how to operate homogenizer | YUANYANG Expert Guide
- Operating Your Industrial Homogenizer: A Comprehensive Guide for Procurement and Performance
- 1. Essential Startup and Operation Procedures
- 2. Prioritizing Safety: Key Homogenizer Safety Protocols
- 3. Troubleshooting Common Homogenizer Issues
- 4. Maintaining Your Homogenizer for Peak Efficiency
- 5. Selecting the Right Homogenizer for Your Industrial Needs
Operating Your Industrial Homogenizer: A Comprehensive Guide for Procurement and Performance
Industrial homogenizers are critical assets in various sectors, from food and beverage to pharmaceuticals and chemicals, ensuring product consistency, stability, and quality. Proper operation and maintenance are paramount not only for peak performance but also for the longevity of the equipment and safety of personnel. This guide addresses common questions industrial users have, aiding both current operators and those in the procurement phase.
1. Essential Startup and Operation Procedures
Starting an industrial homogenizer requires a systematic approach. First, ensure all utility connections – power, water (for cooling/CIP), and compressed air – are secure and within specified parameters. The feed product tank should be filled, and the inlet line primed to prevent cavitation upon startup. Before engaging the main pump, check that all valves are correctly positioned for the intended flow path. Gradually increase the pump speed or pressure setting, monitoring the gauge until the desired homogenization pressure is reached. For example, dairy applications often operate between 1500-2500 psi for milk, while some emulsions may require pressures exceeding 10,000 psi. Throughout operation, continuously monitor flow rates, pressures, and temperatures. Any significant fluctuations can indicate issues such as air ingress or blockages. Always follow the manufacturer's specific sequence for shutdown, typically involving reducing pressure gradually before turning off the pump and isolating the system.
2. Prioritizing Safety: Key Homogenizer Safety Protocols
Safety is non-negotiable when operating high-pressure industrial equipment. Personal Protective Equipment (PPE) is mandatory and includes safety glasses, hearing protection, gloves, and appropriate footwear. Always verify that all safety guards are in place and interlocks are functional before operation. Implement strict Lockout/Tagout (LOTO) procedures during maintenance or cleaning to prevent accidental startup. Be acutely aware of potential hazards such as high-pressure fluid leaks, which can cause severe injury, and rotating machinery. Ensure emergency stop buttons are easily accessible and functional. Proper ventilation is crucial, especially when processing volatile chemicals or during CIP (Clean-in-Place) cycles involving harsh cleaning agents. Training on chemical handling and spill containment is also essential.
3. Troubleshooting Common Homogenizer Issues
Even with proper operation, issues can arise. Common problems include pressure fluctuations, unusual noise, and inconsistent product quality. If pressure fluctuates significantly, check for air in the feed line, clogged inlet filters, or worn homogenization valves/seats. A knocking or loud noise might indicate cavitation due to insufficient feed pressure, worn pump plungers, or bearing issues. If product quality (e.g., particle size, stability) is inconsistent, verify the set pressure, ensure the product is within the recommended temperature range, and inspect the homogenization valve for wear or foreign material. Regular inspection of wear parts, such as valve seats, plungers, and seals, against manufacturer specifications is key to proactive troubleshooting. For instance, a small scratch on a ceramic valve can drastically reduce homogenization efficiency.
4. Maintaining Your Homogenizer for Peak Efficiency
Preventive maintenance is vital for extending the lifespan and ensuring the continuous high performance of your homogenizer. Daily routines should include external cleaning and checking for leaks. Weekly or bi-weekly tasks often involve inspecting seals, gaskets, and plungers for wear and tear, and checking oil levels in the gearbox. Monthly or quarterly checks might include changing lubrication oil, inspecting valve seats and impact rings, and checking belt tension. Annually, a more comprehensive overhaul, including replacement of critical wear parts, checking electrical connections, and calibration of pressure gauges, is recommended. Adhering to the manufacturer's recommended maintenance schedule and using genuine replacement parts are crucial. For example, a worn valve can lead to significant energy waste and reduced product quality.
