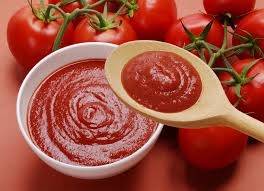
Ketchup Explained: From Ancient Origins to Modern Production Methods
How Lotion Is Made: Step-by-Step Guide for Home and Factory Production
FAQs
What’s your payment term?
Generally, we take 30% of total amount as down payment, which should be wired by T/T. The 70% balance will be paid by T/T after you inspect your machines before shipment. We also accept letter of credit although it takes more expenses. But our bank should confirm your opening bank’s credit first.
Semi Automatic Capping Machine
The capping wheel is a little high for the small bottles, do you have solutions?
Yes, we have designed cylinder type for mini bottles.
What minimum caps size can the desktop capping machine be suit for?
The minimum cap size is 20mm, it is recommend to send caps to test if it is around 20mm.
Industries
What after-sales support services are available?
We offer 7×24-hour online support, regular maintenance, and rapid spare parts supply to ensure the equipment functions smoothly.
Horizontal Filling Machine
What kind of liquids does this liquid bottling machine can fill?
It can fill various liquids products, such shampoo, cream, conditioner, detergent, lotion, sauce, and so on. The materials must be easy to flow down for this cream filler machine. For too viscous paste, pressurized filling machine or hot filling machine will be recommended based on materials. Please send your materials to check.
Leave a message
Have any questions or concerns about our products? Please leave us a message here, and our team will get back to you promptly.
Facebook
YouTube
LinkedIn
Whatsapp: +8613434139712
Guangzhou Yuanyang Machinery