What is the purpose of the vibrating machine? | YUANYANG Expert Guide
- Unveiling the Role of Vibrating Machines in Advanced Industrial Mixing
- 1. What is the Primary Purpose of a Vibrating Machine in Industrial Mixing?
- 2. How Do Vibrating Screens Enhance Product Quality and Production Efficiency in Mixing Operations?
- 3. What are the Different Types of Vibrating Machines Used with Industrial Mixers, and How Do They Differ?
- 4. What Factors Should Be Considered When Integrating a Vibrating Machine into an Existing Mixing Line?
- 5. What Are the Maintenance and Operational Best Practices for Vibrating Machines to Ensure Longevity and Performance?
- YUANYANG's Advantage in Vibrating Separation Technology
Unveiling the Role of Vibrating Machines in Advanced Industrial Mixing
In the realm of industrial mixing, achieving a perfectly homogenous blend is often just one piece of the puzzle. The subsequent, and equally critical, step involves ensuring the purity, consistency, and desired particle size of the final product. This is where vibrating machines, often overlooked but indispensable, play a pivotal role. For professionals in the industrial mixer sector considering a new purchase or system upgrade, understanding the purpose and benefits of these machines is paramount to optimizing their production lines.
1. What is the Primary Purpose of a Vibrating Machine in Industrial Mixing?
The primary purpose of a vibrating machine in an industrial mixing context is to perform a range of crucial separation and classification tasks post-mixing or even during certain pre-mixing stages. These machines, commonly known as vibratory screeners, sieves, or separators, are designed to:
- Remove Oversize & Undersize Particles: Ensure that the mixed product adheres to a specific particle size distribution by separating larger foreign materials (e.g., packaging debris, unmixed agglomerates) or finer dust.
- De-agglomeration: Break down soft lumps or agglomerates formed during mixing, ensuring a free-flowing, uniform powder.
- Product Classification/Grading: Sort mixed materials into multiple fractions based on their particle size, crucial for products requiring precise specifications.
- Quality Control & Contamination Removal: Act as a final check to remove any foreign contaminants that might have inadvertently entered the product stream, ensuring product safety and integrity, especially critical in food, pharmaceutical, and chemical industries.
- Improving Flowability: By ensuring uniform particle size and removing impurities, vibrating machines enhance the flow characteristics of powders, preventing bridging and rat-holing in subsequent processing equipment.
2. How Do Vibrating Screens Enhance Product Quality and Production Efficiency in Mixing Operations?
Integrating a vibrating screen into your mixing line yields significant improvements in both product quality and operational efficiency:
- Enhanced Product Purity: By effectively removing foreign objects, unwanted lumps, and off-spec particles, vibrating screens guarantee a cleaner, purer end product. This is vital for meeting stringent industry standards (e.g., FDA regulations for food and pharmaceuticals) and consumer expectations.
- Consistent Particle Size Distribution: Achieves a more uniform product, which is essential for consistent performance in subsequent processes like tableting, coating, or packaging, and for ensuring consistent dissolution rates or bioavailability in pharmaceutical products.
- Reduced Rework and Waste: Preventing oversized particles from entering downstream processes reduces blockages, equipment wear, and the need for costly rework, thereby minimizing material waste and improving yield.
- Increased Throughput: By maintaining consistent material flow and preventing clogs, vibratory screeners allow the mixing and subsequent processing equipment to operate at optimal capacity, boosting overall production throughput. Many industrial users report throughput increases of 15-30% by integrating efficient screening solutions.
- Cost Savings: Longevity of downstream equipment is improved due to the absence of abrasive foreign particles. Furthermore, reduced product recalls and improved customer satisfaction contribute to long-term financial benefits.
3. What are the Different Types of Vibrating Machines Used with Industrial Mixers, and How Do They Differ?
The selection of a vibrating machine largely depends on the material characteristics, required capacity, and desired separation fineness. Common types include:
- Circular Vibratory Separators/Sieves: The most common type, they use a multi-plane vibratory motion generated by eccentric weights on the motor shaft. They are highly versatile, compact, and efficient for screening powders, granules, and slurries across various industries. They can classify materials into multiple fractions (up to 5 different sizes) simultaneously.
