which is the best water filter | YUANYANG Guide
- Which Is the Best Water Filter for Industrial Mixers?
- Why Water Filtration Matters in Industrial Mixing
- Key Types of Water Filters for Industrial Applications
- How to Choose the Best Water Filter for Your Mixer
- Recommended Filter Brands and Systems
- Common Signs Your Water Filter Needs Upgrade
- References:
- Conclusion:
Which Is the Best Water Filter for Industrial Mixers?
Industrial mixing processes depend on high water quality, but unfiltered water often introduces contaminants that reduce equipment lifespan and product quality. This article explores which is the best water filter for industrial mixers, addressing professionals’ needs for efficiency, compliance, and reliability.
Why Water Filtration Matters in Industrial Mixing
- Equipment Longevity:
- Proper water filtration minimizes scale, corrosion, and buildup in mixer components (Source: NSF International).
- Product Quality:
- Removes impurities and particulates, ensuring consistent, contaminant-free batch outputs.
- Energy and Maintenance Savings:
- Clean water reduces unplanned downtime, lowers energy consumption, and extends maintenance intervals.
- Regulatory Compliance:
- Meets industry-specific water standards (e.g., FDA, ASTM) for food/bev, pharma, and chemical mixing lines.
Key Types of Water Filters for Industrial Applications
- Sediment Filters:
- Captures large particles (sand, silt, rust).
- Essential as a first-stage pre-filter.
- Carbon Filters:
- Absorbs chlorine, organics, and odors.
- Protects sensitive processes and prevents product contamination.
- Reverse Osmosis (RO) Systems:
- Removes up to 99% of dissolved salts, bacteria, and heavy metals.
- Ideal for ultrapure water needs.
- Ultraviolet (UV) Disinfection Units:
- Targets bacteria and viruses without chemicals.
- Common in pharmaceutical and food industry setups.
- Automatic Self-Cleaning Filters:
- Reduces manual filter maintenance.
- Suitable for continuous, high-volume mixing environments.
How to Choose the Best Water Filter for Your Mixer
- Assess Water Source Quality:
- Conduct water testing for TDS, pH, hardness, and microbial content (Reference: American Water Works Association).
- Define Process Requirements:
- Identify critical quality factors for your mixing process—product safety, taste, or chemical purity.
- Match Flow Rate and Volume:
- Select filters rated for your plant’s peak water demand to avoid pressure drops or bottlenecks.
- Consider Maintenance and Lifecycle Costs:
- Evaluate ease of filter change, automation features, and total cost of ownership.
- Compliance and Certification:
- Choose filters certified by recognized standards (NSF, ISO).
Recommended Filter Brands and Systems
- Parker Hannifin, Pentair, and 3M:
- Renowned for robust industrial filtration.
- YUANYANG Water Filtration Solutions:
- Custom-designed for industrial mixer applications; supports integration and aftersales service.
