what water filter is the best | YUANYANG Expert Guide
- Industrial Mixer Procurement: An Essential Buyer's Guide
- What Types of Industrial Mixers Are Available and For What Applications?
- How Do I Determine the Right Size and Capacity for My Industrial Mixer?
- What Factors Influence the Cost of an Industrial Mixer?
- What Are Key Considerations for Maintenance and Longevity of Industrial Mixers?
- What Are Important Safety Features and Regulatory Compliance for Industrial Mixers?
Industrial Mixer Procurement: An Essential Buyer's Guide
Acquiring the right industrial mixer is a pivotal decision for any operation dealing with blending, dispersion, emulsification, or homogenization. It's not merely about purchasing machinery; it's about investing in a solution that optimizes production efficiency, product quality, and operational safety. This guide aims to demystify the procurement process by addressing the top questions buyers typically face, ensuring you make an informed and strategic investment.
What Types of Industrial Mixers Are Available and For What Applications?
The world of industrial mixers is diverse, with designs tailored for specific material properties and processing goals. Common types include:
- Ribbon Blenders: Ideal for dry powders, granules, and pastes. They use helical agitators to create a balanced mixing action, suitable for food ingredients, chemicals, and pharmaceuticals.
- High-Shear Mixers: Employ high-speed rotors and stators to create intense shear forces, perfect for emulsifying liquids, dispersing solids into liquids, and creating fine suspensions in industries like cosmetics, paints, and specialty chemicals.
- Planetary Mixers: Excellent for highly viscous materials like dough, putties, and ceramics. The agitator orbits the mixing bowl while rotating on its own axis, ensuring thorough wall-scraping and homogenous blends.
- Paddle Mixers: Offer gentle mixing for delicate products or when minimal shear is required, often found in food processing for salads or delicate powders.
- Inline Mixers: Designed for continuous processing, these mixers integrate directly into pipelines for constant flow operations, common in chemical and food industries for rapid blending.
Selecting the correct type hinges on your material's viscosity, density, batch size, desired homogeneity, and processing environment (e.g., sanitary, hazardous).
How Do I Determine the Right Size and Capacity for My Industrial Mixer?
Sizing an industrial mixer correctly is crucial for performance and cost-efficiency. It involves analyzing several parameters:
- Batch Volume: The total volume of material to be processed per cycle or continuously. Consider future expansion needs.
- Material Properties: Viscosity, specific gravity, and abrasiveness directly impact motor power requirements and agitator design. A highly viscous material, for example, demands more power and a robust agitator.
- Mixing Time and Homogeneity: Define the desired blend quality and the time frame within which it must be achieved. This influences mixer speed, impeller design, and power input.
- Operating Conditions: Temperature, pressure, and whether the process is batch or continuous.
Many manufacturers offer sizing software or require detailed process information to recommend the optimal model. Pilot testing with a smaller unit is often recommended for complex or critical applications to validate the design and scale-up parameters before a full-scale investment.
What Factors Influence the Cost of an Industrial Mixer?
The cost of an industrial mixer can vary significantly, from a few thousand to several hundred thousand dollars, depending on its specifications. Key cost drivers include:
- Type and Size: Larger, more specialized mixers (e.g., high-pressure, vacuum-rated, or explosion-proof designs) are inherently more expensive.
- Material of Construction: Standard stainless steel (e.g., 304 or 316L for sanitary applications) is common, but exotic alloys (e.g., Hastelloy, Titanium) for corrosive or high-temperature environments significantly increase cost.
- Motor Power and Controls: Higher horsepower motors and advanced control systems (e.g., Variable Frequency Drives (VFDs), PLC integration for automation) add to the price.
- Special Features and Certifications: Options like heating/cooling jackets, vacuum capabilities, clean-in-place (CIP) systems, and compliance with industry standards (e.g., GMP for pharmaceuticals, ATEX for hazardous zones) contribute to the overall investment.
- Customization: Any deviation from standard designs to meet unique process requirements will incur additional engineering and manufacturing costs.
It's vital to balance initial capital outlay with long-term operational efficiency and compliance.
What Are Key Considerations for Maintenance and Longevity of Industrial Mixers?
Proper maintenance is paramount to ensuring the longevity and reliable operation of your industrial mixer. Key considerations include:
- Regular Cleaning: Essential to prevent cross-contamination and material buildup, especially in sanitary applications. CIP systems can automate this.
- Lubrication: Bearings, gearboxes, and seals require routine lubrication according to manufacturer specifications to minimize friction and wear.
- Inspection of Wear Parts: Regularly check agitator blades, seals, belts, and bearings for signs of wear, corrosion, or damage. Proactive replacement prevents catastrophic failures.
