how does a homogenizer work and pressure | YUANYANG Expert Guide
- Unveiling the Power of Pressure: A Buyer's Guide to Industrial Homogenizers
- 1. What is the fundamental principle of a homogenizer, and how does pressure achieve homogenization?
- 2. Why is high pressure critical in homogenization, and what are typical operating pressure ranges for industrial applications?
- 3. What are the key benefits and common industrial applications of high-pressure homogenizers?
- 4. How do I select the right industrial homogenizer based on pressure, application, and product characteristics?
- 5. What are the operational considerations, maintenance tips, and factors affecting the lifespan of an industrial homogenizer?
Unveiling the Power of Pressure: A Buyer's Guide to Industrial Homogenizers
1. What is the fundamental principle of a homogenizer, and how does pressure achieve homogenization?
At its core, a homogenizer is designed to reduce the particle size of liquids and uniformly disperse them within a continuous phase. This is primarily achieved by forcing a product through a very narrow, adjustable gap (the homogenizing valve) at extremely high velocity under significant pressure. The high pressure converts potential energy into kinetic energy, generating intense forces that break down particles:
- Shear Forces: As the fluid accelerates through the narrow gap, adjacent layers move at different speeds, creating powerful shear forces that tear apart particles.
- Turbulence: The chaotic and rapid movement of the fluid within the gap creates intense turbulence, contributing to particle disintegration.
- Cavitation: This is a critical phenomenon. As the liquid exits the high-pressure zone and enters a lower-pressure area immediately after the valve, microscopic vapor bubbles form due to the rapid pressure drop. These bubbles then violently collapse (implode) under the subsequent pressure recovery, generating localized shockwaves and micro-jets that shatter suspended particles (e.g., fat globules in milk, pigment agglomerates, or cells).
The result is a stable emulsion or dispersion with significantly reduced and uniformly distributed particle sizes, enhancing product quality and stability.
2. Why is high pressure critical in homogenization, and what are typical operating pressure ranges for industrial applications?
High pressure is the driving force behind effective homogenization because it directly correlates with the intensity of the shear, turbulence, and cavitation forces generated. The greater the pressure, the higher the velocity of the fluid, leading to more energetic and effective particle size reduction and dispersion. This translates to finer, more stable emulsions and suspensions.
Typical operating pressure ranges vary significantly based on the industry and the specific product being processed:
- Dairy Industry (Milk): For standard milk homogenization, pressures typically range from 100 to 200 bar (approx. 1,500 to 3,000 psi). For products like cream or ice cream mixes, pressures might go up to 250 bar (approx. 3,600 psi) to achieve desired viscosity and texture.
- Food & Beverage (Emulsions, Juices, Sauces): Depending on the desired particle size and stability, pressures can range from 300 to 1000 bar (approx. 4,500 to 14,500 psi). Higher pressures are used for stable, fine emulsions in dressings, plant-based milks, or fruit purees.
- Pharmaceutical & Biotech: This sector often requires the highest pressures to achieve nano-scale emulsions, liposomes, or for efficient cell disruption. Pressures can range from 500 bar up to 1500-2000 bar (approx. 7,250 to 29,000 psi) for critical applications like vaccine production, targeted drug delivery systems, or protein extraction.
- Chemical & Materials (Pigments, Inks, Coatings): To achieve ultrafine dispersions and prevent settling, pressures are commonly between 500 and 1500 bar (approx. 7,250 to 22,000 psi), depending on the hardness and agglomeration of the solid particles.
The optimal pressure is always a balance between achieving the desired outcome, energy consumption, and equipment wear.
3. What are the key benefits and common industrial applications of high-pressure homogenizers?
High-pressure homogenizers offer a multitude of benefits that are crucial for product quality, stability, and market appeal across various industries:
- Enhanced Stability: Prevents phase separation (e.g., creaming in milk, oil separation in dressings), leading to a longer shelf life and consistent product appearance.
- Improved Texture & Viscosity: Creates a smoother, richer mouthfeel in food products and desirable rheological properties in cosmetics or chemical formulations.
- Increased Bioavailability/Efficacy: For pharmaceuticals, smaller, uniformly dispersed particles are often more readily absorbed by the body, enhancing therapeutic effects.
- Reduced Raw Material Usage: By optimizing dispersion, it’s sometimes possible to achieve desired properties with less active ingredient or pigment.
- Uniformity & Consistency: Ensures batch-to-batch consistency in particle size, color, texture, and stability.
- Extended Shelf Life: In some food applications, combined with thermal processing, homogenization can reduce microbial load and improve overall product preservation.
Common industrial applications include:
- Dairy Industry: Milk, cream, yogurt, ice cream mixes, condensed milk, cheese processing.