5. Selecting the Right Homogenizer for Your Industrial Needs
When procuring an industrial homogenizer, several factors must be considered to ensure it aligns with your operational requirements. Key considerations include: Application Type: Food (dairy, juice, sauces), pharmaceutical (emulsions, suspensions, liposomes), chemical (paints, inks), or cosmetic. Each application has specific material compatibility and sanitary requirements. Desired Particle Size and Stability: This dictates the required operating pressure and valve design. For example, liposomal encapsulation might require pressures exceeding 20,000 psi for nanoscale particles. Throughput: Match the homogenizer's capacity (LPH or GPH) to your production volume. Product Viscosity and Abrasiveness: High viscosity or abrasive products require robust pump designs and wear-resistant materials. Sanitary Requirements: For food and pharma, CIP/SIP (Clean-in-Place/Sterilize-in-Place) capabilities, hygienic design, and material traceability are critical. Energy Efficiency: Look for models with optimized pump designs and variable frequency drives (VFDs) to reduce operational costs. Automation and Controls: Integration with existing plant control systems (e.g., PLC) can enhance efficiency and reduce manual intervention. According to recent industry reports, the global industrial homogenizer market is projected to grow, driven by increasing demand for stable emulsions and dispersions across various sectors, with a strong emphasis on customizable, energy-efficient, and easy-to-maintain solutions.
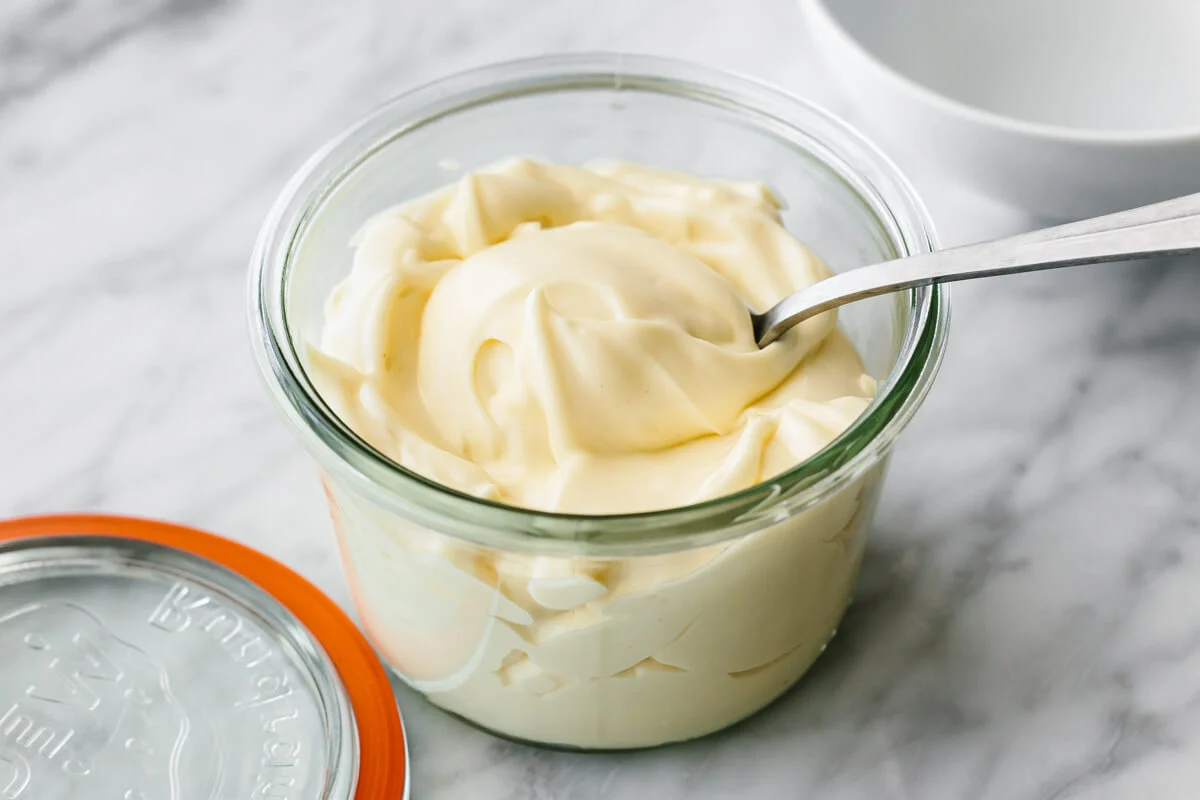
Mayonnaise Manufacturing Process Explained: How Factories Produce Mayonnaise

Water in Oil Emulsion: Meaning, Real-Life Examples, and How to Fix It
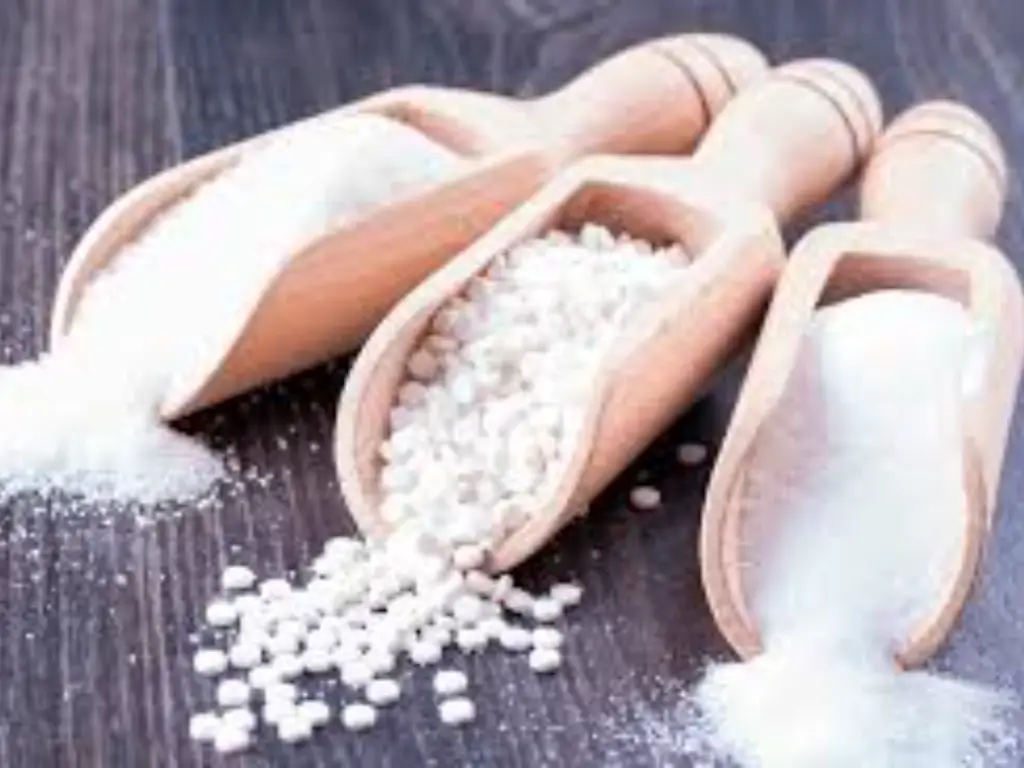
