how ro water filter works | YUANYANG Expert Guide
- How Reverse Osmosis (RO) Water Filters Work: A Deep Dive for Industrial Applications
- What is Reverse Osmosis (RO) and How Does it Work?
- What Impurities Does an RO System Effectively Remove from Water?
- What Are the Core Components of an Industrial RO System?
- How is the Purity of RO Water Measured and Monitored?
- What Are the Key Maintenance Practices for Industrial RO Systems?
- Mastering Your Next Industrial Mixer Repurchase: Professional Insights
- Assessing Your Current Needs & Performance Gaps
- Choosing the Right Mixer Type & Configuration
- Material Science & Construction for Durability
- Automation, Control, and Energy Efficiency
- After-Sales Support, Spares, and Total Cost of Ownership (TCO)
- Why Choose YUANYANG for Your Industrial Mixer Needs?
How Reverse Osmosis (RO) Water Filters Work: A Deep Dive for Industrial Applications
In countless industrial applications, from pharmaceutical manufacturing to food processing and chemical production, water purity is not merely a preference but a stringent requirement. Reverse Osmosis (RO) stands as a cornerstone technology for achieving exceptional water quality. Understanding its mechanism is crucial for optimizing your processes.
What is Reverse Osmosis (RO) and How Does it Work?
Reverse Osmosis is a water purification technology that uses a semi-permeable membrane to remove ions, molecules, and larger particles from drinking water. Unlike standard filtration, which primarily relies on particle size exclusion, RO applies pressure to force water through the membrane, overcoming osmotic pressure. This process allows pure water molecules to pass through, while dissolved solids, salts, and other contaminants are rejected and flushed away as concentrate. In essence, it reverses the natural osmotic flow, pushing water from a higher solute concentration to a lower one, leaving impurities behind.
What Impurities Does an RO System Effectively Remove from Water?
Industrial RO systems are highly effective at removing a broad spectrum of impurities. These include but are not limited to: total dissolved solids (TDS) such as salts (e.g., sodium, chloride, calcium, magnesium), heavy metals (e.g., lead, mercury), bacteria, viruses, pesticides, herbicides, and most dissolved organic compounds. Typically, RO membranes achieve a rejection rate of 95-99% for TDS, making the filtered water ideal for applications requiring high purity, like boiler feedwater, rinse water in electronics manufacturing, or ingredient water in food and beverage production.
What Are the Core Components of an Industrial RO System?
An industrial RO system is more than just a membrane. Key components include:
- Pre-treatment Filters: Essential for removing larger particles (sediment filters) and chlorine (carbon filters) to protect the delicate RO membrane from clogging and degradation.
- High-Pressure Pump: Provides the necessary force to push water through the RO membrane, overcoming osmotic pressure.
- RO Membranes: The heart of the system, typically spiral-wound thin-film composite membranes, arranged in pressure vessels.
- Control Panel: Manages system operation, monitoring pressure, flow rates, and water quality.
- Post-treatment (Optional): Depending on purity requirements, this might include deionization (DI) resin beds for ultra-pure water, UV sterilization for microbial control, or remineralization.
How is the Purity of RO Water Measured and Monitored?
The purity of RO water is primarily measured by its Total Dissolved Solids (TDS) content, expressed in parts per million (ppm) or micrograms per centimeter (µS/cm) for conductivity. Lower TDS values indicate higher purity. Industrial systems often incorporate inline TDS or conductivity meters to continuously monitor output water quality. Regular calibration of these sensors ensures accurate readings. Water recovery rates, typically ranging from 50% to 85% in well-designed industrial systems, are also monitored to ensure efficient water usage.
What Are the Key Maintenance Practices for Industrial RO Systems?
Proper maintenance is critical for the longevity and efficiency of an industrial RO system:
- Regular Pre-filter Replacement: Changing sediment and carbon filters as per schedule prevents membrane fouling and chlorine damage.
- Membrane Cleaning: Over time, membranes can foul with scale, organic matter, or biological growth. Chemical cleaning (CIP - Clean-In-Place) is performed periodically to restore membrane performance.
- System Monitoring: Regularly checking pressures (feed, permeate, concentrate), flow rates, and TDS rejection rates helps identify issues early. A sudden drop in rejection or permeate flow indicates a problem.
