how to clean cup sealing machine? | YUANYANG Guide
- How to Clean Cup Sealing Machine?
- How to Clean Cup Sealing Machine?
- Why Clean Cup Sealing Machines Regularly?
- Essential Cleaning Tools & Supplies
- Step-by-Step: Cleaning Cup Sealing Machine
- Preparation
- Disassembly
- Surface Cleaning
- Sanitizing
- Component Cleaning
- Reassembly & Inspection
- Frequency of Cleaning
- Key Safety Considerations
- Documentation and Compliance
- Final Recommendations
How to Clean Cup Sealing Machine?
Professionals in the industrial mixer sector require meticulous cleaning of equipment like cup sealing machines to ensure hygiene, prevent cross-contamination, and maintain performance. This knowledge article covers step-by-step instructions on how to clean cup sealing machine components, integrating best practices and industry standards.
How to Clean Cup Sealing Machine?
Cup sealing machines are integral in beverage processing and packaging; keeping them clean is key to operational efficiency and safety. This guide covers detailed, efficient cleaning procedures adapted for industrial mixer professionals, optimized for quick reference and maximum clarity.
Why Clean Cup Sealing Machines Regularly?
- Preserves food safety and prevents microbial contamination (Source: *FDA Food Code 2017*)
- Prevents buildup of adhesive, residue, or product, which could impair machine performance
- Extends machine lifespan, reducing maintenance costs
- Meets regulatory and internal audit requirements
Essential Cleaning Tools & Supplies
- Non-abrasive cleaning cloths and sponges
- Food-safe sanitizing agents (comply with *NSF/ANSI Standard 3-A*)
- Soft-bristle brushes for hard-to-reach areas
- Personal protective equipment (PPE)
- Clean water supply for rinsing
Step-by-Step: Cleaning Cup Sealing Machine
Preparation
- Disconnect the cup sealing machine from all power sources and allow to cool.
- Remove any leftover product and consumables (cups, film).
Disassembly
- Consult the machine’s user manual before disassembly.
- Remove seal ring, pressing plates, and other detachable parts.
Surface Cleaning
- Wipe all accessible surfaces with a soft, damp cloth using a mild detergent.
- Avoid excessive moisture near electronic or motor components.
Sanitizing
- Apply food-safe sanitizer to surfaces in contact with consumables.
- Use brushes to clean textured or hard-to-reach surfaces.
Component Cleaning
- Soak removable parts in warm, soapy water; scrub gently.
- Rinse thoroughly and sanitize before drying.
Reassembly & Inspection
- Ensure all parts are fully dry before reassembling.
- Inspect for wear, damage, or residue before reactivation.
Frequency of Cleaning
- Daily: Light wipe-down and removal of visible debris after each shift.
- Weekly: Deep cleaning with full disassembly and sanitization.
- As Needed: Immediate cleaning after spills, heavy use, or production of allergenic or sticky products.
Key Safety Considerations
- Always follow manufacturer’s recommendations for detergents and sanitizers.
- Never submerge electrical parts in water.
- Verify all seals and fittings before restarting equipment to prevent leaks or malfunction.
Documentation and Compliance
- Maintain cleaning logs per HACCP (Hazard Analysis Critical Control Point) principles.
- Regular staff training ensures consistency and upholds industry best practices.
- Reference jurisdictional sanitation codes (e.g., FDA, EU Hygiene Regulation EC 852/2004).
Final Recommendations
- Schedule regular maintenance checks to accompany cleaning.
- Use only approved cleaning agents.
- Replace worn parts promptly to avoid contamination risks.
