how to repair sealing machine | YUANYANG Expert Guide
- How to Repair a Sealing Machine: A Comprehensive Guide for Industrial Mixer Users
- 1. What are the most common problems with sealing machines?
- 2. How do I troubleshoot a sealing machine that's not sealing properly?
- 3. When should I repair versus replace my sealing machine?
- 4. What are the essential maintenance tips to prolong the life of my sealing machine?
- 5. What new features should I consider when purchasing a new sealing machine?
How to Repair a Sealing Machine: A Comprehensive Guide for Industrial Mixer Users
Sealing machines are crucial in various industries, particularly in ensuring the integrity of products processed by industrial mixers. A malfunctioning sealing machine can lead to significant downtime and product spoilage. This guide addresses common issues, frequently asked questions, and essential knowledge for industrial mixer users when dealing with sealing machine repairs and potential re-procurement.
Meta Title: Sealing Machine Repair Guide for Industrial Mixer Users
Meta Description: Troubleshooting sealing machine issues? Learn how to repair your sealing machine, common problems, and when to consider a replacement. Essential for industrial mixer operators.
Summary: This comprehensive guide provides industrial mixer users with actionable insights on repairing sealing machines. We cover common problems, troubleshooting steps, and critical factors to consider before deciding to repair or replace your equipment. By understanding these key areas, you can minimize downtime and optimize your production process. Approximately 290 characters.
1. What are the most common problems with sealing machines?
Common issues include:
- Inconsistent Seals: This is often due to temperature fluctuations, incorrect pressure settings, or worn-out heating elements.
- Torn or Weak Seals: Can result from using the wrong sealing material, improper alignment, or excessive heat.
- Machine Not Heating: Often caused by a faulty heating element, blown fuse, or wiring issues. According to a 2023 report by Industrial Equipment News, heating element failure accounts for 35% of sealing machine malfunctions.
- Jammed or Stuck Parts: Due to debris buildup or lack of lubrication.
- Control Panel Malfunctions: Problems with the digital interface or settings.
2. How do I troubleshoot a sealing machine that's not sealing properly?
Here's a step-by-step troubleshooting guide:
- Check the Power Supply: Ensure the machine is properly plugged in and the power switch is on.
- Inspect the Heating Element: Look for signs of damage or wear. Use a multimeter to test for continuity. Replace if necessary. Heating elements typically cost between $50 and $200, depending on the model.
- Verify Temperature Settings: Make sure the temperature is appropriate for the sealing material. Consult the manufacturer's recommendations.
- Adjust Pressure Settings: Incorrect pressure can lead to weak or torn seals. Experiment with slight adjustments to find the optimal setting.
- Clean the Sealing Surfaces: Remove any debris or residue that may be interfering with the seal.
- Check the Sealing Material: Ensure you are using the correct type and thickness of material for the machine.
- Inspect the Timing: For continuous sealing machines, verify that the timing is correct. Misalignment can cause improper seals.
3. When should I repair versus replace my sealing machine?
The decision to repair or replace depends on several factors:
- Age of the Machine: Older machines are more prone to breakdowns and may be difficult to repair due to obsolete parts. According to a study by Plant Engineering Magazine, the average lifespan of a sealing machine is 7-10 years with proper maintenance.
- Cost of Repair: If the repair cost exceeds 50% of the replacement cost, replacement is generally more economical.
- Availability of Parts: If parts are no longer available, replacement is the only option.
- Frequency of Breakdowns: If the machine is experiencing frequent breakdowns, it may be time to replace it, even if the individual repairs are relatively inexpensive.
- Technological Advancements: Newer sealing machines may offer improved efficiency, features, and reliability, making replacement a worthwhile investment. Many modern sealing machines offer energy savings of up to 20% compared to older models.
4. What are the essential maintenance tips to prolong the life of my sealing machine?
- Regular Cleaning: Clean the sealing surfaces and surrounding areas regularly to remove debris and prevent buildup.
- Lubrication: Lubricate moving parts as recommended by the manufacturer.
