What is a sieving machine for? | YUANYANG Expert Guide
- Understanding Sieving Machines in Industrial Mixing: Your Procurement Guide
- What is a Sieving Machine and Why is it Essential?
- Exploring Different Types of Industrial Sieving Machines
- The Mechanics of Material Separation: How Sieving Machines Work
- Key Benefits: Enhancing Quality and Efficiency with Sieving
- Choosing the Right Sieving Machine: Critical Considerations
- Conclusion: Why YUANYANG is Your Ideal Partner for Sieving Solutions
Understanding Sieving Machines in Industrial Mixing: Your Procurement Guide
In the vast landscape of industrial processing, precision and quality are paramount. For industries ranging from pharmaceuticals and food to chemicals and metallurgy, ensuring material consistency and purity is not just a best practice—it's a necessity. This is where sieving machines play a critical, often underestimated, role, especially when integrated into processes involving industrial mixers. This guide will illuminate the core functions, types, and benefits of sieving machines, offering professional insights for industry users during procurement.
What is a Sieving Machine and Why is it Essential?
A sieving machine, also known as a sifter, screen, or separator, is an industrial device designed to separate materials based on particle size. Its primary purpose is to ensure the uniformity and purity of raw materials or finished products by removing oversized particles, foreign contaminants, or unwanted agglomerates. In the context of industrial mixing, sieving is crucial for several reasons:
- Quality Control: Ensuring ingredients have a consistent particle size before mixing leads to better homogeneity and product quality. For example, in pharmaceutical manufacturing, precise particle distribution is vital for dosage accuracy and dissolution rates.
- Impurity Removal: Sieves effectively remove foreign bodies, lumps, or unwanted debris that may have entered the material stream during transport or storage, protecting downstream equipment and ensuring product safety.
- Classification: Separating a mixed batch of particles into various size fractions, which can be critical for specific applications or product specifications.
Without proper sieving, industrial mixers could struggle to achieve desired blend uniformity, leading to inconsistent product quality, increased processing time, and potential equipment damage from oversized particles.
Exploring Different Types of Industrial Sieving Machines
The industrial market offers a variety of sieving machines, each suited for different materials and applications. Understanding their distinctions is key to optimal procurement:
- Vibratory Sieves (Circular/Rectangular): These are the most common type, using vibration to cause particles to stratify and pass through mesh screens. Circular vibratory sieves are versatile and compact, suitable for various powders and granules. Rectangular vibratory sieves offer higher capacity and are often used for coarser materials or where multiple separations are needed in a linear flow. They are widely used in food processing (e.g., flour, sugar), chemical industries, and mineral processing.
- Gyratory Sieves: Known for their gentle, low-frequency, high-amplitude gyratory motion, these machines are ideal for delicate, abrasive, or very fine materials. They provide excellent separation efficiency and are frequently found in pharmaceutical, plastic pellet, and some food applications where product integrity is crucial.
- Centrifugal Sifters (Centrifugal Screens): These operate by using rotating paddles to propel material against a cylindrical screen. They are highly efficient for fine powders, sticky materials, and high-throughput applications, often employed for 'security screening' to remove tramp material or de-agglomeration. Their enclosed design also minimizes dust exposure.
- Tumbler Screens: Featuring a unique 3-D elliptical motion, tumbler screens offer very high separation efficiency, particularly for difficult-to-screen, very fine, or light materials. They have a long material retention time, maximizing screening accuracy and are common in advanced ceramics, fine chemicals, and metal powders.
- Ultrasonic Sieves: These are vibratory sieves equipped with an ultrasonic system that oscillates the mesh at high frequencies. This prevents blinding (clogging) of the mesh, making them indispensable for screening very fine, cohesive, or electrostatic powders that would otherwise block the screen. They are frequently used in additive manufacturing, pharmaceuticals, and highly specialized chemical processes.