- Motor and Electrical Checks: Inspect motor functionality, wiring integrity, and control panel components. For VFDs, ensure proper settings and cooling.
- Scheduled Preventative Maintenance: Adhere strictly to manufacturer-recommended maintenance schedules. Many operations implement predictive maintenance technologies, such as vibration analysis or thermal imaging, to anticipate issues before they lead to downtime.
Investing in quality spare parts and having a clear maintenance schedule will significantly extend the life cycle of your equipment.
What Are Important Safety Features and Regulatory Compliance for Industrial Mixers?
Safety is non-negotiable in industrial environments. Modern industrial mixers incorporate numerous safety features, and compliance with regulations is mandatory:
- Emergency Stops (E-stops): Strategically placed buttons to immediately halt operation in an emergency.
- Interlocks: Safety switches that prevent mixer operation if guards are open, lids are not secured, or other hazardous conditions exist.
- Pressure Relief: For sealed vessels, pressure relief valves are critical to prevent over-pressurization.
- Explosion-Proof (Ex) Motors and Controls: Essential for processing flammable liquids or dusts. Compliance with standards like ATEX (Europe) or IECEx (International) is critical for hazardous areas.
- Guarding: Physical barriers to prevent contact with moving parts.
- Regulatory Compliance: Adherence to local and international standards such as OSHA (Occupational Safety and Health Administration) in the U.S., CE marking in Europe, and Good Manufacturing Practices (GMP) for food and pharmaceutical industries.
Always ensure your chosen mixer meets all relevant safety standards and regulatory requirements for your specific industry and location. Discuss these critical aspects thoroughly with your supplier during the procurement process.
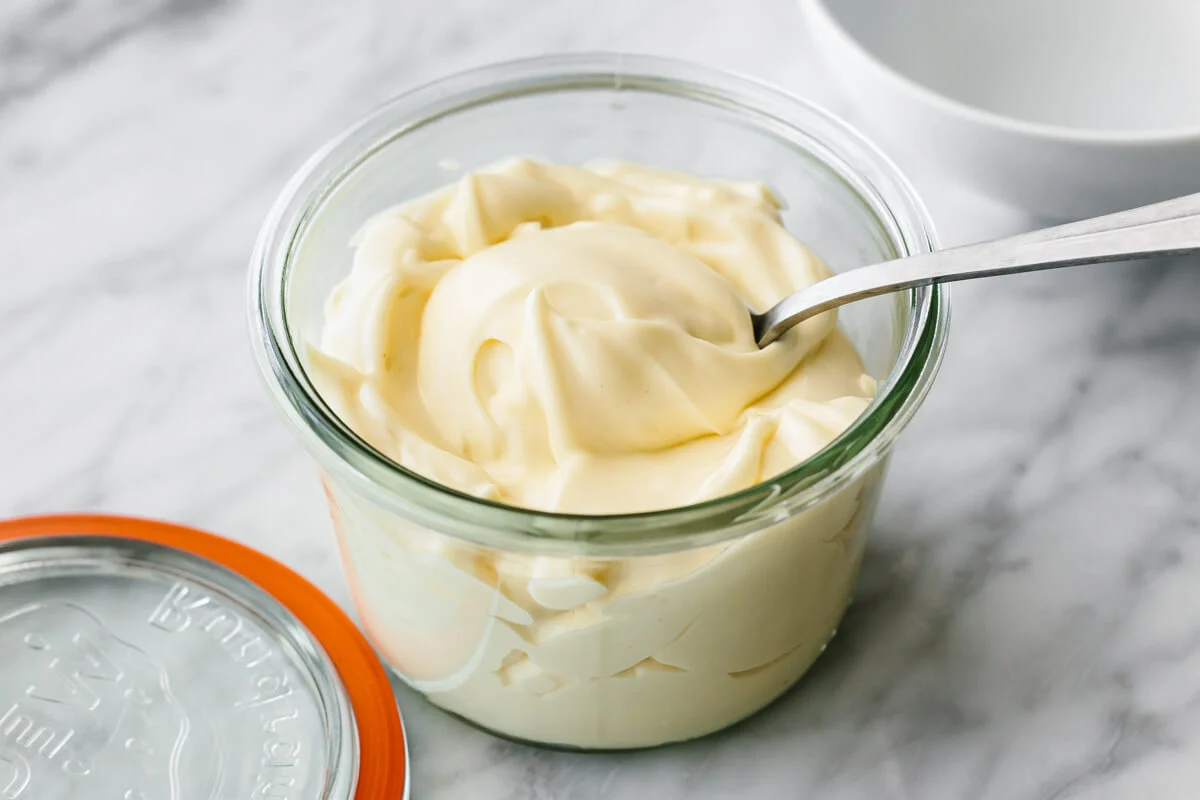
