what is the best water filter | YUANYANG Guide
- What is the Best Water Filter for Industrial Mixer Applications?
- Best Water Filters for Industrial Mixer Professionals
- Importance of Water Filtration in Industrial Mixing
- Essential Qualities of the Best Water Filter
- Leading Water Filter Technologies
- Factors for Selecting the Best Water Filter
- Maintenance Best Practices
- Authoritative Sources
- Key Takeaways
What is the Best Water Filter for Industrial Mixer Applications?
Professionals in the industrial mixer sector often ask: what is the best water filter? Clean water is critical for mixer performance, equipment longevity, and product quality. This knowledge article reviews the top industrial water filter solutions to guide informed decisions.
Best Water Filters for Industrial Mixer Professionals
Importance of Water Filtration in Industrial Mixing
- Ensures Consistent Product Quality
Filtration removes particulates, minerals, and contaminants that can alter mixing outcomes.
- Protects Equipment and Reduces Downtime
Clean water prevents clogging, scale buildup, and corrosion, extending mixer lifespan.
*Source: (https://www.cdc.gov/healthywater/drinking/public/water_treatment.html)*
- Enhances Compliance
Meets regulatory standards for water purity in industrial processes.
Essential Qualities of the Best Water Filter
- High Flow Rate Compatibility
Supports fast-paced, large-scale mixing operations.
- Particle Removal Efficiency
Filters with micron ratings of 5 or lower capture fine particles.
- Chemical Resistance
Materials designed for harsh industrial environments (e.g., stainless steel or specialized polymers).
- Ease of Maintenance
Quick-access housings and visual indicators optimize filter replacement cycles.
- Scalability
Modules available for both single-mixer stations and central water supply lines.
Leading Water Filter Technologies
Sand Filters
- Function: Remove suspended solids, suitable for preliminary filtration.
- Best For: High-volume water intake lines before finer filtration stages.
Cartridge Filters
- Function: Trap particulates down to the micron level; common for point-of-use filtration.
- Advantages: Easy replacement and customizable for flow and retention.
Reverse Osmosis (RO) Systems
- Function: Eliminates dissolved salts, organics, and most microorganisms.
- Usage: Critical in industries requiring high water purity (e.g., food & beverage, pharmaceuticals).
- Reference: (https://www.epa.gov/water-research/water-treatment-technologies)
UV Disinfection Units
- Function: Non-chemical microbial control for water feeding into mixers.
- Benefit: Ensures sterility without chemical byproducts.
Factors for Selecting the Best Water Filter
- Water Source Quality
Test source water for particulates, hardness, and biological contaminants.
- Process Water Purity Requirements
Match filter technology to end-product specifications.
- Operating Costs and ROI
Consider energy use, maintenance, and replacement frequency.
- Integration with Mixer Systems