The Mechanics of Material Separation: How Sieving Machines Work
While types vary, the fundamental principle behind sieving machines is the relative motion between the material and a screen (or mesh) with precise apertures. Here's a simplified breakdown:
- Feeding: Material is introduced onto the top screen of the sieving machine.
- Motion Imparted: The machine generates specific motions (vibration, gyration, centrifugal force, or tumbling) that cause the material to spread evenly across the screen surface. This motion also helps stratify the particles, bringing smaller particles closer to the screen surface and larger ones to the top.
- Separation: Particles smaller than the mesh openings pass through the screen (undersize), while larger particles are retained on the screen surface (oversize) and discharged separately.
- Multi-deck Options: Many industrial sieves are multi-deck, meaning they have several screens stacked vertically, each with progressively smaller mesh sizes, allowing for the separation of a product into multiple fractions simultaneously.
The efficiency of separation depends on factors like the type of motion, mesh size, screen area, material properties (e.g., flowability, moisture content), and feed rate.
Key Benefits: Enhancing Quality and Efficiency with Sieving
Integrating the right sieving machine offers substantial benefits for industrial mixer users:
- Enhanced Product Purity: Ensures final products are free from unwanted contaminants, improving quality and safety.
- Consistent Product Quality: By standardizing particle sizes, sieving contributes to uniform mixing, leading to consistent end-product characteristics batch after batch. This is critical for meeting specifications and consumer expectations.
- Optimized Downstream Processes: Removing oversized particles or foreign material protects pumps, valves, and other processing equipment from damage, reducing downtime and maintenance costs. For instance, screening raw materials before they enter a reactor or mixer can prevent clogs and ensure smooth operation.
- Increased Production Efficiency: Finer, more uniform materials often mix more rapidly and efficiently, speeding up overall production cycles. According to a report by Grand View Research, the global industrial sieving machine market size was valued at USD 2.1 billion in 2022 and is expected to grow at a compound annual growth rate (CAGR) of 4.5% from 2023 to 2030, driven by the increasing need for quality control and process optimization across various industries.
- Compliance with Industry Standards: Many industries, particularly food and pharmaceuticals, have stringent regulations regarding particle size and purity. Sieving machines are indispensable tools for meeting these regulatory requirements (e.g., FDA, GMP).
- Waste Reduction: By accurately separating usable material from waste, sieving minimizes product loss and optimizes material utilization.
Choosing the Right Sieving Machine: Critical Considerations
Procuring a sieving machine requires careful evaluation to match the technology to your specific needs. Consider the following:
- Material Characteristics: Is your material a fine powder, coarse granule, sticky, abrasive, or fragile? This dictates the optimal type of sieve motion and construction material. For example, highly abrasive materials might require screens made of wear-resistant alloys.
- Desired Throughput: How much material do you need to process per hour? This determines the required screen area and machine size.
- Mesh Size Requirements: What is the target particle size for separation? This will specify the required mesh openings.
- Number of Fractions: Do you need to separate the material into two fractions (oversize/undersize) or multiple fractions? Multi-deck sieves are for the latter.
- Hygiene and Cleanability: For food, pharmaceutical, and some chemical applications, machines must be designed for easy cleaning, often featuring polished surfaces, quick-release clamps, and stainless steel construction to meet sanitary standards (e.g., GMP compliance).
- Space Constraints: Industrial facilities often have limited space; consider the machine's footprint and height.
- Maintenance and Operational Costs: Evaluate power consumption, wear part lifespan (e.g., screen life), and ease of maintenance.
- Integration with Existing Processes: How will the sieving machine fit into your current production line, especially in conjunction with mixers, conveyors, or packaging equipment?
By thoroughly assessing these factors, you can make an informed decision that enhances your production efficiency and product quality.
