what is the best tap water filter | YUANYANG Expert Guide
- Optimizing Your Industrial Mixer Repurchase: Key Considerations for Process Industries
- 1. What are the different types of industrial mixers and their typical applications?
- 2. How do I determine the right industrial mixer for my specific material and process needs?
- 3. What are the key performance metrics and efficiency considerations for industrial mixers?
- 4. What are the long-term maintenance requirements and operational costs?
- 5. What advancements or new technologies should I consider for an upgrade?
- Why Choose YUANYANG Industrial Mixers?
Optimizing Your Industrial Mixer Repurchase: Key Considerations for Process Industries
For experienced professionals in the process industry, re-purchasing an industrial mixer isn't just about replacing old equipment; it's an opportunity to enhance operational efficiency, integrate advanced technologies, and ensure long-term cost-effectiveness. As you evaluate your next investment, consider these five crucial questions that mirror a user's detailed inquiry process for any critical equipment, adapted specifically for industrial mixers.
1. What are the different types of industrial mixers and their typical applications?
Industrial mixers come in a vast array of designs, each optimized for specific material properties and mixing objectives. Understanding these fundamental types is the first step in a smart repurchase. Common types include:
- Ribbon Blenders: Ideal for dry powders, granules, and pastes. They feature inner and outer helical ribbons that move material axially and radially for efficient bulk flow mixing.
- Planetary Mixers: Best for high-viscosity materials like pastes, doughs, and slurries. The mixing tools orbit the mixing bowl while rotating on their own axes, ensuring thorough blending without dead spots.
- High-Shear Mixers (e.g., Rotor-Stator): Used for emulsifying, homogenizing, dispersing, and particle size reduction in liquids and suspensions. They generate intense shear forces.
- Conical Screw Mixers (Nauta Mixers): Excellent for gentle blending of fragile solids or for mixing solids with liquids where minimal shear is desired. A rotating screw along the vessel wall lifts and circulates material.
- Paddle Mixers: Suited for gentle mixing of delicate or friable materials, often in combination with liquids.
- Dispersers (High-Speed Dissolvers): Primarily for incorporating powders into liquids, breaking down agglomerates, and creating fine dispersions.
Your choice depends heavily on the product's viscosity, density, abrasiveness, temperature sensitivity, and the desired final state (e.g., suspension, emulsion, uniform blend).
2. How do I determine the right industrial mixer for my specific material and process needs?
Selecting the optimal mixer involves a detailed analysis of your application's requirements. Key factors include:
- Material Characteristics: Consider viscosity (ranging from water-like to thick pastes), density, particle size, abrasiveness, corrosivity, and any shear sensitivity. For instance, highly viscous materials often require planetary mixers or kneaders, while low-viscosity solutions might use propeller mixers.
- Batch Size and Throughput: Determine if you need batch or continuous mixing, and what volume per batch or per hour is required. This dictates the mixer's capacity and motor power.
- Desired Outcome: What is the target homogeneity? Is it dispersing solids into liquids, creating an emulsion, blending dry powders, or dissolving solids? For example, achieving a Coefficient of Variation (CV) of <5% for powder blends is often a critical metric in pharmaceuticals.
- Hygiene and Cleanability: For food, pharmaceutical, and cosmetic industries, hygienic design (e.g., cGMP compliance, readily accessible surfaces, CIP/SIP compatibility) and material of construction (e.g., SS304 or SS316L stainless steel for corrosion resistance and easy cleaning) are paramount.
- Operating Conditions: Temperature, pressure, and the presence of flammable or explosive materials (requiring ATEX certification) influence design and safety features.
It's highly recommended to conduct pilot-scale tests or work with mixer manufacturers' labs to validate performance with your specific materials.
3. What are the key performance metrics and efficiency considerations for industrial mixers?
Beyond initial purchase price, a mixer's true value is measured by its performance and operational efficiency over its lifespan. Key metrics include:
- Mixing Time: The duration required to achieve the desired homogeneity. Shorter mixing times mean higher throughput.