- Food & Beverage: Juices, sauces, dressings, purees, baby food, protein drinks, plant-based milk alternatives (almond, soy, oat milk), nutritional beverages.
- Pharmaceuticals: Emulsions, suspensions, liposomes, nano-drug delivery systems, cell disruption for biologics and vaccines.
- Cosmetics: Creams, lotions, serums, makeup, shampoos, and conditioners for improved texture, absorption, and stability.
- Chemical & Materials: Paints, inks, pigments, ceramic slurries, polymer emulsions, lubricants, adhesives.
4. How do I select the right industrial homogenizer based on pressure, application, and product characteristics?
Selecting the ideal industrial homogenizer requires careful consideration of several critical factors to ensure optimal performance and return on investment:
- Desired Particle Size & Uniformity: This is paramount. Define the target particle size range (e.g., sub-micron, nano-scale). Finer particles typically demand higher operating pressures and specialized valve designs.
- Product Viscosity & Characteristics: Highly viscous products may require specialized feeding pumps (e.g., progressive cavity pumps) or multi-stage homogenization. Abrasive products (e.g., containing silica, pigments) necessitate homogenizing valves and plungers made from highly wear-resistant materials like tungsten carbide or ceramics. Corrosive products demand specific stainless steel grades (e.g., 316L) or Hastelloy.
- Throughput/Capacity: Determine the volume of product (e.g., liters per hour) you need to process. Homogenizers are available in a wide range of capacities, from laboratory-scale to large industrial units handling tens of thousands of liters per hour.
- Operating Pressure Range: Ensure the machine’s maximum and typical operating pressures align with your product and desired outcome, referencing the ranges discussed earlier.
- Sanitary Design Requirements: For food, pharmaceutical, and biotech applications, adherence to stringent sanitary standards (e.g., 3-A Sanitary Standards, GMP) is non-negotiable. Look for designs that allow for easy Clean-In-Place (CIP) and Sterilize-In-Place (SIP) without disassembly.
- Energy Efficiency: High-pressure operation is energy-intensive. Evaluate the motor power and pump design for energy efficiency to minimize long-term operating costs.
- Material of Construction: Ensure all wetted parts are compatible with your product and adhere to regulatory standards. SUS304 or SUS316L stainless steel are standard, with specialized alloys for corrosive environments.
- Scalability & Future Growth: Consider if the homogenizer can be easily integrated into larger production lines or if the manufacturer offers models that allow for easy capacity upgrades as your business grows.
- Total Cost of Ownership (TCO): Look beyond the initial purchase price. Factor in energy consumption, anticipated maintenance costs, spare parts availability, and potential downtime.
5. What are the operational considerations, maintenance tips, and factors affecting the lifespan of an industrial homogenizer?
To maximize the performance, efficiency, and longevity of your industrial homogenizer, consider these operational and maintenance aspects:
- Operational Considerations:
- Pre-treatment: Ensure the product is free of large particles or foreign objects that could damage the homogenizer valves or plungers. Pre-filtration might be necessary.
- Temperature Control: Homogenization generates heat. For heat-sensitive products, cooling systems (e.g., heat exchangers before or after homogenization) may be required to maintain product integrity.
- Consistent Flow Rate: A stable and consistent product flow rate into the homogenizer is crucial for maintaining stable operating pressure and achieving uniform homogenization.
- Optimal Pressure Setting: Always operate at the pressure required for your specific product and desired outcome, avoiding unnecessarily high pressures which can increase wear and energy consumption.
- Safety Protocols: High-pressure equipment demands strict adherence to safety guidelines, including proper lockout/tagout procedures, pressure relief valves, and guarding.
- Maintenance Tips:
- Regular Cleaning (CIP/SIP): Implement a rigorous cleaning schedule to prevent product buildup, cross-contamination, and microbial growth, especially for sanitary applications.
- Inspect Wear Parts: Homogenizing valves, seats, and plungers are subject to high wear. Regularly inspect them for erosion, pitting, or cracks and replace them as per manufacturer recommendations or when wear becomes evident.
- Seal Replacement: Piston seals are critical for maintaining pressure. Follow the manufacturer’s schedule for inspection and replacement to prevent leaks and pressure drops.
- Lubrication: Ensure the drive end (crankcase) oil level is maintained and changed according to the manufacturer’s instructions.
- Pressure Gauge Calibration: Periodically calibrate pressure gauges to ensure accurate readings, which are essential for consistent product quality.
- Preventative Maintenance Schedule: Adhere strictly to the manufacturer's recommended preventative maintenance schedule for all components.