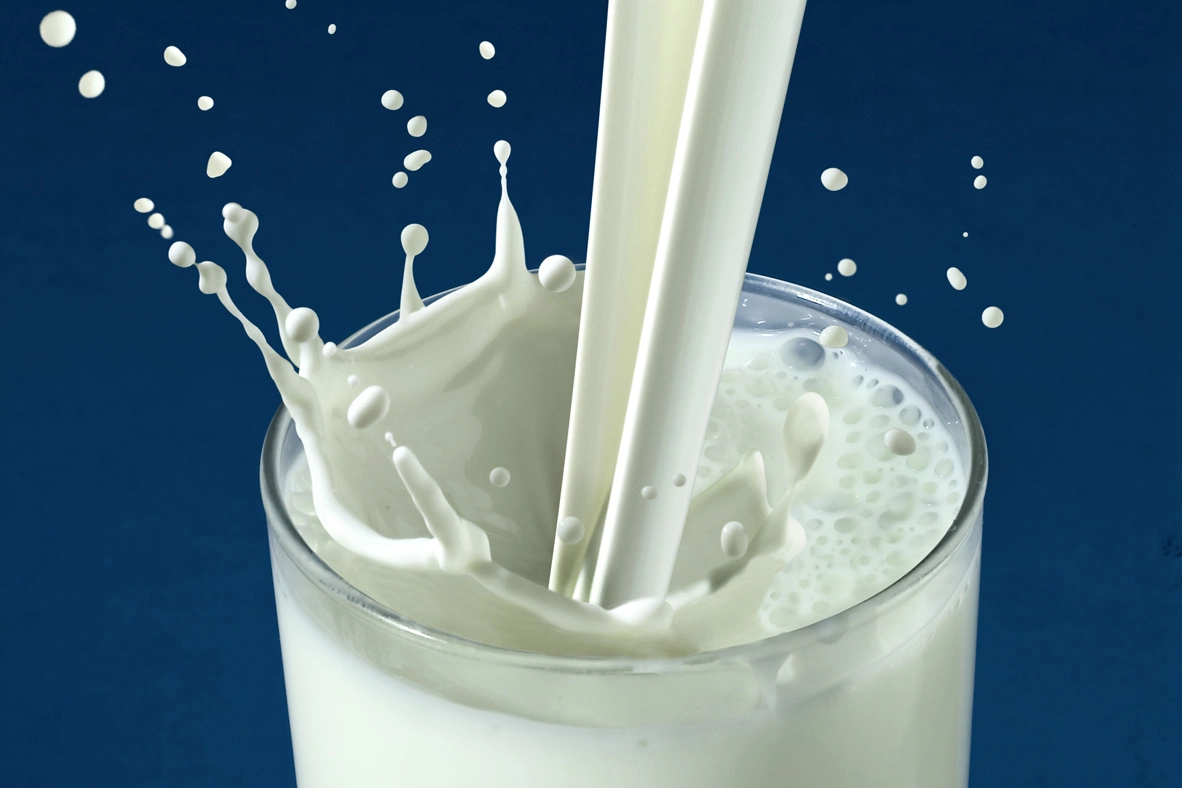
Milk Homogenization Process: Everything You Need to Know About How It Works
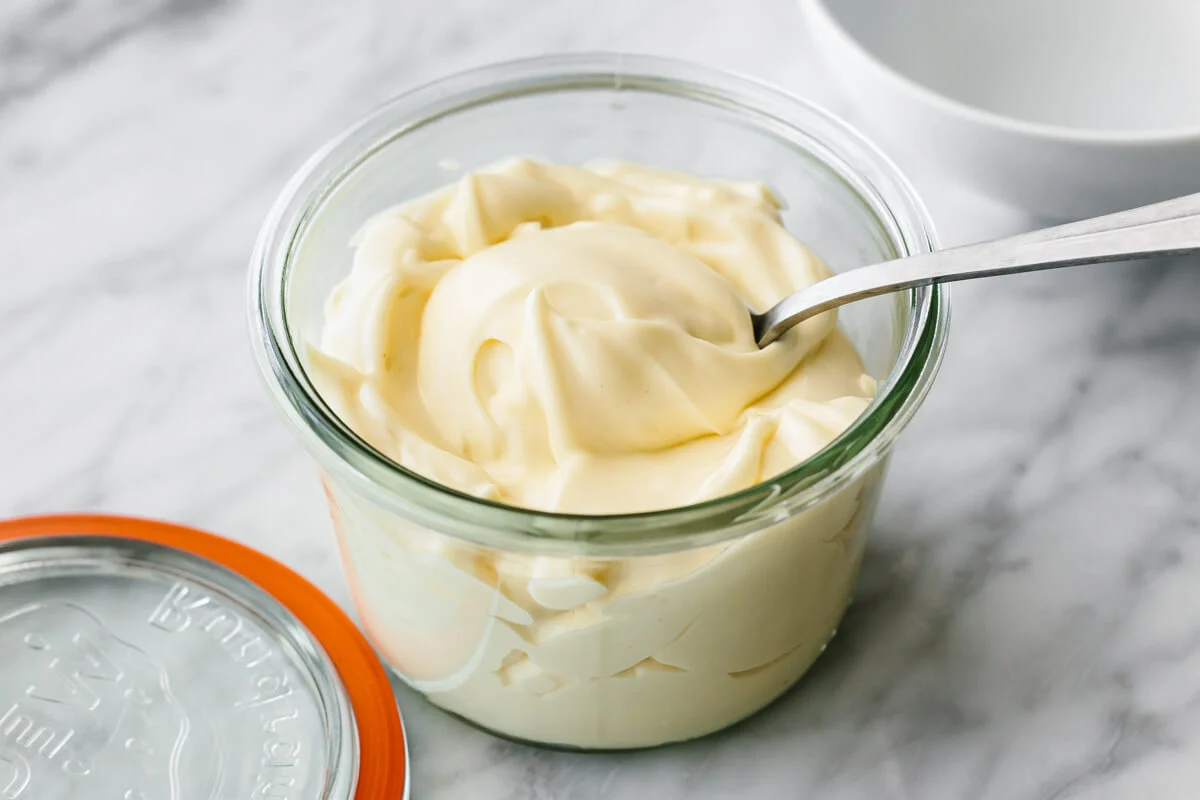
Mayonnaise Manufacturing Process Explained: How Factories Produce Mayonnaise

Water in Oil Emulsion: Meaning, Real-Life Examples, and How to Fix It
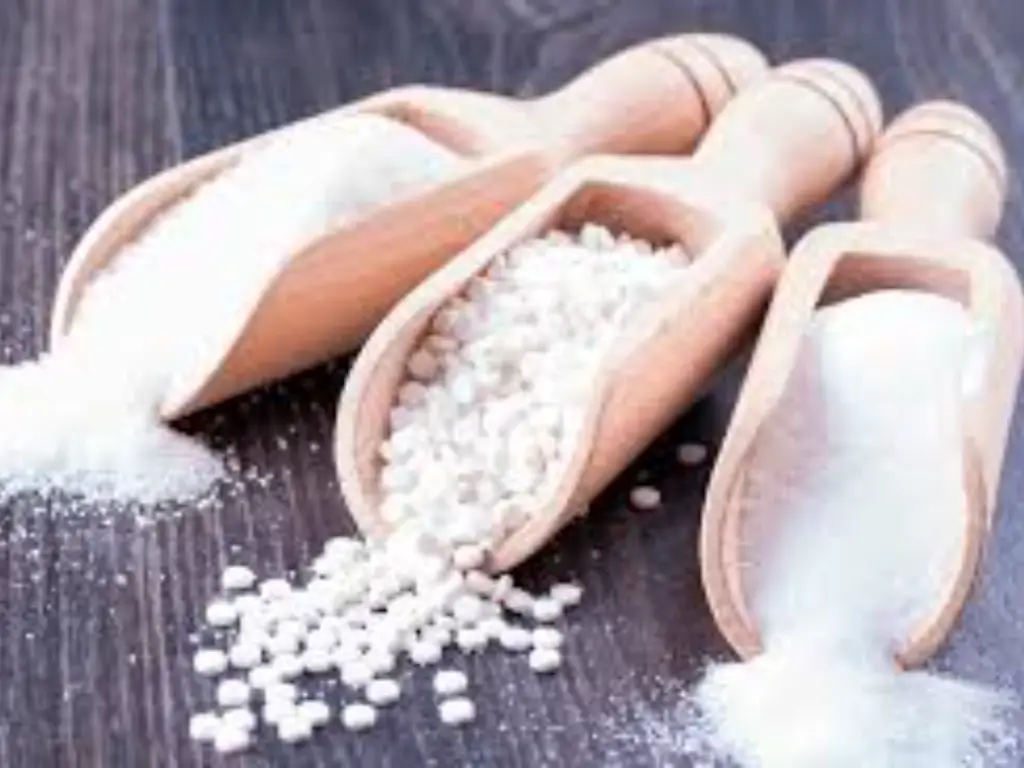
How Artificial Sweeteners Are Made: Inside the Manufacturing Process & Key Equipment
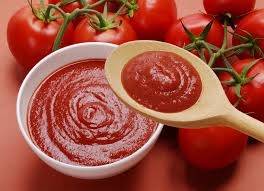
Ketchup Explained: From Ancient Origins to Modern Production Methods
Horizontal Filling Machine
What kind of liquids does this liquid bottling machine can fill?
It can fill various liquids products, such shampoo, cream, conditioner, detergent, lotion, sauce, and so on. The materials must be easy to flow down for this cream filler machine. For too viscous paste, pressurized filling machine or hot filling machine will be recommended based on materials. Please send your materials to check.
Powder Sachet Packaging Machine
What type of powders is the plastic bag packing machine suitable for?
The packing machinery for powders include various types such tea powder, walnut powder, mini granules, coffee powder, corn powder, rice powder, milk powder, etc.
Semi automatic powder filling machine
Can you customize the nozzle size to fit my different container?
Yes, we customize nozzle for clients according specific packages.
Industries
Do you offer customization services?
Yes, we support personalized design of equipment and adjustments based on specific customer needs.
Food
Do you support international shipping and installation?
Yes, we provide global delivery services and offer international installation and commissioning services to ensure you can smoothly use the equipment for production.
Leave a message
Have any questions or concerns about our products? Please leave us a message here, and our team will get back to you promptly.
Facebook
YouTube
LinkedIn
Whatsapp: +8613434139712
Guangzhou Yuanyang Machinery