what is a homogenizer | YUANYANG Expert Guide
- Understanding Homogenizers: A Procurement Guide for Industrial Mixers
- What Exactly is a Homogenizer and How Does it Function?
- Exploring the Different Types of Industrial Homogenizers
- Key Applications of Homogenizers Across Various Industries
- Critical Factors to Consider When Procuring an Industrial Homogenizer
- The Tangible Benefits of Integrating Homogenizers into Your Production Line
Understanding Homogenizers: A Procurement Guide for Industrial Mixers
In the complex world of industrial manufacturing, achieving uniform product quality, stability, and optimal performance often hinges on the precise control of particle size and dispersion. This is where industrial homogenizers become indispensable. For professionals involved in industrial mixer procurement, a deep understanding of these powerful machines is crucial. This guide aims to demystify homogenizers, exploring their function, types, applications, and key considerations for a wise investment.
What Exactly is a Homogenizer and How Does it Function?
A homogenizer is a high-shear or high-pressure mixing device used to reduce the particle size and uniformly disperse one substance into another, creating a stable and consistent mixture. The core principle involves subjecting a fluid mixture to intense mechanical forces, typically high pressure, high velocity, or high shear, forcing particles or droplets to break down into much smaller sizes, often into the sub-micron range (e.g., 100-500 nanometers for many high-pressure applications). This process increases the surface area of the dispersed phase, leading to greater stability, improved texture, and enhanced properties of the final product.
For example, in dairy processing, milk is passed through a homogenizer at pressures often ranging from 1500 to 2500 PSI (100-170 bar). This intense pressure forces milk through a tiny gap, shearing fat globules into smaller, more stable particles, preventing cream separation. Other methods include cavitation (ultrasonic homogenizers) and mechanical impact/shear (rotor-stator mixers).
Exploring the Different Types of Industrial Homogenizers
Industrial applications demand robust and specialized homogenizer types. The choice depends heavily on the desired particle size, product viscosity, and production volume:
- High-Pressure Homogenizers: These are perhaps the most common for high-volume, fine particle reduction. They operate by pumping the product at very high pressures (up to 60,000 PSI or 4000 bar) through a small, adjustable gap. The forces involved include intense shear, cavitation, and turbulence, leading to highly uniform particle sizes. They are ideal for emulsions, suspensions, and liposomal formulations.
- Rotor-Stator Homogenizers (High-Shear Mixers): These consist of a rapidly rotating rotor within a stationary stator. The product is drawn into the center of the mixing head and expelled at high velocity through the openings in the stator. This generates intense shear forces, ideal for initial particle breakdown, dissolving solids, and creating coarse to medium emulsions. They are often used as a pre-treatment before high-pressure homogenization or for less demanding applications.
- Ultrasonic Homogenizers: These utilize high-frequency sound waves (ultrasound) to create cavitation bubbles within the liquid. The rapid collapse of these bubbles generates localized high-pressure and shear forces, effectively disrupting particles and cells. They are particularly effective for cell lysis, nano-emulsions, and certain chemical reactions, often used for smaller-scale or specialized applications.
Key Applications of Homogenizers Across Various Industries
Homogenizers are critical across a diverse range of industries due to their ability to create stable, high-quality products:
- Food and Beverage: Dairy (milk, cream, yogurt), sauces, dressings, fruit juices, purees, infant formula, plant-based beverages. They prevent separation, improve mouthfeel, and extend shelf life.
- Pharmaceutical: Emulsions (e.g., IV lipids), suspensions (e.g., antibiotic syrups), liposomes, vaccines, API dispersion. Essential for bioavailability, dosage consistency, and stability.
- Cosmetics and Personal Care: Creams, lotions, shampoos, foundations. They create stable emulsions, improve texture, and ensure consistent product appearance.
- Chemical Industry: Pigment dispersion, polymer emulsions, lubricants, adhesives. Used to achieve uniform particle size for optimal performance and stability.
- Biotechnology: Cell disruption (e.g., bacteria, yeast, algae) for protein extraction, DNA/RNA isolation.
Critical Factors to Consider When Procuring an Industrial Homogenizer
Selecting the right homogenizer requires careful consideration of several factors to ensure it meets your specific operational and product requirements:
- Application Specifics: What is the desired particle size? Is it an emulsion, suspension, or cell disruption?
- Product Viscosity and Abrasiveness: High viscosity or abrasive products require robust pump designs and wear-resistant materials.
- Production Capacity: What flow rate (liters per hour or gallons per hour) is needed to match your production line?
- Operating Pressure: Higher pressures generally lead to finer particle sizes but also higher energy consumption.
- Material Compatibility: Ensure all wetted parts are compatible with your product, especially for corrosive or sterile applications (e.g., stainless steel grades like 316L, special alloys).