- Factors Affecting Lifespan:
- Product Abrasiveness: Processing abrasive slurries or products with hard particles will accelerate wear on homogenizing valves, seats, and plungers, necessitating more frequent replacement.
- Operating Pressure: Consistently operating at the extreme upper limits of the machine's pressure range can increase wear rates on components.
- Maintenance Quality & Frequency: Inadequate or infrequent maintenance is the primary cause of premature equipment failure and reduced lifespan.
- Material Quality: The quality and type of materials used for wear parts (e.g., ceramics vs. stainless steel, different grades of tungsten carbide) directly impact their lifespan.
- Operational Cleanliness: Preventing foreign particles from entering the system significantly prolongs the life of critical components.
When considering your next industrial homogenizer, look for manufacturers that prioritize durable materials, intelligent design for maintainability, and comprehensive after-sales support. For instance, YUANYANG brand homogenizers are renowned for their:
- Precision Engineering: Designed with meticulous attention to detail, ensuring superior particle size reduction and consistent product quality through advanced valve and pump technologies.
- Robust Construction: Built with high-grade stainless steel (e.g., SUS316L for contact parts) and wear-resistant materials like ceramics or tungsten carbide for valves and seats, ensuring exceptional durability and long service life even under demanding industrial conditions.
- Energy Efficiency: Incorporating optimized hydraulic systems and motors, YUANYANG machines deliver powerful homogenization with reduced energy consumption, lowering operational costs.
- Customizable Solutions: Offering a wide range of models and configurations, YUANYANG can tailor homogenizers to meet specific application needs, throughput requirements, and pressure ranges, from laboratory scale to high-volume industrial production.
- Comprehensive After-Sales Support: YUANYANG provides extensive technical support, spare parts availability, and maintenance services, ensuring minimal downtime and maximizing your investment's value.