Mayonnaise Manufacturing Process Explained: How Factories Produce Mayonnaise

Water in Oil Emulsion: Meaning, Real-Life Examples, and How to Fix It
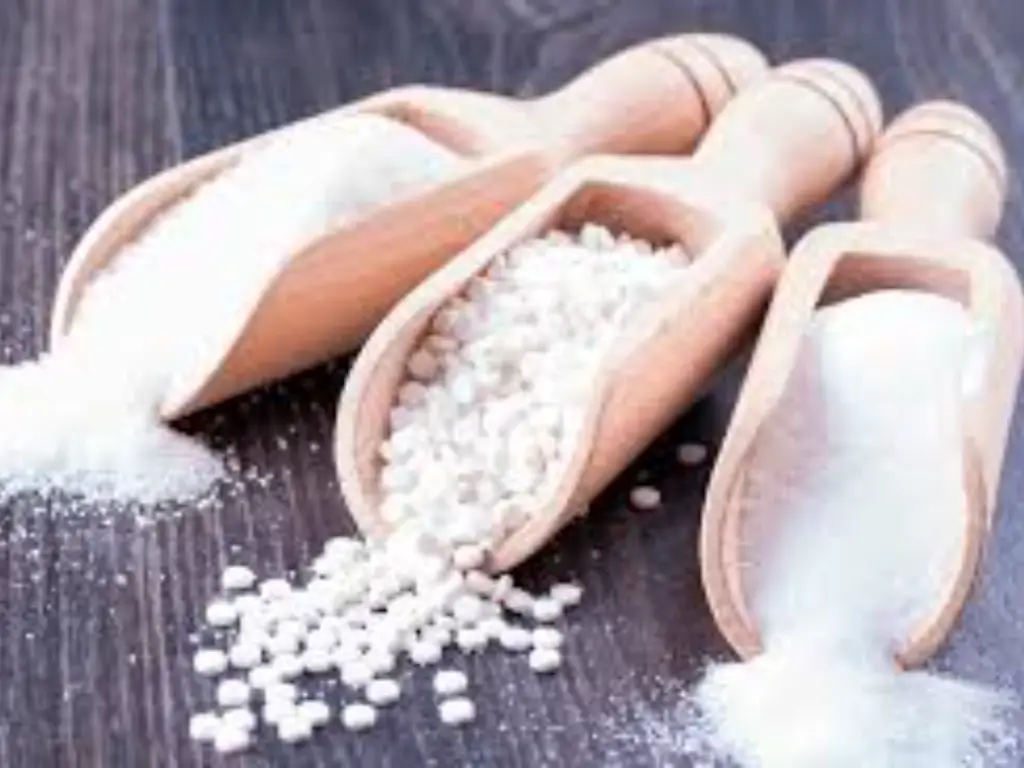
How Artificial Sweeteners Are Made: Inside the Manufacturing Process & Key Equipment
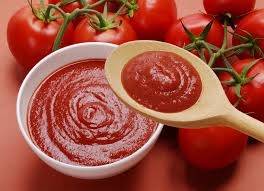
Ketchup Explained: From Ancient Origins to Modern Production Methods
How Lotion Is Made: Step-by-Step Guide for Home and Factory Production
Sachet Packaging Machine for Granules
Can I set the sealing length on the control panel of automatic packing machine?
Yes, each machine has a sealing length range regarding bag size, it is flexible to change the length on the micro control system within available range.
Single Layer Agitator Tank
Does the tank with mixer also has heater?
The model is non-heating type, the heating mixer tanks is another type with 3 layers, a heating jacket and an insulation jacket.
Medicine
Is the equipment suitable for small-batch production?
Yes, Yuanyang’s equipment is also suitable for small-batch production. Our equipment can adjust to batch sizes based on production requirements, while maintaining consistent product quality.
Automatic Servo Motor Capping Machine
Is there a bottle gripper to keep thin bottles stable?
Yes, the auto servo capping machine is equipped with pneumatic clamping device for bottle stability.
FAQs
I don’t come to the company, how can I learn the machines?
We provide video & manual instructions of the machines you purchase and online service,as well as face-to-face teaching. Any questions or concerns,please feel free to contact our customer service for free information. If you come to the company,our technical staff will teach you hand by hand.
Leave a message
Have any questions or concerns about our products? Please leave us a message here, and our team will get back to you promptly.
Facebook
YouTube
LinkedIn
Whatsapp: +8613434139712
Guangzhou Yuanyang Machinery