How to manufacturing double jacket mixer in Europe
- How to Manufacture Double Jacket Mixer
- Understanding the Double Jacket Mixer
- Core Components of a Double Jacket Mixer
- Step 1: Design and Engineering
- Step 2: Material Selection and Preparation
- Step 3: Cutting and Forming the Steel Plates
- Step 4: Welding and Assembly
- Step 5: Integration of Mixing Mechanism
- Step 6: Installation of Control Systems
- Step 7: Quality Inspection and Pressure Testing
- Step 8: Surface Polishing, Cleaning, and Final Assembly
- Step 9: Functional Testing
- Step 10: Packaging, Delivery, and Turnkey Support
- Why Choose YUANYANG for Your Double Jacket Mixer Needs?
- Frequently Asked Questions
How to Manufacture Double Jacket Mixer
The double jacket mixer is a staple in the industrial mixing field, especially for applications requiring precise temperature control and efficient mixing of viscous materials. As a leading China-based industrial mixer and blender factory, YUANYANG offers not just finished double jacket mixer products, but also deep expertise in the design, manufacturing, and installation of such specialized equipment. we’ll walk through the complete process of how to manufacture a double jacket mixer, spotlighting key design considerations, construction steps, and quality control measures.
Understanding the Double Jacket Mixer
Before delving into the manufacturing steps, it's important to understand what makes the double jacket mixer unique. This professional mixing equipment features an internal mixing chamber surrounded by a secondary outer jacket. The double jacket enables efficient thermal transfer—heating or cooling the contents precisely—while maintaining the integrity and homogeneity of the mixture. Frequently used in cosmetics, pharmaceuticals, food, and chemical industries, this type of mixer underscores YUANYANG’s commitment to robust, safe, and high-efficiency mixing solutions.
Core Components of a Double Jacket Mixer
Every double jacket mixer manufactured by YUANYANG or other leading factories comprises several essential components:
- Inner Tank: The main vessel where mixing occurs, constructed from high-grade stainless steel for hygiene and durability.
- Outer Jacket: A shell that envelopes the inner tank, providing space for thermal fluids to circulate and change the temperature inside the vessel.
- Mixing Mechanism: Usually high shear or emulsifying mixers installed for thorough blending of ingredients.
- Insulation Layer: Minimizes energy loss, maintaining temperature efficiency.
- Agitator and Drive System: Ensures constant, reliable mixing during operation.
- Control Panel: Advanced automation for temperature and speed settings.
- Safety Features: Pressure relief valves, sight glasses, and sanitary fittings to ensure operator safety and product quality.
Step 1: Design and Engineering
Manufacturing a double jacket mixer begins with careful design and engineering—an area where YUANYANG’s technical team excels. The process starts with gathering client requirements regarding capacity, material, mixing type, and operating conditions. Using CAD software, engineers design the tank geometry, agitation components, and jacket system to match the end-use.
Key design considerations include:
- Capacity (from small lab sizes to large-scale production)
- Level of agitation (high shear, low speed, etc.)
- Material compatibility (304/316L stainless steel commonly used)
- Heating/cooling requirements (steam, water, glycol as thermal media)
- Compliance with CE and other regulatory standards
Step 2: Material Selection and Preparation
High-quality stainless steel, such as SUS304 or SUS316L, is selected for both the inner and outer vessels, given their corrosion resistance and compliance with industry hygiene standards. All materials undergo rigorous inspection and preparation, including:
- Surface treatment (pickling and passivation)
- Thickness and grade verification to ensure tensile strength
- Traceability checks for CE certification requirements
Step 3: Cutting and Forming the Steel Plates
Based on detailed engineering drawings, stainless steel plates are precision-cut using CNC laser or plasma cutting equipment. The plates are then pre-formed, typically through rolling or pressing, to achieve the desired curvature for inner and outer shells.
In this stage, CNC accuracy ensures the perfect alignment of the inner tank, jacket, ports, and all connection flanges—critical for leak-proof and high-performance double jacket mixer.