- Clean-in-Place (CIP) / Sterilize-in-Place (SIP) Capability: Essential for hygiene-sensitive industries like food and pharma, simplifying cleaning and reducing downtime.
- Energy Efficiency: Homogenizers can be energy-intensive. Evaluate power consumption relative to throughput.
- Maintenance and Spare Parts: Consider ease of maintenance, availability of spare parts, and supplier support.
- Industry Standards and Certifications: Compliance with FDA, GMP, CE, 3-A Sanitary Standards, etc., is vital for regulated industries.
- Cost of Ownership: Beyond the initial purchase, consider operating costs, maintenance, and potential productivity gains.
The Tangible Benefits of Integrating Homogenizers into Your Production Line
Investing in the right industrial homogenizer yields significant benefits that directly impact product quality, efficiency, and market competitiveness:
- Enhanced Product Stability: Prevents separation, settling, or creaming, leading to longer shelf life and reduced product waste.
- Improved Texture and Consistency: Creates smoother, more uniform products with better mouthfeel and visual appeal.
- Increased Bioavailability/Absorption: Especially critical in pharmaceutical applications where finer particles are absorbed more efficiently.
- Better Color and Appearance: For pigments, dyes, and cosmetic formulations, uniform dispersion leads to brighter, more consistent colors.
- Reduced Ingredient Usage: In some cases, improved dispersion can allow for lower concentrations of expensive ingredients while maintaining desired product properties.
- Cost Savings: By extending shelf life, reducing rework, and optimizing ingredient usage, homogenizers can contribute to overall cost efficiency.
In conclusion, industrial homogenizers are vital assets for modern manufacturing, enabling the production of high-quality, stable, and consistent products. By carefully assessing your specific needs and understanding the various technologies available, procurement professionals can make informed decisions that drive innovation and efficiency within their operations.