- Inspect Heating Elements: Regularly inspect heating elements for signs of wear or damage.
- Check Wiring: Inspect wiring for loose connections or frayed wires.
- Calibrate Regularly: Ensure the temperature and pressure settings are calibrated correctly.
- Train Operators: Properly train operators on the correct use and maintenance of the machine.
- Follow Manufacturer's Guidelines: Adhere to the manufacturer's recommended maintenance schedule.
5. What new features should I consider when purchasing a new sealing machine?
When procuring a new sealing machine, consider the following features:
- Digital Controls: Digital controls offer precise temperature and pressure settings, improving sealing consistency.
- Automatic Adjustment: Some machines automatically adjust settings based on the material being sealed.
- Data Logging: Data logging capabilities allow you to track sealing parameters and identify potential problems.
- Energy Efficiency: Look for machines with energy-saving features, such as insulated heating elements and automatic shut-off.
- Remote Monitoring: Some machines can be remotely monitored, allowing you to track performance and identify potential problems from anywhere.
- Integration Capabilities: Consider machines that can be easily integrated with your existing industrial mixer and other equipment. Packaging World reports a growing trend toward integrated packaging solutions.
By addressing these key questions and considerations, industrial mixer users can effectively manage their sealing machine maintenance and procurement strategies, minimizing downtime and maximizing productivity.
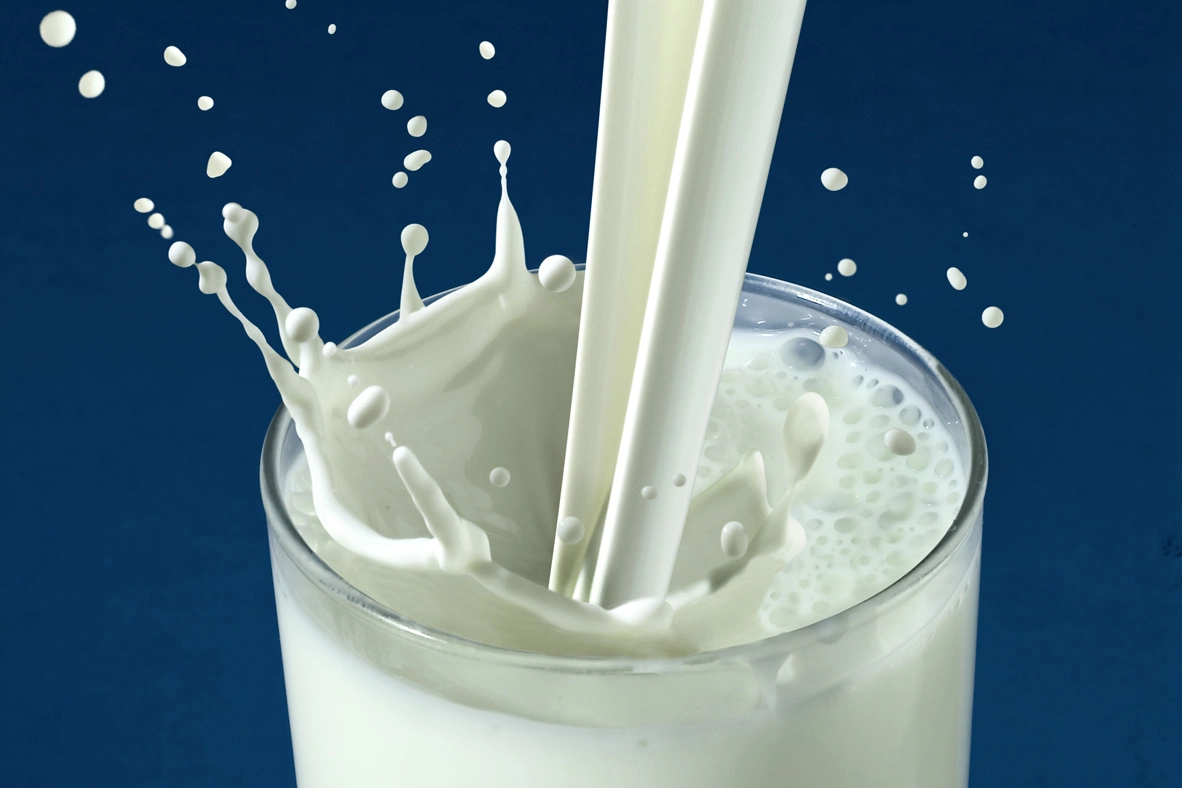
Milk Homogenization Process: Everything You Need to Know About How It Works
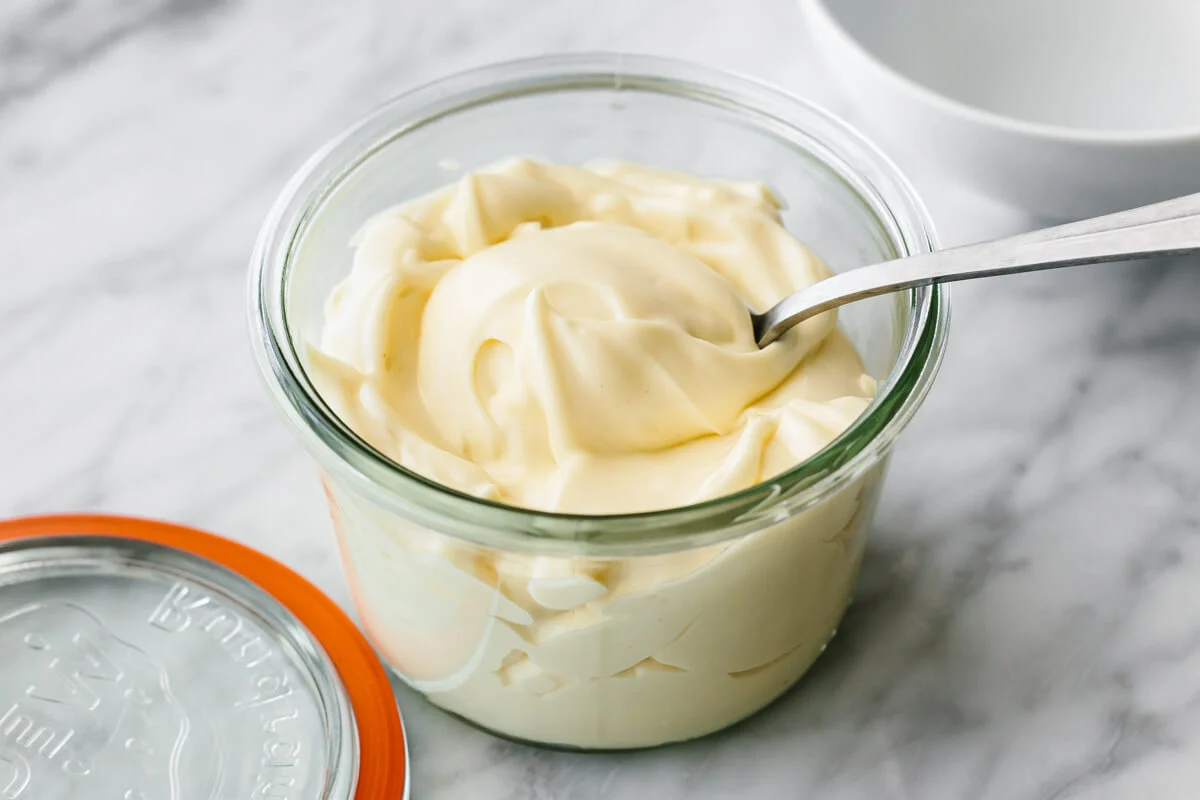
Mayonnaise Manufacturing Process Explained: How Factories Produce Mayonnaise

Water in Oil Emulsion: Meaning, Real-Life Examples, and How to Fix It
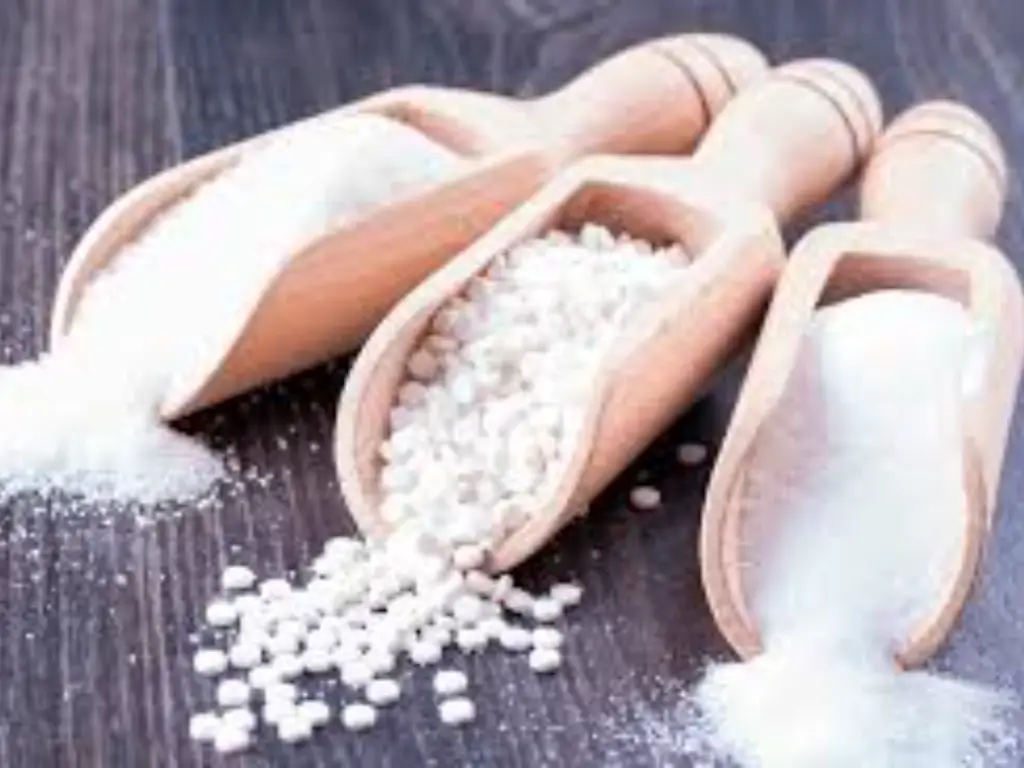
How Artificial Sweeteners Are Made: Inside the Manufacturing Process & Key Equipment
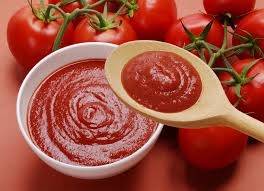
Ketchup Explained: From Ancient Origins to Modern Production Methods
Horizontal Filling Machine
What’s the filling range of this semi auto filler?
There are different sizes of air cylinders. Therefore there are the following filling range:5-60g, 10-120g, 20-200g, 30-300g, 50-500g, 100-1000g, 200-2000g, 300-3000g, 500-5000g. Please tell the minimum bottle and maximum bottle capacity, suitable types of filling machine model will be recommended.
Sachet Packaging Machine for Granules
What cutting method does the granules packaging machine have?
There are in-line cutting, pattern cutting, and in-line continuous bag cutting.
What’s the date printing, steel printing or coding?
There are standard steel date printing on the automatic packaging machine, if clients needs coding type, just tell us to add an extra coding device.
High Speed Dispersion Machine
Can I add two layers of plate for the dispersion machine?
Yes, we can two or more layers of plates or blades.
Semi automatic powder filling machine
What’s the motor brand of this semi automatic powder packing machine?
The filling motor is with Servo motor, which has high filling precision.
Leave a message
Have any questions or concerns about our products? Please leave us a message here, and our team will get back to you promptly.
Facebook
YouTube
LinkedIn
Whatsapp: +8613434139712
Guangzhou Yuanyang Machinery