Common Signs Your Water Filter Needs Upgrade
- Increased mixer downtime due to scaling or blockages.
- Visible sediment in mixed batches.
- Monitor spikes in water pressure or unexplained taste/odor issues.
References:
1. NSF International – Water Quality Standards
2. American Water Works Association – Water Filtration Best Practices
3. U.S. EPA – Industrial Water Use and Treatment
Conclusion:
Selecting the best water filter is critical for mixer reliability, product quality, and operational efficiency. YUANYANG offers tailored filtration solutions and expert support for the industrial mixer industry. For a personalized assessment, contact YUANYANG’s water filtration experts.
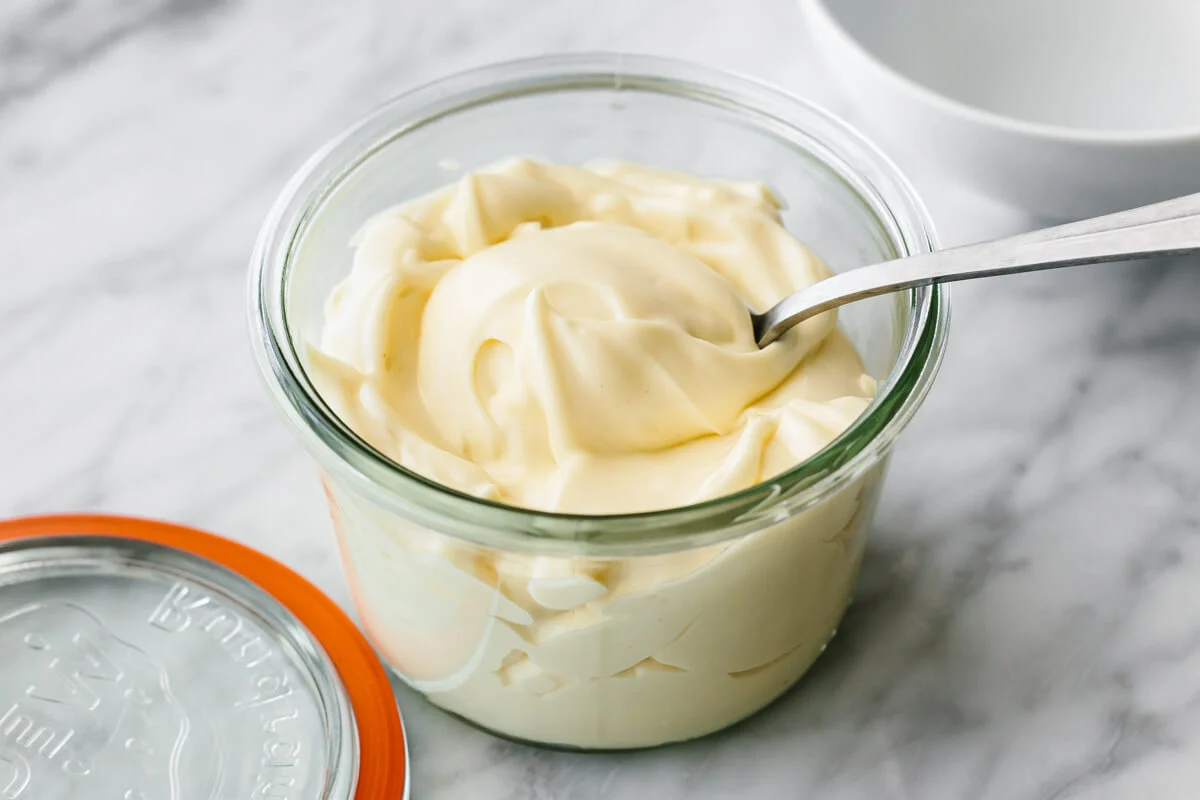
Mayonnaise Manufacturing Process Explained: How Factories Produce Mayonnaise

Water in Oil Emulsion: Meaning, Real-Life Examples, and How to Fix It
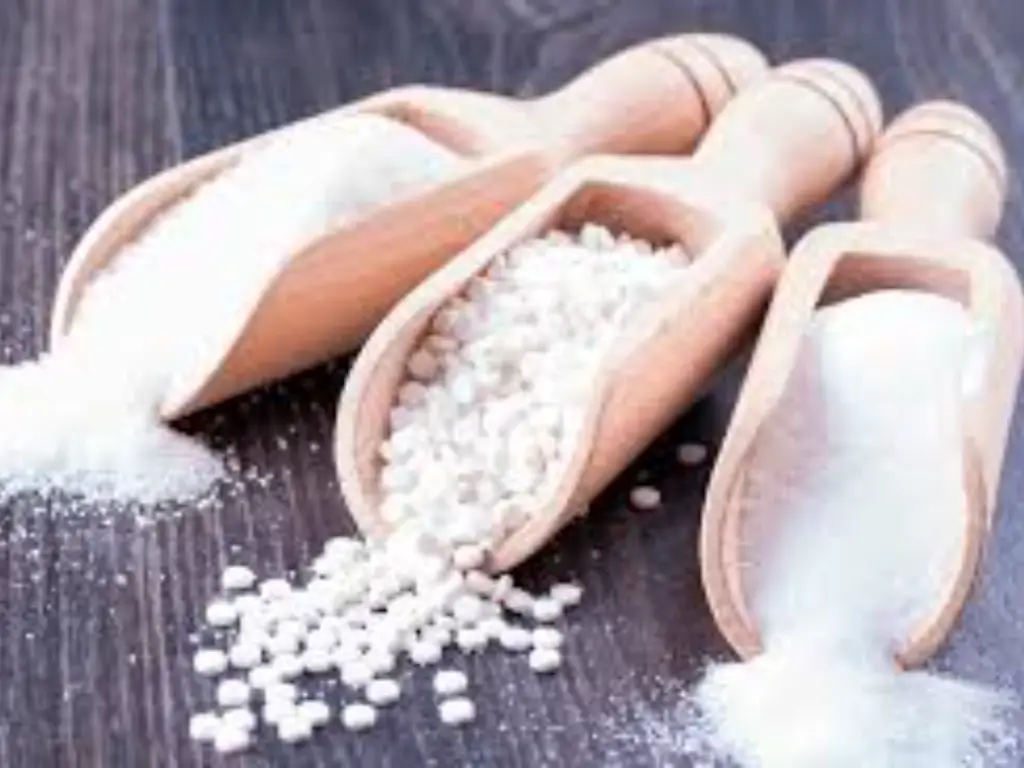
How Artificial Sweeteners Are Made: Inside the Manufacturing Process & Key Equipment
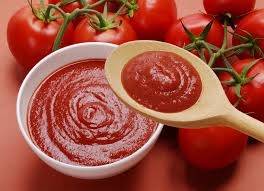
Ketchup Explained: From Ancient Origins to Modern Production Methods
How Lotion Is Made: Step-by-Step Guide for Home and Factory Production
Semi Automatic Double Sides Labeling Machine
What types bottles are suitable for this label dispenser?
It is suitable for single side and double side labeling of flat bottles, round bottles and square bottles, such as shampoo, laundry detergent flat bottles, lubricating oil flat bottles, hand sanitizer round bottles and other double side labeling, both sides of the same labeling, double labeling improves production efficiency, and is widely used in daily chemical, cosmetics, petrochemical, pharmaceutical and other industries.
Semi automatic powder filling machine
Do you supply the powder feeder for the powder filler machine?
Yes, we also supply powder feeding machine. It is recommended to purchase a complete set including the auger feeder machine.
Washing Powder
Do you offer warranties and after-sales service?
Yes, we provide warranties and comprehensive after-sales support to ensure uninterrupted production and equipment reliability.
Automatic Piston Filling Machine
Can the filling machine be connected with other machines, such as capping machine, bottle sorting machine?
Yes, this pneumatic filling machine is one of the complete filling line machines, user can tell the conveyor height of his current machine, we shall customize accordingly. If client buy a complete line from us, we will make every machine in a line or according to space.
Sachet Packaging Machine for Granules
What’s the date printing, steel printing or coding?
There are standard steel date printing on the automatic packaging machine, if clients needs coding type, just tell us to add an extra coding device.
Leave a message
Have any questions or concerns about our products? Please leave us a message here, and our team will get back to you promptly.
Facebook
YouTube
LinkedIn
Whatsapp: +8613434139712
Guangzhou Yuanyang Machinery