- Rectangular/Linear Vibrating Screens: These machines use a linear vibratory motion and are often preferred for high-capacity applications involving coarser materials, such as minerals, aggregates, or large-volume chemical powders. Their large screening area allows for higher throughput.
- Tumbler Screeners: Offering a gentle, three-dimensional motion, tumbler screeners are ideal for very fine, sensitive, or abrasive powders. They provide high screening accuracy and efficiency, often used in pharmaceutical, food, and fine chemical applications where particle sizes can be as small as 20-50 microns.
- Ultrasonic Vibrating Screens: These screens integrate an ultrasonic transducer that vibrates the mesh at high frequencies (e.g., 36 kHz). This innovation prevents blinding (clogging) of the mesh when handling extremely fine, sticky, or electrostatically charged powders, dramatically increasing screening efficiency and reducing downtime.
4. What Factors Should Be Considered When Integrating a Vibrating Machine into an Existing Mixing Line?
When re-purchasing or integrating a new vibrating machine, several critical factors must be evaluated to ensure seamless operation and optimal performance:
- Material Characteristics: Consider the material's bulk density, abrasiveness, moisture content, temperature, and flow properties. For instance, highly abrasive materials might require screens made of wear-resistant alloys, while sticky materials might need ultrasonic systems.
- Required Capacity & Separation Fineness: Determine the desired throughput (e.g., kg/hour or tons/hour) and the specific mesh sizes (e.g., 20 mesh for coarse separation, 325 mesh for fine powders) needed to achieve the target particle size distribution. This directly impacts the screen's size and number of decks.
- Space & Layout Constraints: Assess the available floor space and height in your facility to ensure the selected machine fits within the existing layout and integrates smoothly with upstream (mixer discharge) and downstream (packaging, storage) equipment.
- Sanitation & Compliance: For hygienic industries (food, pharma), prioritize machines constructed from food-grade stainless steel (e.g., SS304 or SS316L), with easy-to-clean designs, minimal dead spots, and adherence to GMP (Good Manufacturing Practice) standards.
- Energy Consumption & Noise Levels: Evaluate the power requirements and consider models with energy-efficient motors. Also, assess noise levels to ensure they comply with workplace safety regulations and do not disrupt the working environment.
- Automation & Integration Capabilities: Consider how easily the vibrating machine can be integrated into your existing control systems for automated operation, data logging, and remote monitoring.
5. What Are the Maintenance and Operational Best Practices for Vibrating Machines to Ensure Longevity and Performance?
To maximize the lifespan and efficiency of your vibrating machine, adhere to these best practices:
- Regular Inspection of Screen Media: Periodically check the mesh for tears, blockages, or wear. Worn screens lead to inefficient separation and potential product contamination. Screen replacement frequency varies but can range from every few weeks for highly abrasive materials to annually for less demanding applications.
- Motor and Bearing Checks: Inspect the vibratory motor for unusual noises or vibrations. Ensure bearings are properly lubricated (if applicable) and check for overheating. Over time, bearings can degrade, leading to reduced performance and potential motor failure.
- Spring & Suspension System Maintenance: The springs or rubber isolators absorb vibrations and ensure efficient energy transfer to the screen. Check them for cracks, fatigue, or breakage and replace as needed.
- Cleaning Protocols: Implement regular and thorough cleaning routines, especially for machines handling sticky or hygroscopic materials, to prevent material buildup and ensure consistent performance. For hygienic applications, CIP (Clean-In-Place) capabilities can be a significant advantage.
- Proper Tensioning: Ensure the screen media is correctly tensioned. Improper tension can lead to premature wear, reduced screening efficiency, and even damage to the machine frame.
- Operator Training: Ensure that operators are well-trained in machine operation, troubleshooting, and routine maintenance tasks. Proper operation minimizes wear and tear and maximizes efficiency.
- Preventive Maintenance Schedule: Establish a comprehensive preventive maintenance schedule based on manufacturer recommendations and operational hours to proactively address potential issues before they lead to costly downtime.
YUANYANG's Advantage in Vibrating Separation Technology
When considering a reliable partner for your industrial mixing and separation needs, YUANYANG stands out. With decades of expertise, YUANYANG offers robust and highly efficient vibrating machines tailored to diverse industry requirements. Our key advantages include:
- Customization Capabilities: YUANYANG understands that every application is unique. We provide bespoke solutions, designing and manufacturing vibrating screens that perfectly integrate with your existing mixing lines and meet specific capacity, fineness, and material handling needs.
