how to make labeling machine work better | YUANYANG Expert Guide
- Optimizing Industrial Mixers: A Guide for Enhanced Performance & Repurchase Decisions
- How Can I Assess If My Current Industrial Mixer Needs an Upgrade or Replacement?
- What Advanced Technologies Can Enhance the Efficiency and Performance of New Industrial Mixers?
- How Can I Minimize Operational Costs, Particularly Energy Consumption, in My Next Industrial Mixer Investment?
- What Critical Design and Material Considerations Ensure My New Mixer Meets Specific Process and Regulatory Demands?
- Beyond Purchase, What Best Practices Will Maximize the Lifespan and ROI of a New Industrial Mixer?
Optimizing Industrial Mixers: A Guide for Enhanced Performance & Repurchase Decisions
For process-driven industries, an industrial mixer is often the heart of operations. As technology evolves and production demands shift, deciding when and how to upgrade or replace your mixing equipment becomes crucial. This article delves into the key considerations for industrial mixer users looking to enhance performance, reduce costs, and ensure future-proof operations during the repurchasing cycle.
How Can I Assess If My Current Industrial Mixer Needs an Upgrade or Replacement?
Evaluating your existing industrial mixer’s performance is the first step in any repurchasing decision. Key indicators include:
- Declining Efficiency: Is your mixer taking longer to achieve desired homogeneity? Are there inconsistencies in the final product? Older designs might struggle with new material formulations or higher throughput demands.
- High Maintenance Costs & Downtime: Frequent breakdowns, expensive spare parts, or prolonged downtime directly impact profitability. If maintenance costs exceed 10-15% of the mixer’s initial value annually, it’s a strong indicator for replacement.
- Increased Energy Consumption: Older mixer models often lack energy-efficient features. According to the U.S. Department of Energy, optimizing motor systems and adopting variable frequency drives (VFDs) can lead to 20-50% energy savings in many industrial applications, including mixing.
- Regulatory Non-Compliance: Evolving industry standards (e.g., GMP, HACCP, ATEX) might render older equipment non-compliant, particularly concerning material contact surfaces, cleanability (CIP/SIP), and safety features.
- Production Bottlenecks: If your mixer cannot keep pace with increased production demands, it becomes a bottleneck, limiting overall plant capacity.
What Advanced Technologies Can Enhance the Efficiency and Performance of New Industrial Mixers?
Modern industrial mixers are integrated with advanced technologies that offer significant improvements in control, efficiency, and safety:
- Variable Frequency Drives (VFDs): Beyond energy savings, VFDs allow for precise control of mixing speed, adapting to different process stages and material viscosities, leading to optimal mixing results and reduced batch times.
- Computational Fluid Dynamics (CFD) & Simulation Software: Before manufacturing, advanced manufacturers use CFD to simulate fluid dynamics within the mixer, optimizing impeller design, tank geometry, and baffling for superior mixing efficiency and homogeneity, reducing scale-up risks.
- IoT & Industry 4.0 Integration: Smart mixers equipped with sensors can monitor critical parameters like temperature, pressure, torque, and vibration in real-time. This data facilitates predictive maintenance, improves process control, and enables remote monitoring and diagnostics, reducing unscheduled downtime by up to 25-50% according to some industry reports (e.g., Deloitte).
- Advanced Impeller Designs: Innovations in impeller geometry, such as hydrofoil impellers, offer higher pumping efficiency and better mixing effectiveness with less energy input compared to traditional designs.
- Automated Cleaning (CIP/SIP Systems): Integrated Clean-in-Place (CIP) and Sterilize-in-Place (SIP) systems significantly reduce cleaning time and manual labor, enhance hygiene, and minimize cross-contamination risk, crucial for food, pharmaceutical, and chemical industries.
How Can I Minimize Operational Costs, Particularly Energy Consumption, in My Next Industrial Mixer Investment?
Reducing operational expenditure is a primary driver for new mixer investments. Focus on:
- Optimal Sizing and Design: A mixer that is either oversized or undersized will consume more energy and perform sub-optimally. Partner with suppliers who offer detailed process analysis to ensure the mixer is perfectly matched to your application's volume, viscosity, and mixing requirements.
