how packing machine works | YUANYANG Expert Guide
- Demystifying Packing Machines: Essential Knowledge for Industrial Mixer Professionals
- What are the Fundamental Principles and Types of Packing Machines?
- How Do Packing Machines Seamlessly Integrate with Industrial Mixing Lines?
- What are the Key Benefits of Automating Packaging with These Machines?
- What Factors Should Industrial Mixer Users Consider When Selecting a Packing Machine?
- How Do Modern Packing Machines Ensure Precision, Hygiene, and Sustainability?
Demystifying Packing Machines: Essential Knowledge for Industrial Mixer Professionals
You've mastered the art of mixing. Your industrial mixers produce perfect batches consistently. But what happens next? The journey from a well-blended product to a market-ready package is where packing machines become indispensable. For professionals in the industrial mixing sector, understanding 'how packing machine works' isn't just about curiosity; it's about optimizing your entire production line, ensuring product integrity, and maximizing efficiency. This article delves into the core mechanics and critical considerations of packing machines, offering insights crucial for your next procurement decision.
What are the Fundamental Principles and Types of Packing Machines?
At their core, packing machines automate the process of preparing products for distribution. Their fundamental principles involve precise dispensing (filling), securing (sealing), and presentation (labeling, boxing). The basic automation cycle typically includes product feeding, accurate filling, reliable sealing, and efficient discharge.
Various types of packing machines cater to diverse product forms and packaging needs:
- Form-Fill-Seal (FFS) Machines: Create, fill, and seal pouches or bags from a roll of film. Vertical FFS (VFFS) is common for powders and granules (like dry mixes), while Horizontal FFS (HFFS) is often used for individual items or solid products.
- Cartoning Machines: Erect, fill, and seal cartons, ideal for boxing finished products or multiple smaller packages.
- Bottling and Capping Lines: Specialized for filling liquids, pastes, or powders into bottles and applying caps.
- Vacuum Packaging Machines: Remove air to extend shelf life, particularly for food products.
- Palletizers: End-of-line machines that automatically stack packaged products onto pallets for shipping.
For products emerging from industrial mixers – whether powders, granules, viscous pastes, or liquids – understanding these diverse methods is key to selecting a machine compatible with your product's post-mixing physical state and desired packaging format.
How Do Packing Machines Seamlessly Integrate with Industrial Mixing Lines?
Effective integration between your mixing operation and the packaging line is paramount for a smooth, efficient production flow. Products typically move from the mixer's discharge point – via conveyors, pumps, or gravity – into the packing machine's infeed system.
Synchronization is critical. Advanced control systems, often using Programmable Logic Controllers (PLCs) and an array of sensors, ensure that the packing machine's speed matches the mixer's output, preventing bottlenecks or product starvation. Buffer systems, such as intermediate hoppers or accumulators, can be employed to manage variations in flow between batch mixing and continuous packaging operations.
Seamless integration can lead to a 20-30% reduction in manual handling and a significant decrease in product spillage, which is crucial for maintaining Good Manufacturing Practices (GMP) standards, especially in pharmaceutical and food industries.
What are the Key Benefits of Automating Packaging with These Machines?
Automating your packaging process offers substantial advantages that directly impact your bottom line and product quality:
- Increased Efficiency and Throughput: Automated systems can achieve fill rates of hundreds per minute, far exceeding manual capabilities, leading to throughput increases of over 50% for many operations. This enables higher production volumes and faster time to market.
- Reduced Operational Costs: Industry reports show automated packaging can cut labor costs by up to 70% in high-volume settings. Furthermore, precise filling minimizes product giveaway, reducing material waste and improving profitability.
- Enhanced Accuracy and Consistency: Modern gravimetric and volumetric fillers ensure accuracy within ±0.5% for consistent product weight and fill levels. This uniformity improves brand consistency and customer satisfaction.
- Improved Hygiene and Safety: By minimizing human contact, automated systems reduce the risk of contamination, crucial for food, pharmaceutical, and cosmetic products. Compliance with HACCP and GMP guidelines is significantly enhanced with enclosed, automated systems.
The global packaging machinery market is expected to grow at a CAGR of 4-6% from 2023 to 2028, a clear indicator of the increasing adoption and recognized benefits of automation across industries.
What Factors Should Industrial Mixer Users Consider When Selecting a Packing Machine?
When it's time to procure or upgrade your packing machine, a systematic approach is vital. Consider the following factors, especially in relation to your mixed product:
- Product Characteristics: The viscosity, density, particle size, and flowability of your mixed product (e.g., fine powder, granular material, thick paste, liquid) will dictate the type of filling mechanism required (e.g., auger filler, piston filler, gravimetric filler).
- Packaging Type and Material: Will your product go into bags, bottles, cartons, or pouches? What material will be used (e.g., plastic film, glass, aluminum, paper)? The machine must be compatible with your chosen packaging.
- Throughput Requirements: The packing machine's capacity must align with or exceed your industrial mixer's output to avoid bottlenecks. Calculate your required output in units per minute/hour.