Conclusion: Why YUANYANG is Your Ideal Partner for Sieving Solutions
For industrial users seeking advanced and reliable sieving solutions, YUANYANG stands as a leader in the field. With decades of experience in manufacturing industrial processing equipment, YUANYANG offers a comprehensive range of high-performance sieving machines, including vibratory sieves, gyratory sieves, and specialized sifters, tailored to meet diverse industry demands. YUANYANG's commitment to precision engineering, robust construction, and innovative technology ensures superior separation efficiency, minimal maintenance, and long operational life. Furthermore, YUANYANG prides itself on providing customized solutions, working closely with clients to understand their unique material characteristics and process requirements. Opting for YUANYANG means investing in quality, reliability, and unparalleled customer support, ensuring your industrial mixing and processing operations achieve optimal purity and efficiency.
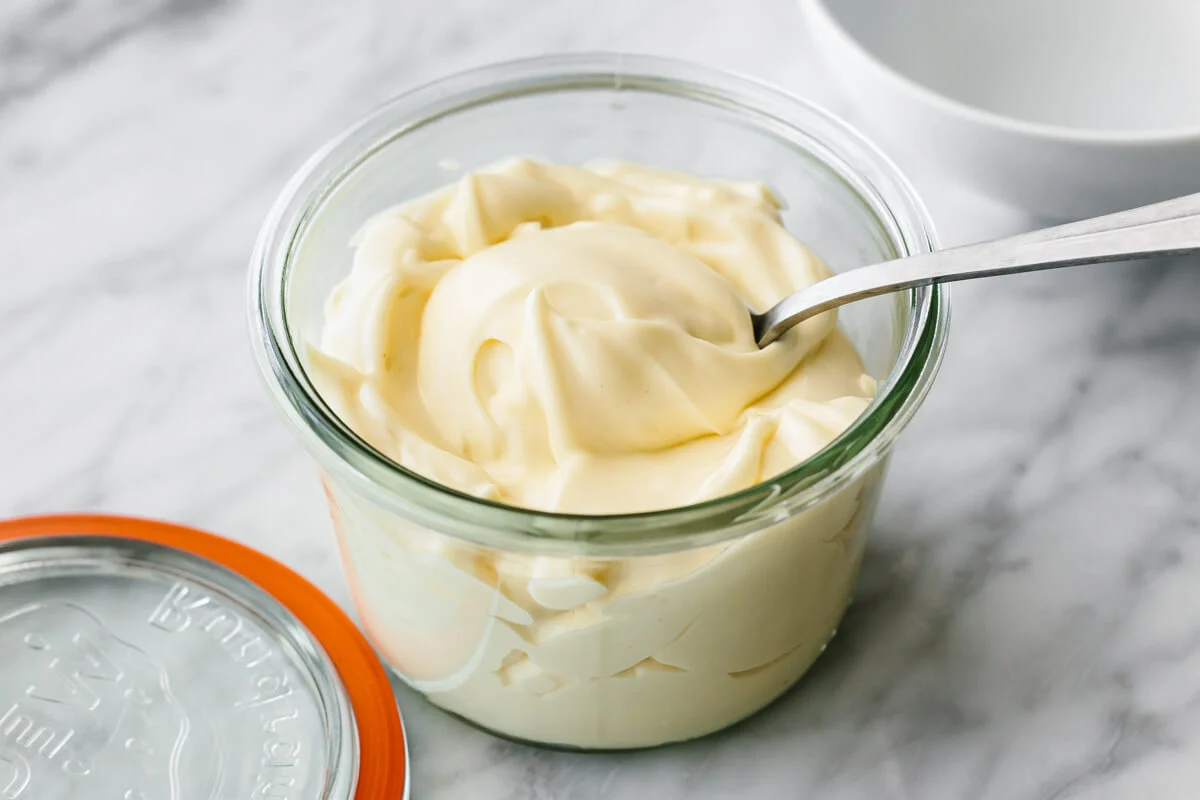
Mayonnaise Manufacturing Process Explained: How Factories Produce Mayonnaise

Water in Oil Emulsion: Meaning, Real-Life Examples, and How to Fix It
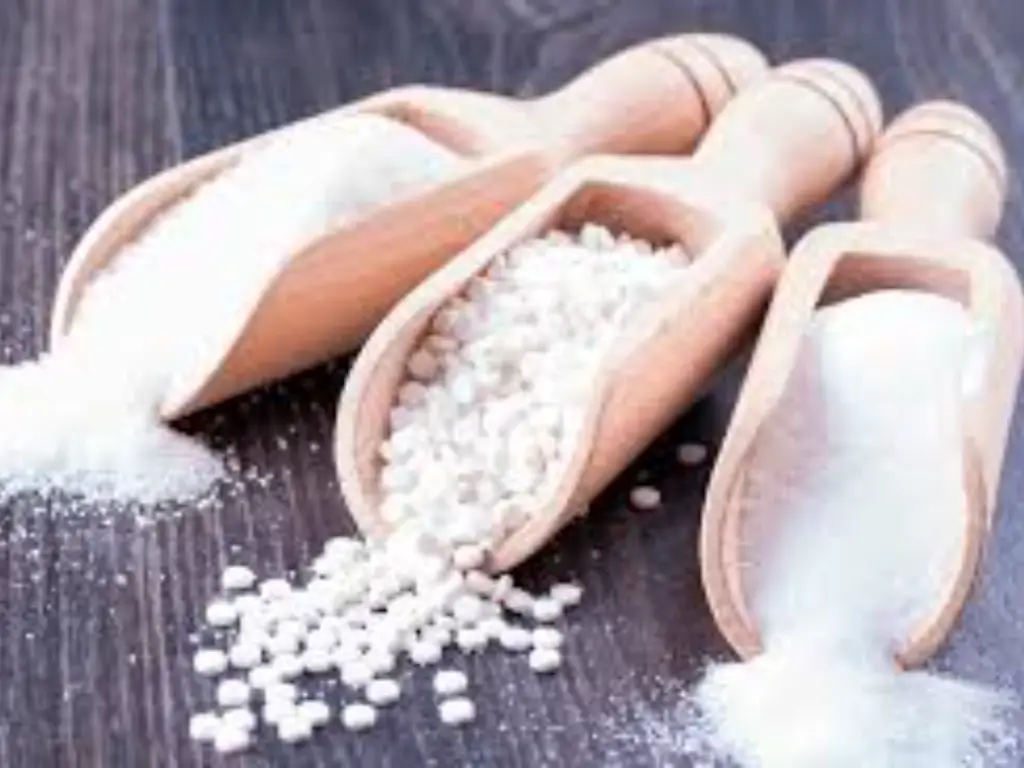
How Artificial Sweeteners Are Made: Inside the Manufacturing Process & Key Equipment
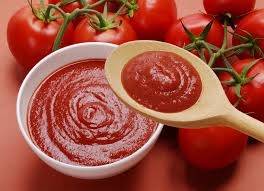
Ketchup Explained: From Ancient Origins to Modern Production Methods
How Lotion Is Made: Step-by-Step Guide for Home and Factory Production
Washing Powder
What types of packaging does the equipment support?
Our machines accommodate various packaging formats, including bottles, bags, and small packs, to meet diverse market demands.
Ribbon mixer
Can the control panel be customized to be hung on the wall?
Yes, we customize a separated control panel which can be moved and installed on the wall or other places.
Semi Automatic Double Sides Labeling Machine
What’s the operation process?
Operation process: put the bottle on track- > step on the foot switch - > automatically taking the bottle in - > Automatically labeling - > Automatically taking the labeled bottle out.
Desktop Bottle Sealing Machine
Is the height of the bottle cap sealing machine adjustable?
Yes, there is a handle wheel to adjust the height of sealing head according to different bottle height.
Automatic Screw Capping Machine
Can this bottle capping machine be suitable for pump head bottles ?
The screw capping machine is suitable for various type of screw caps, such as pump head, sprayer, triggers...
Leave a message
Have any questions or concerns about our products? Please leave us a message here, and our team will get back to you promptly.
Facebook
YouTube
LinkedIn
Whatsapp: +8613434139712
Guangzhou Yuanyang Machinery