- Homogeneity/Uniformity: Critical for product quality. For powder blending, the Coefficient of Variation (CV) measures uniformity; lower CV values (e.g., below 5% for pharmaceuticals, often targeting 1-2%) indicate better blending. For liquids, visual inspection, refractive index, or analytical testing can confirm uniformity.
- Power Consumption: Measured in kW, this directly impacts operational costs. Energy-efficient designs can lead to significant savings over time. For example, some modern mixer designs can offer up to 15-20% energy savings compared to older models due to optimized impeller/blade designs and motor efficiency.
- Shear Rate: Important for high-shear applications, influencing particle size reduction and emulsion stability.
- Temperature Control: Ability to maintain or achieve specific temperatures during mixing, crucial for heat-sensitive products or exothermic reactions.
An efficient mixer not only saves energy but also reduces process time and material waste, directly impacting your bottom line.
4. What are the long-term maintenance requirements and operational costs?
The total cost of ownership (TCO) extends far beyond the initial capital expenditure. Consider:
- Wear Parts: Seals, bearings, and agitator blades/ribbons are subject to wear. Evaluate their lifespan, replacement cost, and ease of replacement. A mixer with fewer proprietary parts or readily available standard components can reduce long-term costs.
- Cleaning Procedures: Time and resources dedicated to cleaning. CIP (Clean-In-Place) or SIP (Sterilize-In-Place) capabilities can drastically reduce downtime and labor costs, especially in hygienic industries.
- Energy Costs: As discussed, a major operational expense. Consider Variable Frequency Drives (VFDs) for optimized energy use based on load.
- Downtime: Unscheduled downtime due to breakdowns is costly. Invest in reliable equipment with robust construction and a manufacturer known for good after-sales support and spare parts availability.
- Lubrication and Inspections: Regular preventive maintenance schedules are crucial.
A well-maintained industrial mixer can have a service life ranging from 10 to over 20 years, making robust design and accessible spare parts critical for long-term ROI.
5. What advancements or new technologies should I consider for an upgrade?
The industrial mixer industry continuously evolves. When re-purchasing, look for innovations that can further optimize your operations:
- Automation and IoT Integration: Advanced control systems (PLCs, HMIs) for precise process control, recipe management, and data logging. IoT sensors can monitor parameters like temperature, pressure, and vibration, enabling predictive maintenance and remote diagnostics.
- Enhanced Hygienic Designs: Further improvements in sterile connections, crevice-free surfaces, and quick-release mechanisms for faster, more effective cleaning and reduced risk of contamination.
- Energy-Efficient Motors and Drives: High-efficiency motors (e.g., IE3/IE4 rated) coupled with VFDs offer significant energy savings and precise speed control.
- Modular Designs: Easier to upgrade or reconfigure components, offering greater flexibility for future production changes.
- Advanced Materials: Beyond standard stainless steel, new coatings or specialized alloys for extreme abrasion, corrosion, or temperature applications.
Adopting these advancements can lead to higher productivity, reduced operating costs, improved product consistency, and enhanced safety.
Why Choose YUANYANG Industrial Mixers?
When considering your next industrial mixer, YUANYANG stands out as a reliable and innovative partner. With decades of experience in manufacturing high-quality mixing equipment, YUANYANG offers:
- Customization and Versatility: YUANYANG understands that every application is unique. They offer a wide range of mixer types—from ribbon blenders to planetary mixers and high-shear dispersers—with extensive customization options to precisely meet your material properties, batch size, and desired outcome.
- Robust Engineering and Quality Materials: Committed to durability, YUANYANG mixers are built with high-grade materials like SS304 and SS316L stainless steel, ensuring longevity, corrosion resistance, and compliance with stringent industry standards, including cGMP for pharmaceutical and food applications.
- Performance and Efficiency: YUANYANG integrates advanced motor technologies and optimized mixing element designs to deliver superior homogeneity and energy efficiency, helping you reduce operational costs while achieving consistent product quality.