- Level of Automation: Do you need a semi-automatic machine for lower volumes and more flexibility, or a fully automatic, high-speed solution for continuous production?
- Footprint and Scalability: Assess available factory space. Consider if the machine can be integrated into your current layout and if it offers modularity for future expansion.
- Hygiene and Material Compatibility: For pharmaceutical or food-grade applications, ensure contact parts are made of high-grade stainless steel (e.g., SS304 or SS316L) and adhere to regulatory standards like FDA, USDA, or GMP.
- Budget and ROI: Balance the initial investment cost with the long-term savings in labor, material waste, and increased throughput.
- After-Sales Support and Spare Parts: Reliable technical support, readily available spare parts, and comprehensive training are crucial for minimizing downtime.
How Do Modern Packing Machines Ensure Precision, Hygiene, and Sustainability?
Modern packing machines are designed with advanced features to meet stringent industry demands:
- Precision: Achieved through sophisticated technologies like servo motors for exact motion control, high-resolution load cells for gravimetric filling, and vision systems for quality control and labeling accuracy. PLC programming ensures repeatable and precise processes, with accuracy levels often within ±0.5% for fill weights.
- Hygiene: Designed with easy-to-clean surfaces, Quick-Change-Over (QCO) parts, and often Clean-In-Place (CIP) capabilities for liquid lines. The extensive use of food-grade materials (like SS304/SS316L for all product contact surfaces) and minimized human intervention significantly reduce contamination risks, aligning with strict regulatory frameworks.
- Sustainability: The drive for environmental responsibility influences machine design. This includes:
- Material Efficiency: Optimizing film usage and minimizing trim waste.
- Energy Efficiency: Incorporating energy-saving servo motors and optimized control systems, potentially reducing energy consumption by 15-20% compared to older models.
- Waste Reduction: Precise filling minimizes product giveaway. Machines are increasingly designed to handle thinner films and recyclable or compostable packaging materials, reflecting the global trend where over 60% of consumers prefer sustainable packaging options.
Conclusion: YUANYANG's Advantage