- Superior Construction & Durability: Our machines are built with high-quality, durable materials, including pharmaceutical-grade stainless steel (SS304/SS316L), ensuring longevity, minimal maintenance, and compliance with international standards like CE and ISO.
- High Efficiency & Precision: YUANYANG vibratory separators are engineered for optimal separation efficiency, ensuring consistent product quality and maximum throughput, even for challenging materials like ultra-fine powders or viscous slurries.
- Comprehensive After-Sales Support: We provide extensive technical support, spare parts availability, and maintenance guidance, ensuring your YUANYANG equipment operates at peak performance throughout its lifecycle.
- Versatile Applications: From food processing and pharmaceuticals to chemicals, ceramics, and metallurgy, YUANYANG vibrating machines are trusted across various industries for their reliability and performance.
Investing in a high-quality vibrating machine from YUANYANG is not just a purchase; it's an investment in the enhanced quality, efficiency, and profitability of your industrial mixing operations.
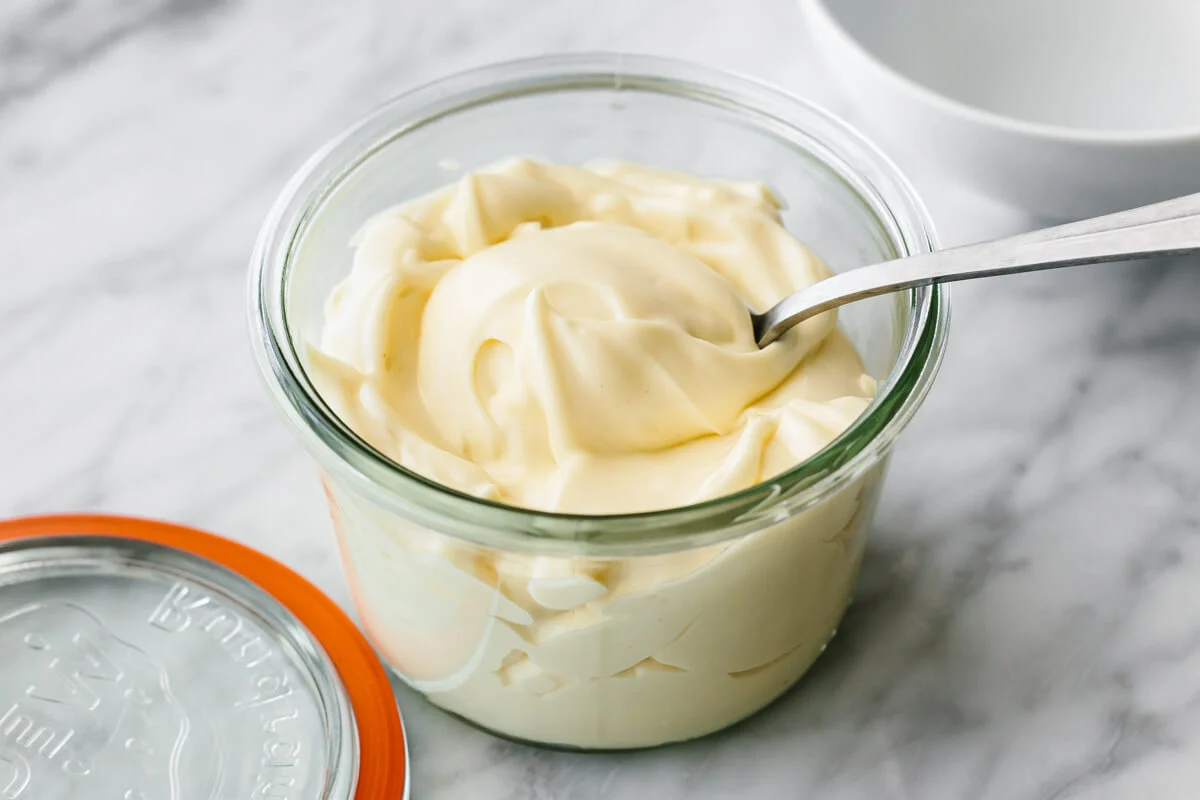
Mayonnaise Manufacturing Process Explained: How Factories Produce Mayonnaise

Water in Oil Emulsion: Meaning, Real-Life Examples, and How to Fix It
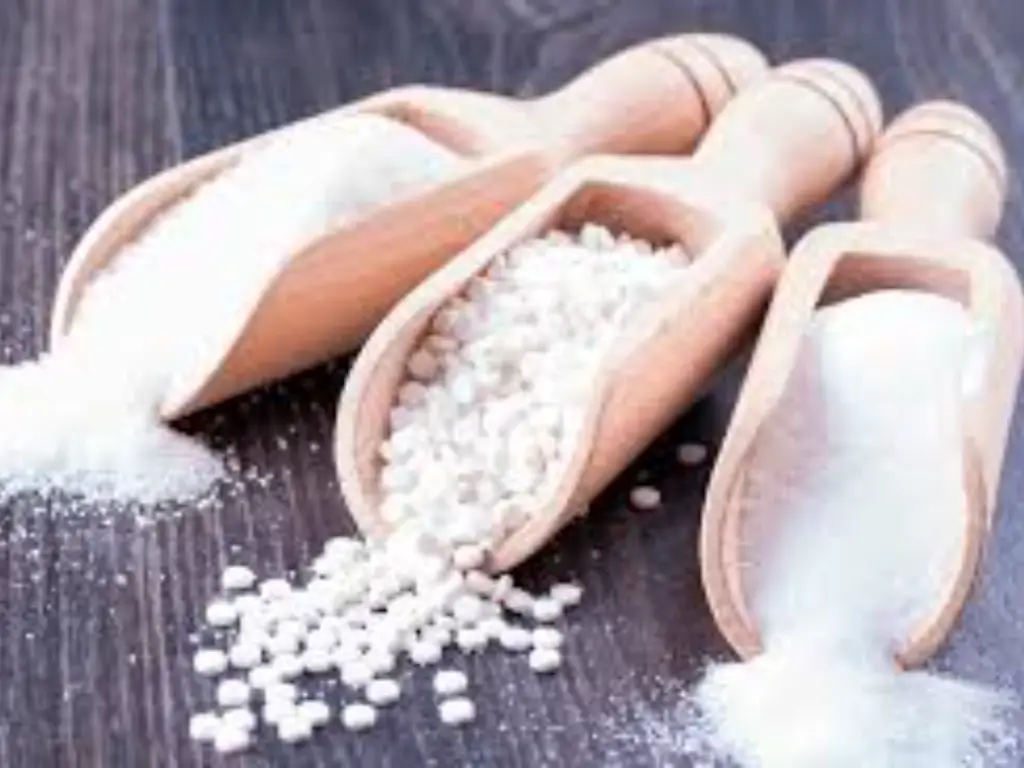