- Sanitization: Periodic sanitization might be required, especially in industries like food & beverage, to prevent microbial growth within the system.
Just as water purity is fundamental to sensitive processes, the core of many industrial operations hinges on the efficiency and reliability of mixing equipment. As your business grows or production demands evolve, the decision to repurchase or upgrade your industrial mixers becomes a strategic one, impacting product quality, operational efficiency, and overall profitability.
Mastering Your Next Industrial Mixer Repurchase: Professional Insights
Repurchasing an industrial mixer is a significant investment that goes beyond simply replacing old equipment. It's an opportunity to optimize your production line, enhance product quality, and integrate modern efficiencies. Here's a guide to making an informed decision:
Assessing Your Current Needs & Performance Gaps
Before looking at new equipment, thoroughly evaluate your existing mixer's performance. Are you experiencing inconsistencies in blend uniformity (e.g., Coefficient of Variation (CV) above 5% for dry blends), longer-than-desired mixing times, energy inefficiencies, or maintenance headaches? Define your desired outcomes: increased throughput, better homogeneity for specific viscosities (e.g., up to 1,000,000 cP for planetary mixers), reduced energy consumption, or enhanced safety features. Documenting these gaps will inform your specifications for a new mixer.
Choosing the Right Mixer Type & Configuration
The vast array of industrial mixers—from high-shear dispersers and homogenizers (generating shear rates often exceeding 100,000 s⁻¹) to low-shear agitators, ribbon blenders, and planetary mixers—each serves specific applications. Consider:
- Material Properties: Viscosity, density, abrasiveness, corrosiveness, and shear sensitivity. For instance, viscous pastes often require planetary mixers or Z-blade kneaders, while low-viscosity liquids might use turbine or propeller agitators.
- Desired Output: Blending, dispersion, emulsification, dissolution, or particle size reduction.
- Batch Size & Scale-up: Ensure the new mixer can handle current and projected production volumes.
- Operating Environment: Temperature, pressure, and potentially explosive atmospheres (requiring ATEX compliance for safety).
Material Science & Construction for Durability
The materials of construction significantly impact a mixer’s lifespan and suitability for specific products. Stainless Steel 316L is a common choice, preferred over 304 for corrosive applications due to its 2-3% molybdenum content, which significantly enhances corrosion resistance, especially against chlorides. For highly corrosive or abrasive materials, exotic alloys like Hastelloy, Titanium, or specialized coatings may be necessary. Consider surface finishes (e.g., Ra <0.8 µm for pharmaceutical grades) and robust sealing mechanisms (e.g., double mechanical seals) to prevent leaks and product contamination.
Automation, Control, and Energy Efficiency
Modern industrial mixers offer advanced automation and control features. Look for integrated Programmable Logic Controllers (PLCs) with Human-Machine Interfaces (HMIs) for precise control over mixing parameters, batch consistency, and data logging. Energy efficiency is paramount; seek mixers equipped with High Quality efficiency motors (meeting standards like IE3 or IE4, offering 85-95% efficiency) and variable frequency drives (VFDs) for optimized power consumption based on load. Predictive maintenance capabilities (IoT sensors for vibration, temperature monitoring) can also extend equipment life and reduce unexpected downtime.
After-Sales Support, Spares, and Total Cost of Ownership (TCO)
The initial purchase price is just one component of the Total Cost of Ownership (TCO). Energy consumption, maintenance, and the availability and cost of spare parts often constitute 70-80% of a mixer's lifetime cost. Evaluate the manufacturer's after-sales support, warranty, and technical assistance. A reputable supplier should offer readily available spare parts, maintenance contracts, and expert troubleshooting to minimize downtime and ensure long-term operational reliability.
Why Choose YUANYANG for Your Industrial Mixer Needs?
At YUANYANG, we understand the critical role industrial mixers play in your production success. Our commitment to innovation, quality, and customer satisfaction sets us apart:
- Customized Solutions: We don't just sell mixers; we engineer bespoke solutions tailored to your unique material properties, process requirements, and production scale. Our expertise ensures you get the exact mixer for your application, whether it's for high-viscosity pastes, delicate emulsions, or abrasive slurries.