While YUANYANG excels in delivering state-of-the-art industrial mixers, our understanding of the complete production cycle, including downstream packaging, sets us apart. YUANYANG's expertise ensures that our mixers provide products perfectly prepared and ready for seamless integration with modern packing machinery. We focus on robust design, consistent performance, and customized mixing solutions that optimize your overall line efficiency, from product formulation to packing readiness. By partnering with YUANYANG, you invest in a partner who understands the entire value chain, helping you achieve superior product quality and operational excellence for every batch.
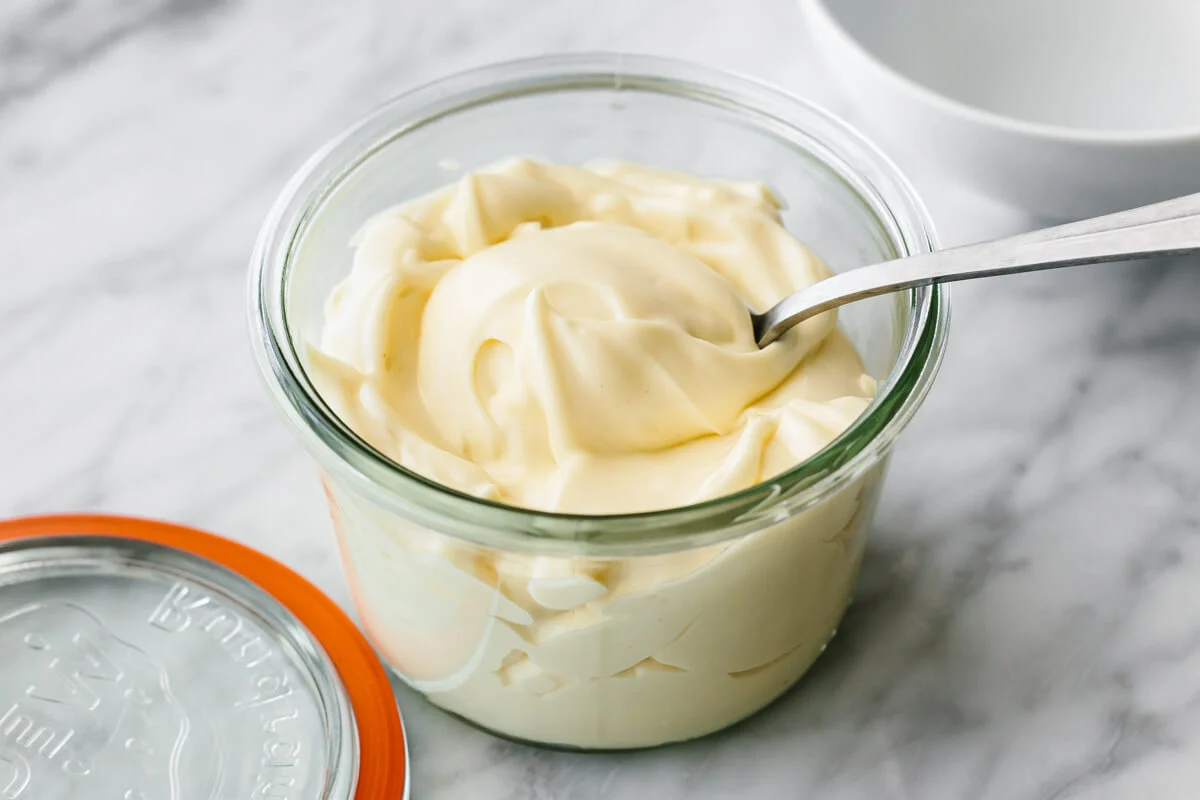
Mayonnaise Manufacturing Process Explained: How Factories Produce Mayonnaise

Water in Oil Emulsion: Meaning, Real-Life Examples, and How to Fix It
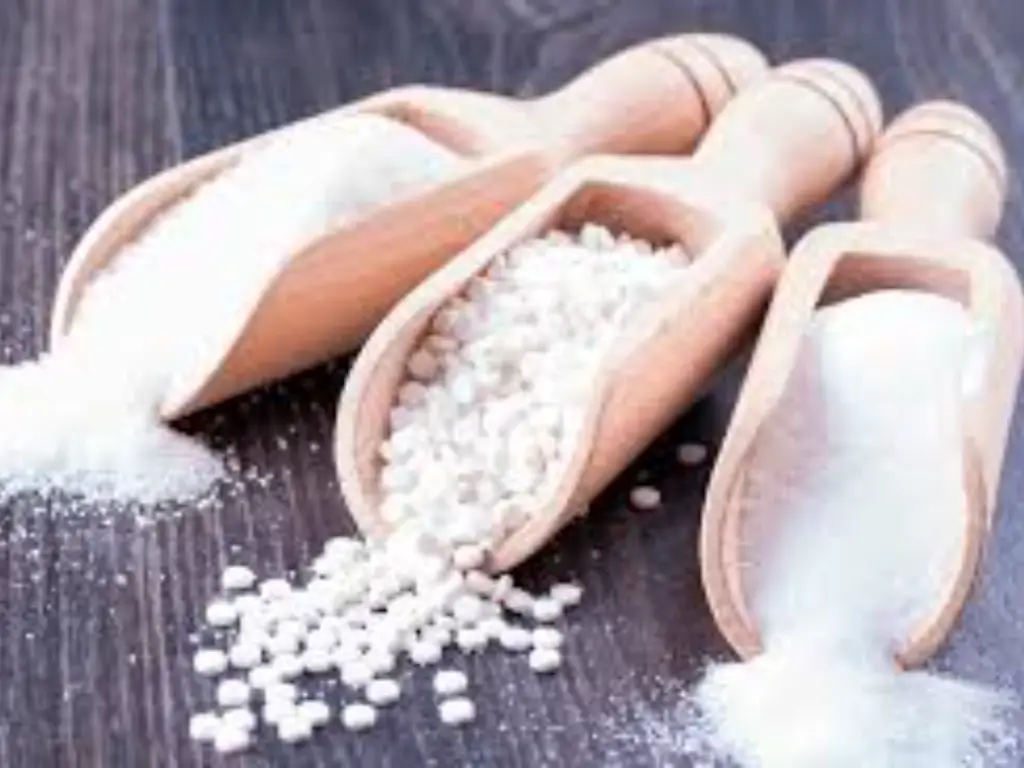
How Artificial Sweeteners Are Made: Inside the Manufacturing Process & Key Equipment
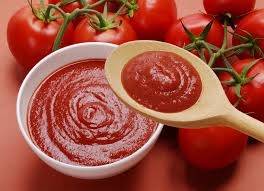
Ketchup Explained: From Ancient Origins to Modern Production Methods
How Lotion Is Made: Step-by-Step Guide for Home and Factory Production
Automatic Servo Motor Capping Machine
Can rotation speed of the bottle separator be controlled for this servo capper machine?
The speed to separate bottles can be controlled with frequency converter on the electric cabinet.
FAQs
How is the quality?
We provide high-standard equipment. Quality is priority. People from Yuany always attach great importance to quality control from the beginning to the end. We support production inspection before shipment. And all machines will be tested and send you videos. You can also send your own packages/materials for rest-run after the machines are finished. Our factory has gained GMP,ISO,and CE Certificates.
Water Filling Machine
What liquid is it suitable for ?
No, this is water filling machine, only suitable for liquids like water, drinks, milk, perfume, eye drops...
Detergent powder mixer
Do you also supply the complete powder production line machines?
Yes, we provide a solution including: powder feeding machine, powder mixing machine, and powder packing machine which will be recommended according to how client plans to pack the powder.
High shear homogneizer
Can the working head parts be dismountable?
Yes, the homogenizer head is dismountable. If there is any problem of the working head, just disassemble it and check. Videos is provided.
Leave a message
Have any questions or concerns about our products? Please leave us a message here, and our team will get back to you promptly.
Facebook
YouTube
LinkedIn
Whatsapp: +8613434139712
Guangzhou Yuanyang Machinery