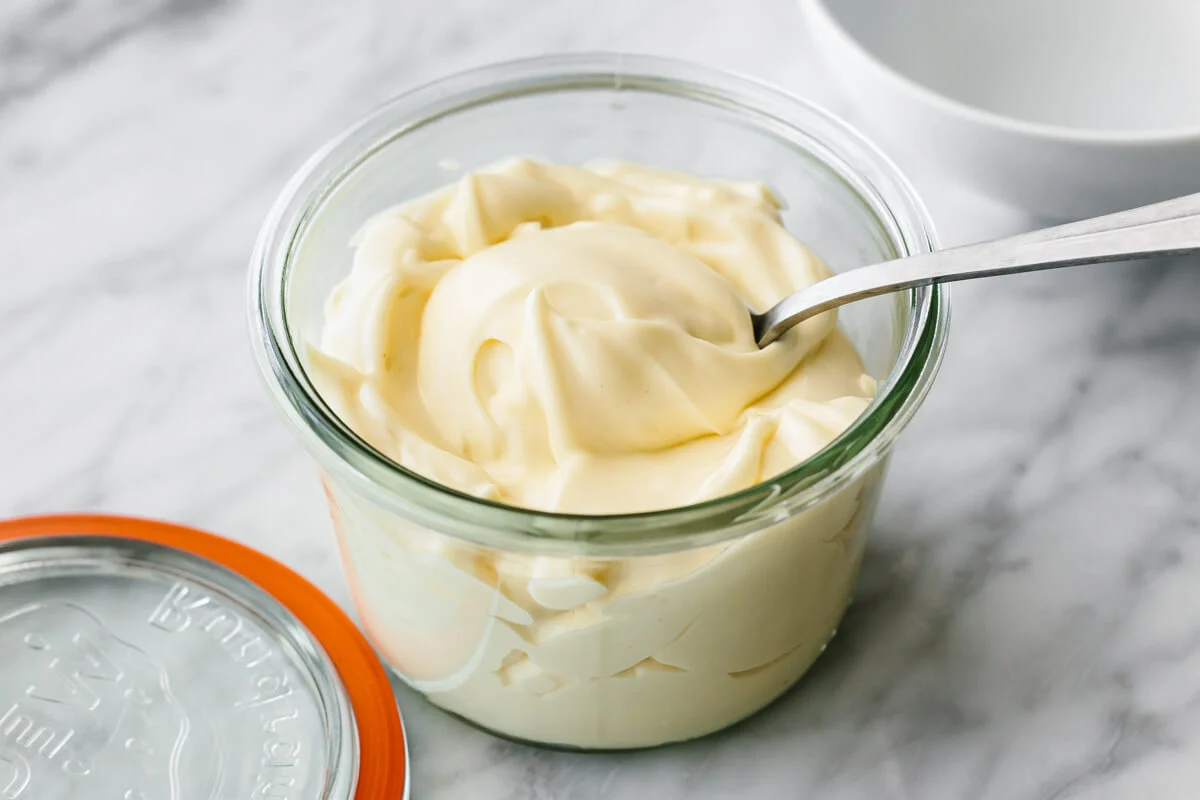
Mayonnaise Manufacturing Process Explained: How Factories Produce Mayonnaise

Water in Oil Emulsion: Meaning, Real-Life Examples, and How to Fix It
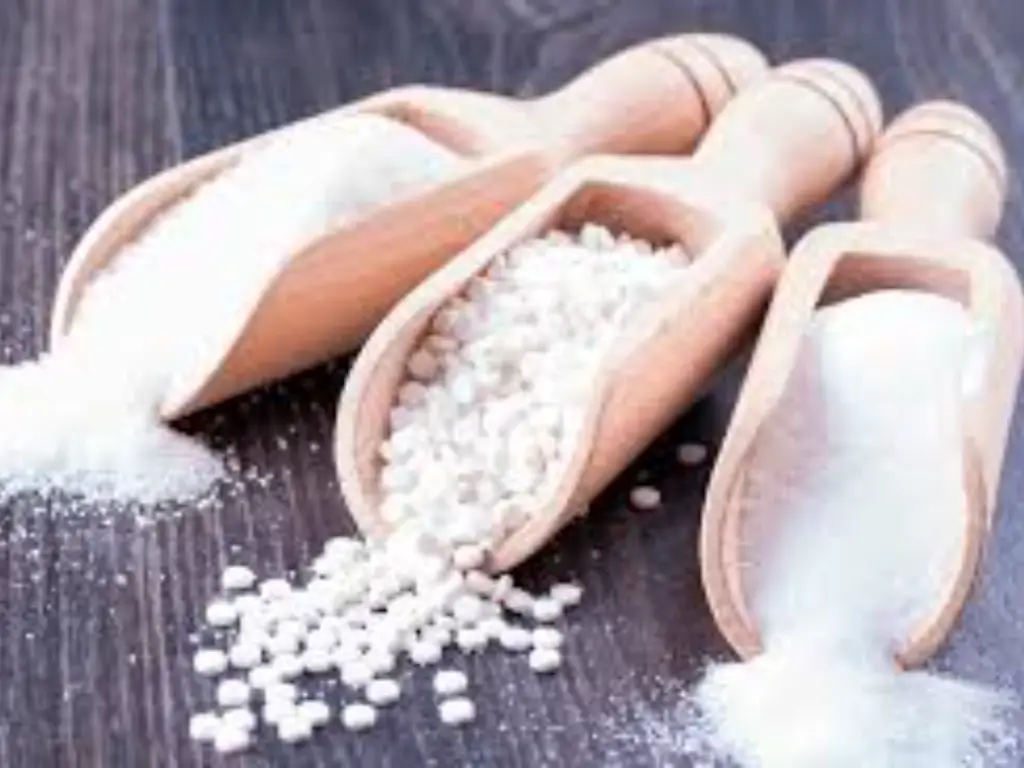
How Artificial Sweeteners Are Made: Inside the Manufacturing Process & Key Equipment
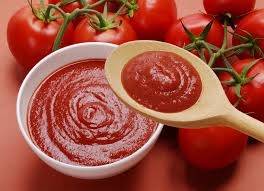
Ketchup Explained: From Ancient Origins to Modern Production Methods
How Lotion Is Made: Step-by-Step Guide for Home and Factory Production
Homogenizing Mixer
For the electric heating liquid soap mixing tank, where do you install the heater, how does it work?
The heater tube is installed at bottom. The heating operation is controlled on the control box. Before operation, add tap water into jacket from heater container’s inlet valve. The heater heat water, the hot water conduct heat through inner layer to materials in the tank.
Medicine
Does Yuanyang’s pharmaceutical equipment comply with GMP standards?
Yes, all of Yuanyang’s pharmaceutical equipment complies with Good Manufacturing Practice (GMP) standards, ensuring quality and hygiene at every production stage, meeting the requirements of global pharmaceutical regulatory agencies.
Semi automatic powder filling machine
What’s the motor brand of this semi automatic powder packing machine?
The filling motor is with Servo motor, which has high filling precision.
Chemicals
Does the equipment meet environmental standards?
Yes, our equipment meets the environmental standards for the chemical industry, reducing pollutant emissions.
Desktop Bottle Sealing Machine
How does the automatic bottle sealing machine work?
Electromagnetic induction sealing machine uses high-frequency electromagnetic field to act on the packaging film, resulting in an induced current inside, which will generate heat, melt the packaging film, and then form a sealing after cooling.
Leave a message
Have any questions or concerns about our products? Please leave us a message here, and our team will get back to you promptly.
Facebook
YouTube
LinkedIn
Whatsapp: +8613434139712
Guangzhou Yuanyang Machinery