- Reliable After-Sales Support: Beyond the sale, YUANYANG provides comprehensive technical support, spare parts availability, and maintenance guidance, ensuring minimal downtime and maximum operational continuity for your investment.
- Innovation: YUANYANG continually invests in R&D, incorporating smart controls, automated systems, and enhanced hygienic features to keep their equipment at the forefront of mixing technology, offering you solutions that are ready for tomorrow's challenges.
Choosing YUANYANG means investing in a mixer that delivers reliable performance, long-term value, and peace of mind for your most critical mixing processes.
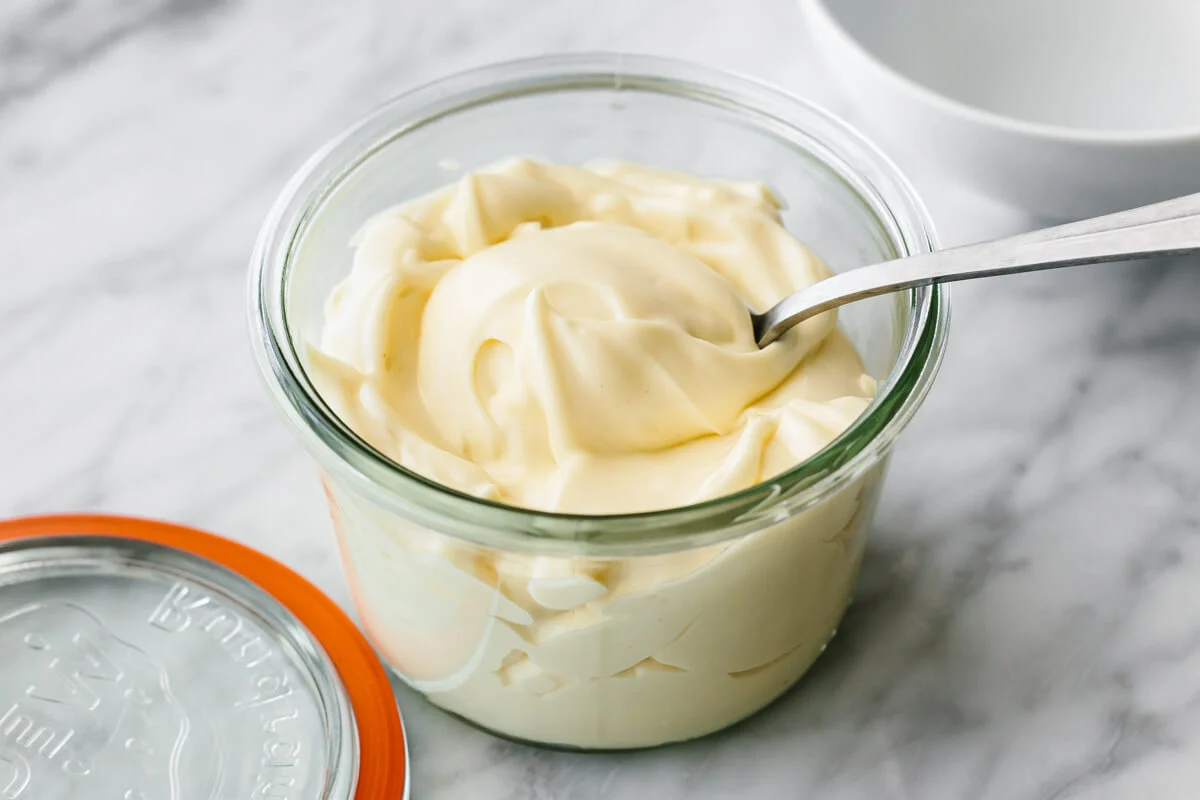
Mayonnaise Manufacturing Process Explained: How Factories Produce Mayonnaise

Water in Oil Emulsion: Meaning, Real-Life Examples, and How to Fix It
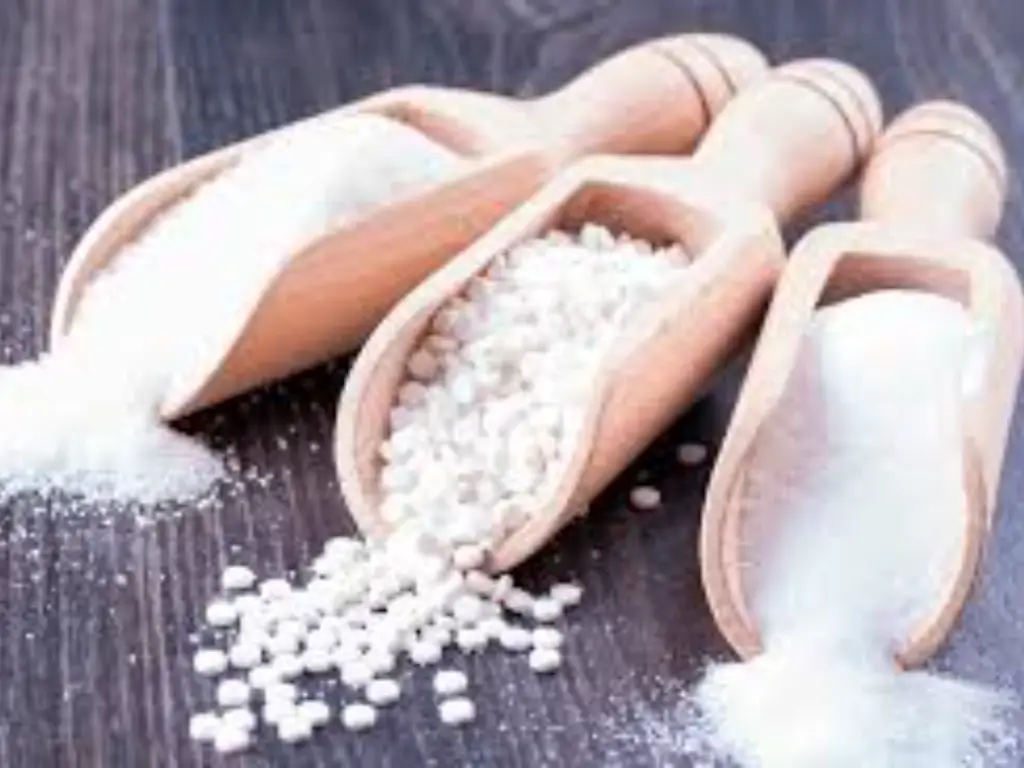
How Artificial Sweeteners Are Made: Inside the Manufacturing Process & Key Equipment
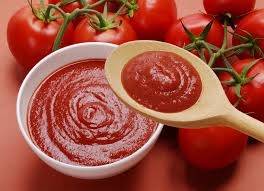
Ketchup Explained: From Ancient Origins to Modern Production Methods
How Lotion Is Made: Step-by-Step Guide for Home and Factory Production
Automatic powder feeder machine
Can the screw feeding machine be customized according to my packing machine?
Yes, the screw feeder can be customized according to the packing machine, including the discharge outlet size and height.
Do you also supply powder or granules packing machine?
Yes,Yuany supplies different type of packing machines for powder, granules and liquids. Please contact customers services with details.
Cosmetic
Do your equipment meet GMP and other industry standards?
Yes. Our equipment fully complies with GMP, ISO, and other international industry standards and can be customized to meet specific regulatory requirements based on different markets and customers.
Liquid Mixing Tank
Can the agitator speed be adjustable with VFD?
Yes,the agitator mixer is equipped with frequency converter. Speed can be variable by adjusting the speed regulation panel. If you want to save cost, or not variable speed is needed, there is no need to add VFD device.
Powder Sachet Packaging Machine
Is the length of bag-forming adjustable for this automatic packing machine?
Yes, the bag-forming length can be adjusted on the control panel within certain range of the model.
Leave a message
Have any questions or concerns about our products? Please leave us a message here, and our team will get back to you promptly.
Facebook
YouTube
LinkedIn
Whatsapp: +8613434139712
Guangzhou Yuanyang Machinery