How Artificial Sweeteners Are Made: Inside the Manufacturing Process & Key Equipment
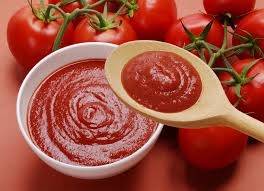
Ketchup Explained: From Ancient Origins to Modern Production Methods
How Lotion Is Made: Step-by-Step Guide for Home and Factory Production
Chemicals
What is the delivery lead time?
The production and delivery lead time depends on specific customization requirements, generally ranging from 4 to 8 weeks.
Cosmetic Making Machine
How to achieve vacuum environment?
The vacuum pump is a device used to generate vacuum, which can draw out the gas in the container to form a vacuum environment. Close wall pipe valves,only open the vacuum pipe pass-by valve,also open the water inlet of vacuum pump,then operate vacuum button. After the the tank get the standard pressure such -0.05Mpa (check the pressure gauge), stop the vacuum operation,close the pass-by valve.
Cosmetic
What is the production capacity of the equipment?
Our equipment supports both small-batch and large-batch production, depending on customer needs. The equipment is highly scalable and can be adjusted according to your production scale.
Detergent powder mixer
Do you also provide formula of detergent powder if I purchase the detergent powder mixer machine?
Yes, Yuany offers technical support to help optimize formulas and adjust production processes, ensuring product stability and performance.
Semi Automatic Capping Machine
What minimum caps size can the desktop capping machine be suit for?
The minimum cap size is 20mm, it is recommend to send caps to test if it is around 20mm.
Leave a message
Have any questions or concerns about our products? Please leave us a message here, and our team will get back to you promptly.
Facebook
YouTube
LinkedIn
Whatsapp: +8613434139712
Guangzhou Yuanyang Machinery