- Advanced Technology: YUANYANG mixers incorporate the latest in motor efficiency, control automation (PLC/HMI), and robust material construction, designed for optimal performance and energy savings. We leverage industry-leading design principles to deliver superior blend uniformity and throughput.
- Proven Reliability & Durability: Built with High Quality materials like SS316L and precision engineering, our mixers are designed for continuous, heavy-duty operation, minimizing maintenance needs and maximizing uptime.
- Comprehensive Support: From initial consultation and system design to installation, training, and responsive after-sales service, YUANYANG provides end-to-end support, ensuring your investment delivers consistent value for years to come.
- Global Expertise: With years of experience serving diverse industries worldwide, YUANYANG possesses the global insight and technical prowess to address even the most complex mixing challenges.
Choose YUANYANG for a partner committed to elevating your industrial mixing processes through precision, efficiency, and unwavering support.
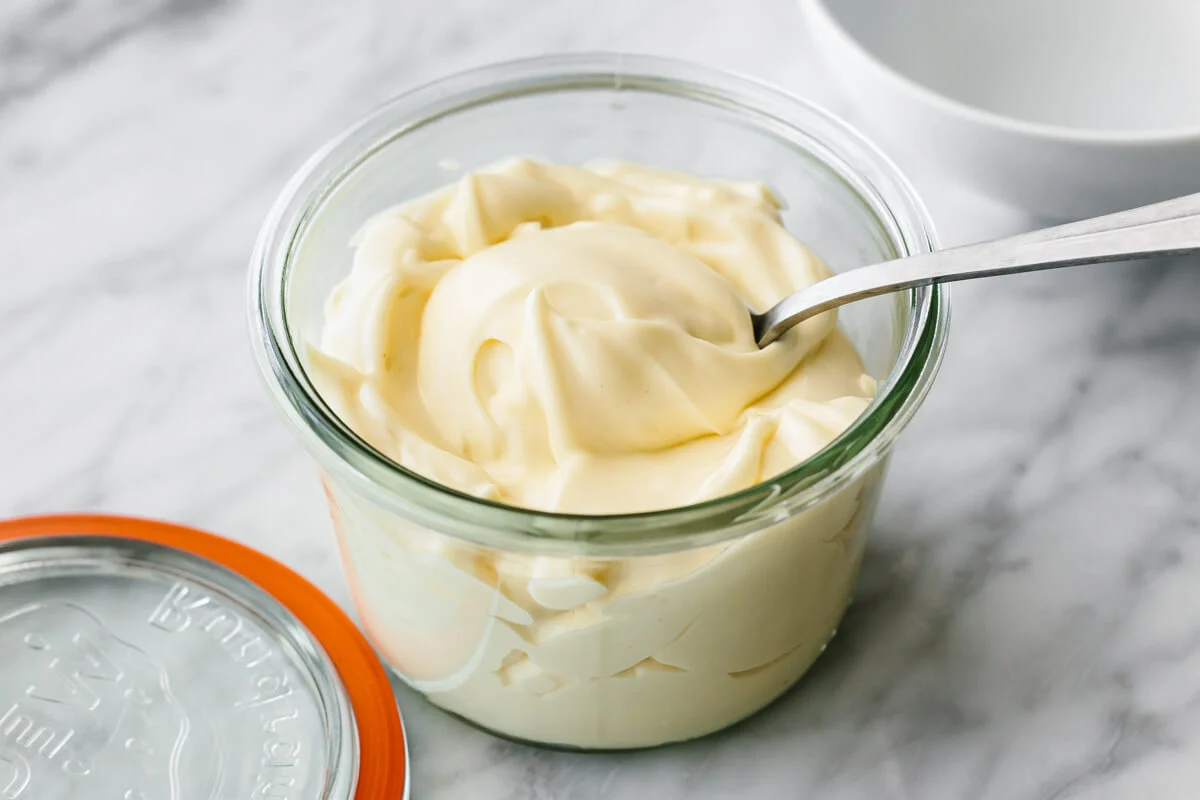
Mayonnaise Manufacturing Process Explained: How Factories Produce Mayonnaise

Water in Oil Emulsion: Meaning, Real-Life Examples, and How to Fix It
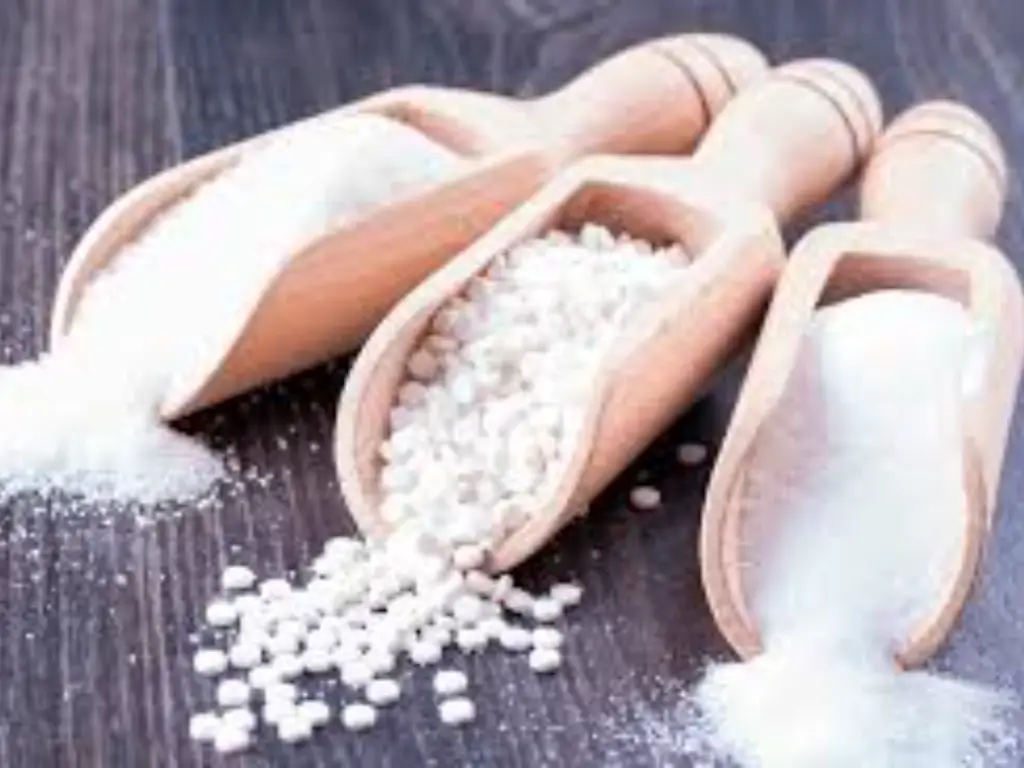
How Artificial Sweeteners Are Made: Inside the Manufacturing Process & Key Equipment
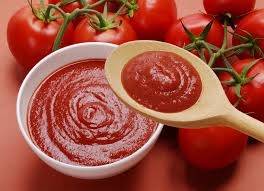
Ketchup Explained: From Ancient Origins to Modern Production Methods