Ensure compatibility with existing plumbing, flow rates, and automation controls.
Maintenance Best Practices
- Scheduled Filter Replacement
Follow manufacturer guidelines; use sensors where possible.
- Periodic System Audits
Check for leaks, bypasses, and drops in pressure.
- Recordkeeping
Log water quality, filter changes, and associated downtime.
Authoritative Sources
- U.S. Environmental Protection Agency (EPA): Water Treatment Technologies
- Centers for Disease Control and Prevention (CDC): Water Treatment Guidance
- Industry Reports: Frost & Sullivan – “Global Industrial Water Filtration Market” (2023)
Key Takeaways
- The best water filter for industrial mixers is one that balances filtration efficiency, flow rate, chemical resistance, and cost-effectiveness.
- Selection depends on water source, process needs, and system compatibility.
- Regular maintenance and monitoring maximize both water quality and equipment lifespan.
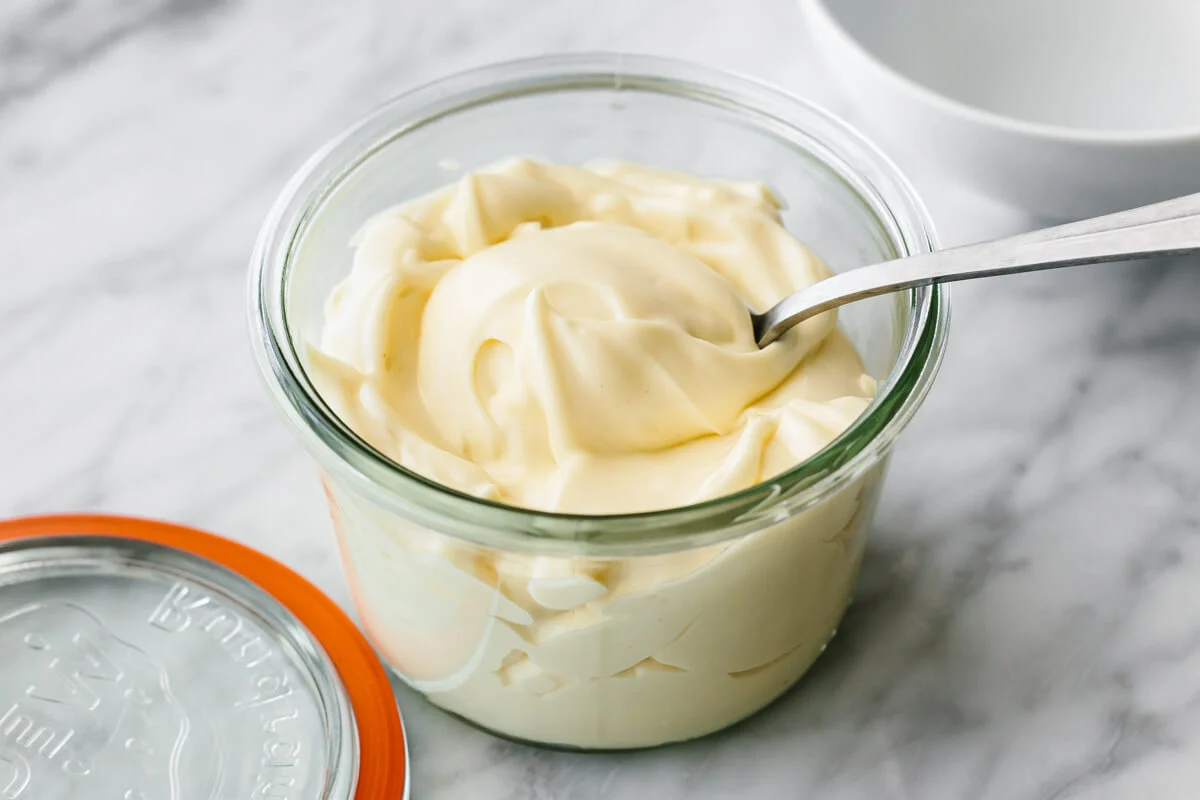
Mayonnaise Manufacturing Process Explained: How Factories Produce Mayonnaise

Water in Oil Emulsion: Meaning, Real-Life Examples, and How to Fix It
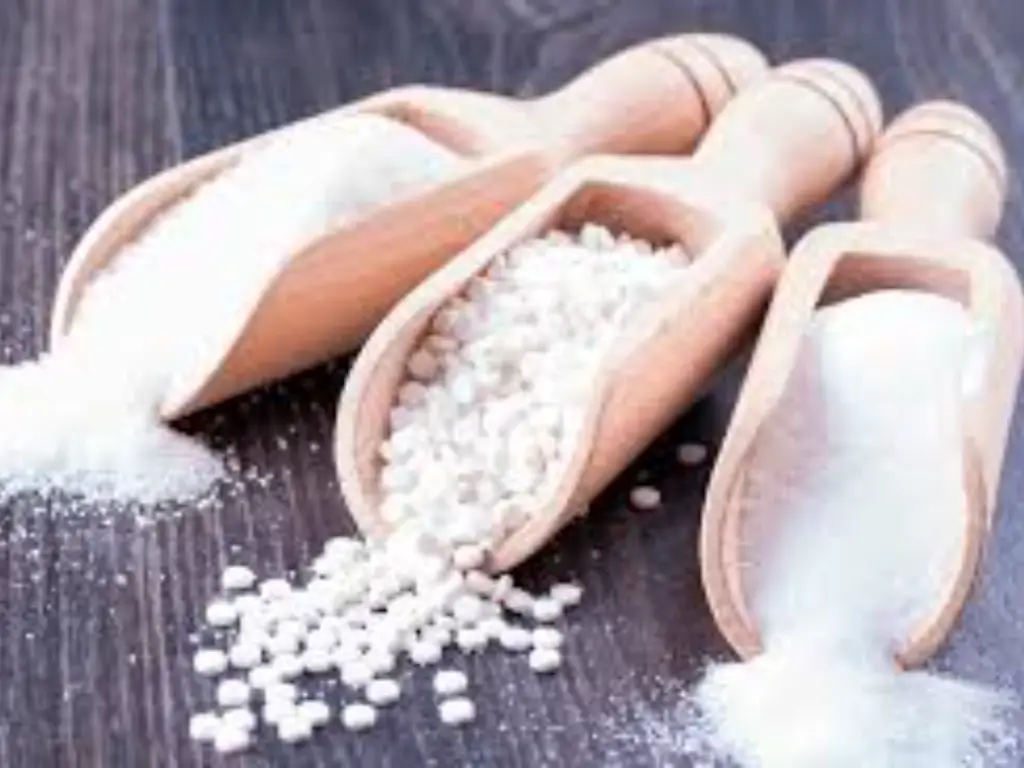
How Artificial Sweeteners Are Made: Inside the Manufacturing Process & Key Equipment
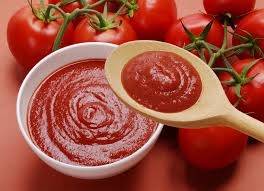
Ketchup Explained: From Ancient Origins to Modern Production Methods
How Lotion Is Made: Step-by-Step Guide for Home and Factory Production
Ribbon mixer
How long does it take to produce the ribbon blender powder machines?
The leading time is about 20-30 days. To ensure quality, the ribbon powder mixer is worth the wait.
Horizontal Filling Machine
How long is the suction hose?
This hose is about 1.3 meters long. Can be longer upon requirements.
Vacuum Homogneizer
What capacity do you recommend for a new factory?
Vacuum homogenizer is a little expensive, and the dimension is big,compared with non-vacuum type. As a start, small capacity from 50-500L is recommended if client has limit budget. Later bigger capacity 500-5000L is considered to expand business.
For easy shipment,50-1000L is often recommended for vacuum type.
Food
Do you support international shipping and installation?
Yes, we provide global delivery services and offer international installation and commissioning services to ensure you can smoothly use the equipment for production.
FAQs
Do you provide installation service locally?
Yes,we can provide installation service.Generally we’ll send one or two technicians to install your machines ordered from us. You should take care of round-trip tickets, hotels, meals and other accommodations. Daily wage for each person is USD100.
But actually,most products are installed before shipment and some are packed as a complete set. When you receive them,normally you only need to install simply. No need to ask professional engineer for help.
Leave a message
Have any questions or concerns about our products? Please leave us a message here, and our team will get back to you promptly.
Facebook
YouTube
LinkedIn
Whatsapp: +8613434139712
Guangzhou Yuanyang Machinery