How Artificial Sweeteners Are Made: Inside the Manufacturing Process & Key Equipment
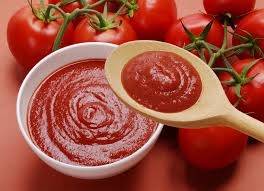
Ketchup Explained: From Ancient Origins to Modern Production Methods
How Lotion Is Made: Step-by-Step Guide for Home and Factory Production
Homogenizer Mixing Tank with Circulation System
I don’t need homogenizer, can you reduce it?
Yes, the homogenizer is an optional function, whether clients need it depends on your own products.
Do you have a water pump with flow meter installed for the shampoo mixer machine?
Yes, water pump with flow meter can be added upon requirements.
Water Cooling Induction Sealer
What’s the purpose of sealing the packages?
Automated sealing machine has high sealing effect, which can ensure the hygiene and safety of the food, extend the shelf life of the food, to prevent chemical reactions or deterioration, to avoid the leakage and pollution of drugs.
Water Filling Machine
What liquid is it suitable for ?
No, this is water filling machine, only suitable for liquids like water, drinks, milk, perfume, eye drops...
Horizontal Filling Machine
How long is the suction hose?
This hose is about 1.3 meters long. Can be longer upon requirements.
Leave a message
Have any questions or concerns about our products? Please leave us a message here, and our team will get back to you promptly.
Facebook
YouTube
LinkedIn
Whatsapp: +8613434139712
Guangzhou Yuanyang Machinery