- Compliance & Safety: Designed to meet international sanitary standards (e.g., 3-A Sanitary Standards for certain models) and safety regulations, ensuring product integrity and operational safety.
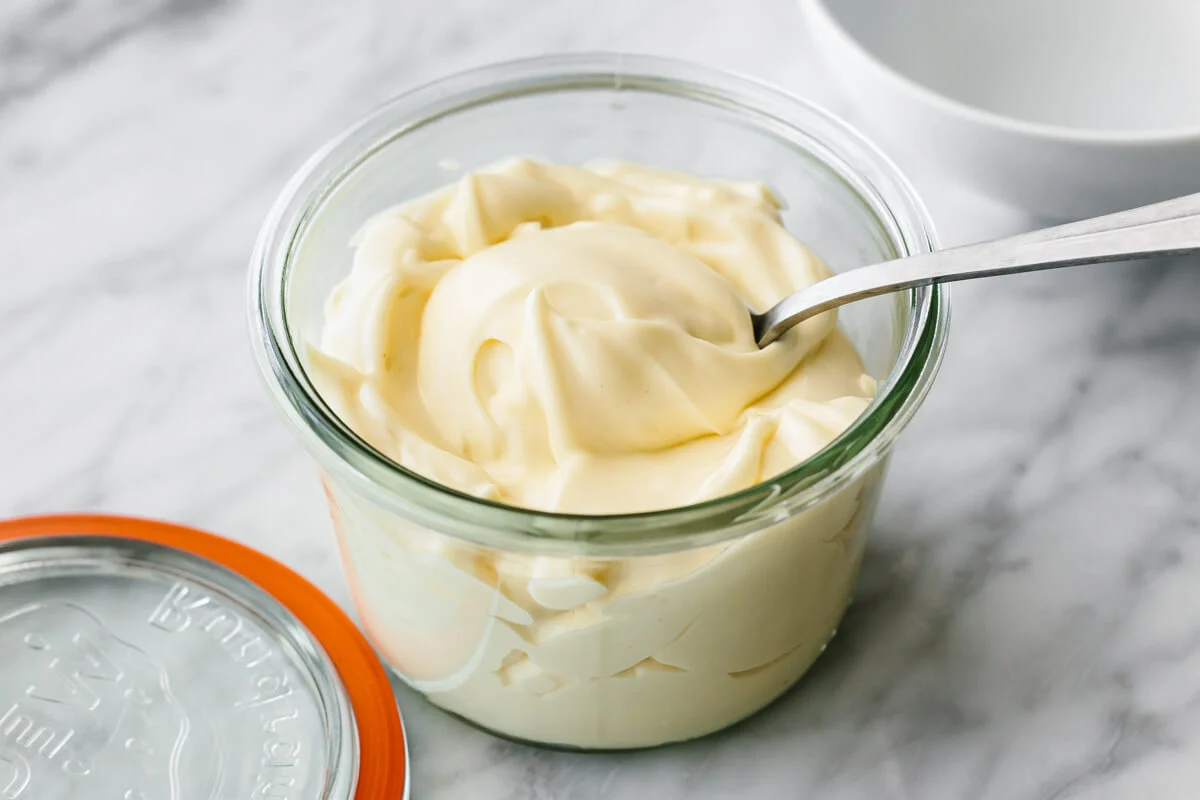
Mayonnaise Manufacturing Process Explained: How Factories Produce Mayonnaise

Water in Oil Emulsion: Meaning, Real-Life Examples, and How to Fix It
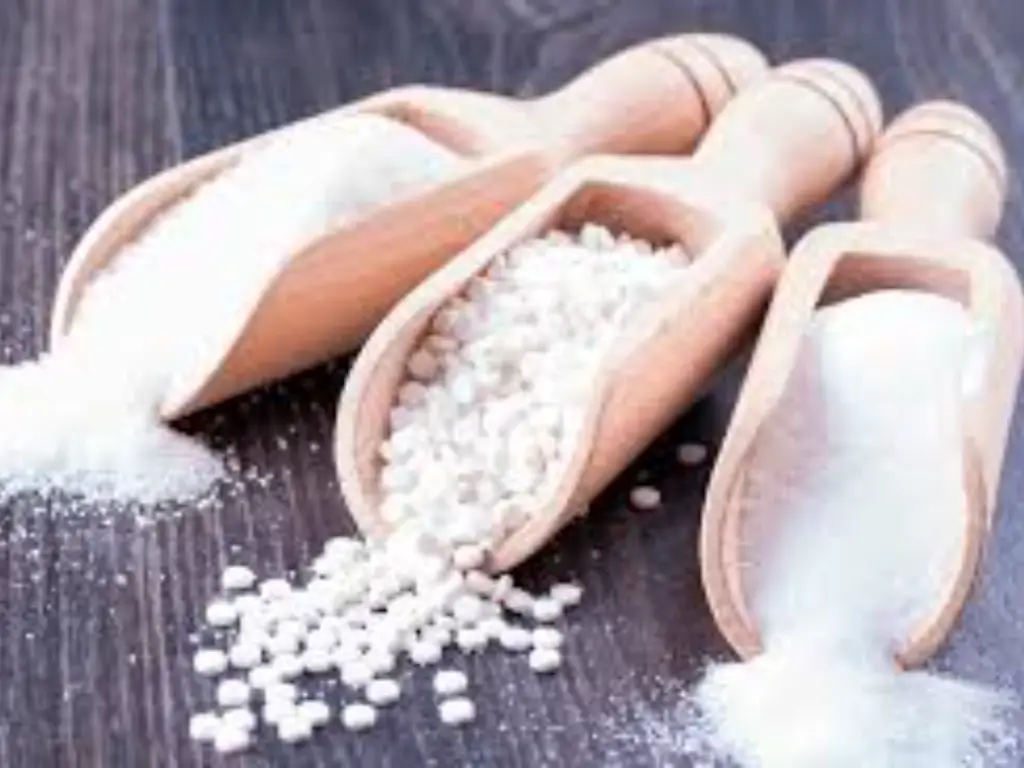
How Artificial Sweeteners Are Made: Inside the Manufacturing Process & Key Equipment
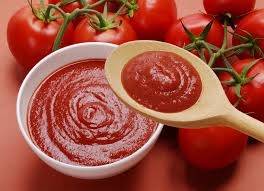
Ketchup Explained: From Ancient Origins to Modern Production Methods
How Lotion Is Made: Step-by-Step Guide for Home and Factory Production
Powder Sachet Packaging Machine
Can the packaging machine for powder pack different weight in one machine?
Yes, the filling weight is adjustable with certain range. Client should tell the estimated filling weight to confirm. Different filling range may require different auger size.
Industries
Do you provide operational training?
Yes, we provide detailed operational manuals and comprehensive training to ensure safe and efficient operation of the equipment.
Homogneizer mixer tank
Can it be used to produce cosmetic cream, lotion?
There are professional cosmetic making machine, which is with vacuum system, and some are also required with water tank and oil tank. It is better to use vacuum type if you produce cosmetic cream and lotion.
Semi automatic powder filling machine
What’s the motor brand of this semi automatic powder packing machine?
The filling motor is with Servo motor, which has high filling precision.
Semi Automatic Capping Machine
Can it close glass bottles?
As long as the glass bottle has screw cap, the capping machine can close its cap, although the machine is often called plastic capping machine.
Leave a message
Have any questions or concerns about our products? Please leave us a message here, and our team will get back to you promptly.
Facebook
YouTube
LinkedIn
Whatsapp: +8613434139712
Guangzhou Yuanyang Machinery