- High-Efficiency Motors & VFDs: As mentioned, investing in IE3 or IE4 efficiency class motors combined with VFDs provides significant long-term energy savings. The initial higher cost is often recouped within a few years through reduced electricity bills.
- Energy-Efficient Impeller Technologies: Impeller designs that maximize fluid movement with minimal power input, such as axial flow hydrofoil impellers, can dramatically lower energy consumption while improving mixing quality.
- Material of Construction & Surface Finish: Smooth, polished internal surfaces (e.g., Ra < 0.4 µm for pharmaceutical applications) reduce friction and facilitate easier, quicker cleaning, leading to less water and cleaning agent consumption and reduced labor costs.
What Critical Design and Material Considerations Ensure My New Mixer Meets Specific Process and Regulatory Demands?
Meeting industry-specific requirements is paramount for compliance and product integrity:
- Material of Construction: Stainless Steel (SS304, SS316L) is common, with SS316L preferred for corrosive environments or hygienic applications due to its superior corrosion resistance. For highly aggressive chemicals, exotic alloys like Hastelloy, Titanium, or specialized coatings may be necessary.
- Hygienic Design (Food, Pharma, Cosmetics): Adherence to GMP standards is critical. This includes smooth, crevice-free internal surfaces, sanitary seals, aseptic connections, minimal dead spaces, and easily drainable designs for effective CIP/SIP. Documentation like material certificates (e.g., FDA-approved, 3-A Sanitary Standards) and surface roughness reports are often required.
- Explosion-Proof (ATEX/IECEx): For processes involving flammable gases, dusts, or vapors, mixers must comply with ATEX (for EU) or IECEx (international) directives, featuring explosion-proof motors, controls, and static-dissipative materials.
- Sealing Solutions: The choice of shaft seal (e.g., mechanical seals, stuffing boxes, lip seals, magnetic drives) depends on product viscosity, pressure, temperature, and cleanliness requirements. Double mechanical seals with barrier fluid systems are common for hazardous or sterile applications.
- Customization Capabilities: Reputable manufacturers offer customization for tank shape, volume, heating/cooling jackets, vacuum/pressure capabilities, and specialized agitators to perfectly match unique process needs.
Beyond Purchase, What Best Practices Will Maximize the Lifespan and ROI of a New Industrial Mixer?
The true ROI of a mixer extends beyond its purchase price, encompassing its entire lifecycle:
- Implement a Robust Preventive Maintenance Program: Regular inspection, lubrication, seal checks, and component replacement as per manufacturer guidelines are vital. This minimizes unexpected breakdowns and extends operational life. For instance, regular oil analysis for gearboxes can detect wear issues before they become critical.
- Embrace Predictive Maintenance: Utilize sensor data (from IoT-enabled mixers) for vibration analysis, temperature monitoring, and motor current signature analysis. This allows for scheduled maintenance based on actual equipment condition rather than fixed intervals, reducing maintenance costs by up to 10-40% and minimizing unscheduled downtime.
- Proper Operator Training: Well-trained operators can identify potential issues early, operate the mixer within its design parameters, and perform routine checks effectively, preventing misuse and premature wear.
- Genuine Spare Parts: Always use genuine manufacturer-recommended spare parts to ensure compatibility, performance, and maintain warranty validity.
- Regular Calibration and Performance Checks: Periodically verify mixing efficiency, energy consumption, and product quality to ensure the mixer continues to meet specifications and identify any performance degradation early.
Choosing the right industrial mixer is a strategic investment. By focusing on these critical areas—assessment, technology, cost optimization, compliance, and long-term maintenance—you can ensure your next mixer enhances your operational efficiency and delivers a strong return on investment.
Why Choose YUANYANG for Your Industrial Mixer Needs?
YUANYANG stands as a leader in industrial mixing solutions, offering unparalleled advantages for your repurchase decisions:
- Customization & Expertise: With deep industry knowledge, YUANYANG provides highly customized mixing solutions tailored to your unique process, materials, and capacity requirements, ensuring optimal performance and efficiency.
- Advanced R&D & Technology: We invest heavily in research and development, integrating the latest technologies like CFD-optimized impeller designs, high-efficiency motors, and smart control systems to deliver mixers that are at the forefront of innovation and energy efficiency.