How Lotion Is Made: Step-by-Step Guide for Home and Factory Production
Homogneizer mixer tank
Can I use city water to produce liquid detergent?
As you know, water takes 70-99% proportion of raw materials for liquid detergent production. So the quality of water is quite important to produce qualified liquid cleaning products. The raw water should be treated before taking into tank.
Semi Automatic Capping Machine
Can it close glass bottles?
As long as the glass bottle has screw cap, the capping machine can close its cap, although the machine is often called plastic capping machine.
Food
Which types of food can Yuanyang's equipment handle?
Yuanyang's equipment can handle various food types, including liquid, viscous, semi-liquid, and solid foods such as beverages, sauces, dairy products, pastries, candies, etc.
Washing Powder
What types of packaging does the equipment support?
Our machines accommodate various packaging formats, including bottles, bags, and small packs, to meet diverse market demands.
One Stage Water Treatment
How long to replace the reverse osmosis membrane and pvc film?
Reverse osmosis membranes are generally recommended to be replaced every year. But it is not a fixed time, the period should be considered according to the actual use environment and operating conditions.
PVC film is recommended to replace every two weeks.
Leave a message
Have any questions or concerns about our products? Please leave us a message here, and our team will get back to you promptly.
Facebook
YouTube
LinkedIn
Whatsapp: +8613434139712
Guangzhou Yuanyang Machinery