- Robust Quality & Reliability: Our mixers are constructed from High Quality materials (e.g., certified SS316L, Hastelloy) with meticulous manufacturing processes, ensuring exceptional durability, reliability, and long operational lifespans, even in demanding environments.
- Comprehensive Support: From initial consultation and design to installation, training, and responsive after-sales service, YUANYANG offers end-to-end support, maximizing your equipment's uptime and ROI.
- Compliance & Safety: We adhere to stringent international standards (e.g., GMP, ATEX, CE), providing mixers that meet the highest levels of hygiene, safety, and regulatory compliance for various industries.
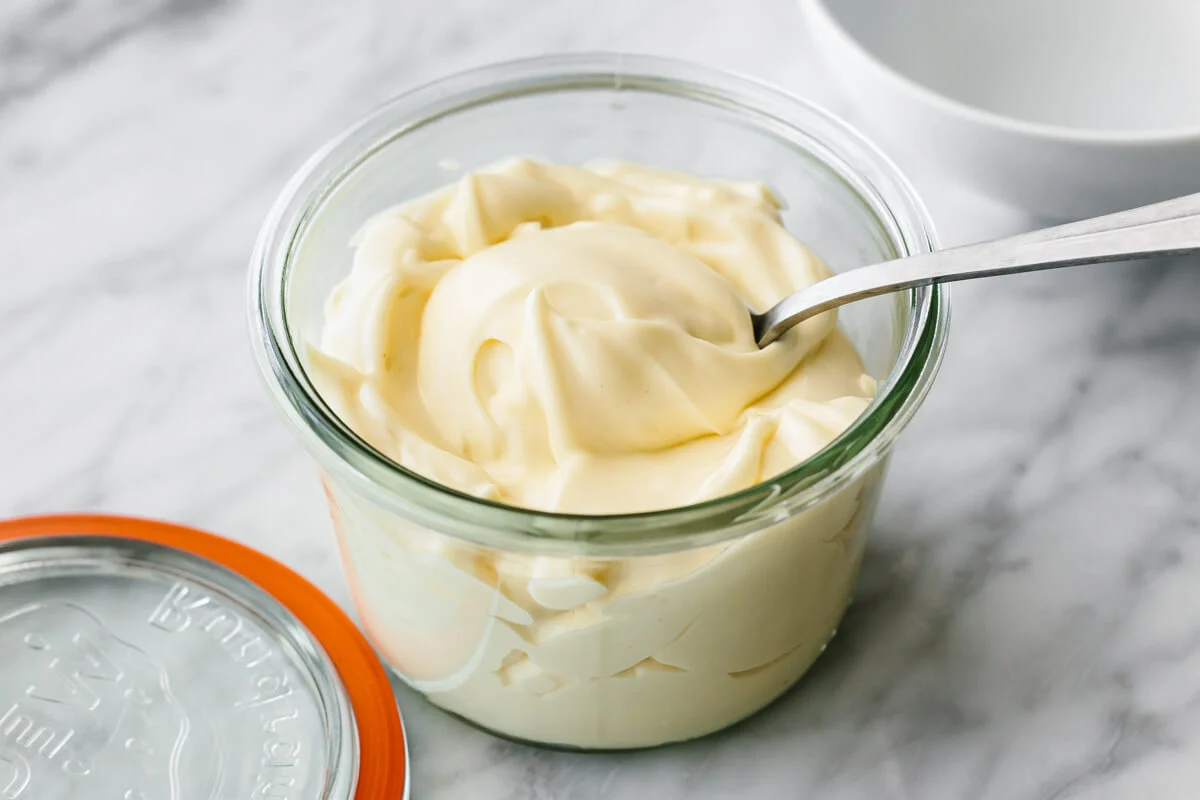
Mayonnaise Manufacturing Process Explained: How Factories Produce Mayonnaise

Water in Oil Emulsion: Meaning, Real-Life Examples, and How to Fix It
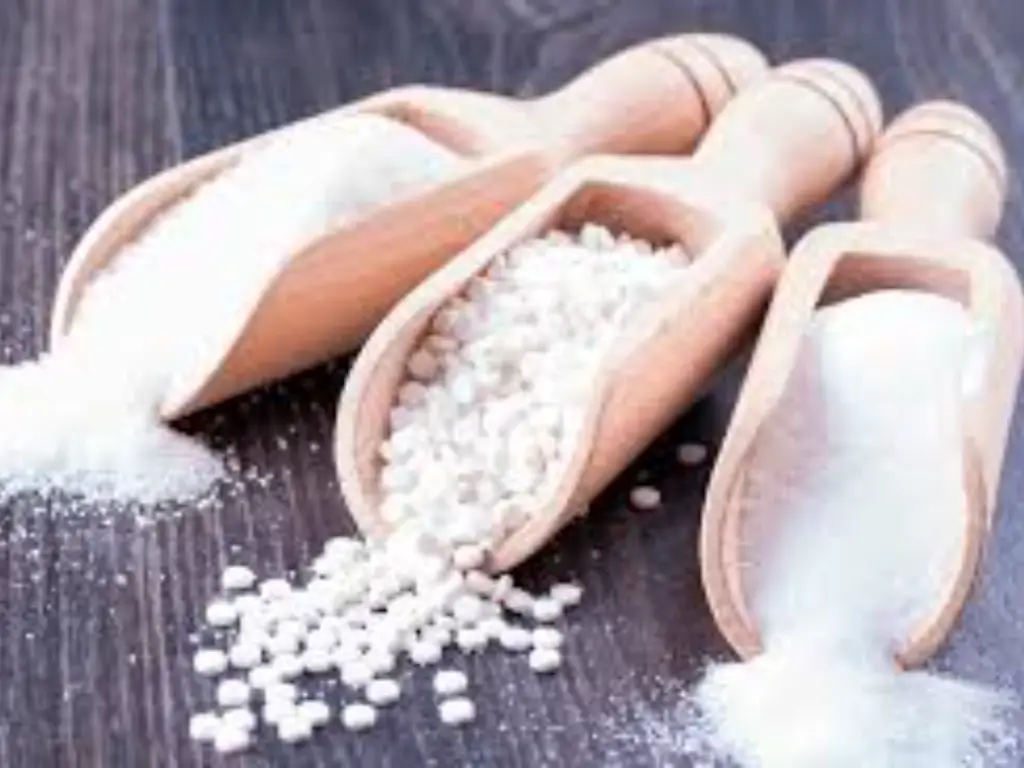
How Artificial Sweeteners Are Made: Inside the Manufacturing Process & Key Equipment
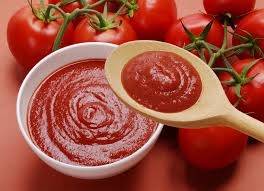
Ketchup Explained: From Ancient Origins to Modern Production Methods
How Lotion Is Made: Step-by-Step Guide for Home and Factory Production
Medicine
How can I ensure my production process is free from contamination?
Our equipment uses materials that meet the strict standards of the pharmaceutical industry and is designed for easy cleaning and maintenance. All our equipment is carefully designed to minimize the risk of cross-contamination.
Cosmetic
Do your equipment meet GMP and other industry standards?
Yes. Our equipment fully complies with GMP, ISO, and other international industry standards and can be customized to meet specific regulatory requirements based on different markets and customers.
Ribbon mixer
Do you also have a machine for powder feeding?
Yes, we also manufacture powder feeder machine for the horizontal mixer machine. It is usually recommended the screw powder feeder type.
Automatic Servo Motor Capping Machine
Do you also supply rotary tables for bottle sorting and collecting on both sides of the high speed capping machine?
Yes, we supply related machines, not only the bottle sorting machine and bottle collection machine, but also many other filling line machines such as filling machine, labeling machine, date printer.
Automatic auger filling machine
Can I replace the screw model of the auger filler to pack different weight in one machine?
Yes, we can customize different screw models for the powder filler, and the screw models are replaceable.
Leave a message
Have any questions or concerns about our products? Please leave us a message here, and our team will get back to you promptly.
Facebook
YouTube
LinkedIn
Whatsapp: +8613434139712
Guangzhou Yuanyang Machinery