Step 4: Welding and Assembly
The assembly of the double jacket mixer requires expert welding skills—an area where YUANYANG’s workforce is highly trained. Welding processes, such as TIG (Tungsten Inert Gas) welding, are widely used to join the vessels and the jacket sections, ensuring contamination-free operation and a smooth interior surface.
Key welding tasks include:
- Joining the inner vessel’s seams and bottoms
- Attaching the outer jacket, ensuring a uniform cavity for thermal fluid circulation
- Installing baffles for improved mixing flow
- Integrating nozzles, manways, and inlets/outlets
After welding, all seams are polished to a sanitary finish, vital for industries like cosmetics and pharmaceuticals.
Step 5: Integration of Mixing Mechanism
YUANYANG’s double jacket mixers commonly feature high shear homogenizer or vacuum emulsifying mixers at their core. The mixing mechanism is installed through reinforced openings in the tank, with the agitator shaft and motor/fan assemblies precisely aligned.
During integration:
- Dynamic shaft seals and bearings are installed for leak prevention
- Mixing blades or stators/rotors are positioned for optimal emulsification and blending
- Vacuum systems or additional agitation features are added for specific processing needs
Step 6: Installation of Control Systems
Modern double jacket mixers from YUANYANG incorporate intelligent control systems. These systems provide real-time monitoring of temperature, agitation speed, mixing duration, and vacuum pressure if applicable.
Control system installation includes:
- Connecting sensors for temperature and pressure
- Wiring control panels for easy start/stop, programmable recipes, and emergency stops
- Testing remote monitoring features or PLC integration for smart production lines
Step 7: Quality Inspection and Pressure Testing
To comply with international safety and sanitation standards, every double jacket mixer undergoes rigorous quality checks:
- Hydrostatic pressure testing of the vessel and outer jacket to guarantee leak-free operation
- Visual and dye-penetrant inspections of all weld joints
- Roughness measurements for interior surfaces (often Ra < 0.6 μm for sanitary applications)
- Operational checks on all agitators, seals, and safety valves
CE certificate documentation is prepared at this stage, as required for sales in European and other regulated markets.
Step 8: Surface Polishing, Cleaning, and Final Assembly
All surfaces are thoroughly polished to the required sanitary finish. The outer shell receives additional finish—matte, mirror, or customized as per client specifications. The tank is cleaned with industrial cleaners to remove residues, ensuring readiness for food, pharmaceutical, or cosmetic-grade production.
Mounting of final accessories, such as viewing ports, manways, pressure sensors, or filling/emptying valves takes place in this step.
Step 9: Functional Testing
Before leaving the YUANYANG factory, the double jacket mixer is fully assembled and subjected to a dry-run and wet-run test. This includes:
- Simulated mixing runs to test agitation efficiency
- Heating/cooling the vessel to check thermal uniformity and energy efficiency
- Running control system diagnostics for alarms, interlocks, and safety responses
Only after passing all Q/C steps does the equipment move toward packaging and delivery.
Step 10: Packaging, Delivery, and Turnkey Support
Packaging is tailored to protect the double jacket mixer during transport—wooden crates, vacuum packing for sensitive parts, and desiccant for moisture-sensitive areas. Clear instruction manuals and technical support documents accompany each shipment.
As part of YUANYANG’s commitment, we offer free technical training and complete turnkey installation support. Our on-site staff ensure that the double jacket mixer is installed, commissioned, and integrated seamlessly with your existing production line equipment, such as storage tanks, filling machines, and water treatment systems.
Why Choose YUANYANG for Your Double Jacket Mixer Needs?
With over 15 years of experience, YUANYANG stands out as a reliable, innovative, and technically advanced manufacturer of double jacket mixers and related industrial solutions. Our products carry multiple CE certifications, ensuring compliance with the strictest international health and safety standards. Beyond manufacturing, our one-stop support—covering technical training, installation, and after-sales service—guarantees long-term equipment performance and minimized downtime for your production line.
Frequently Asked Questions
What is a double jacket mixer?
A double jacket mixer is industrial mixing equipment designed with two layers: an inner tank for mixing and an outer jacket for circulating heating/cooling fluids. This design ensures precise temperature control during the mixing of sensitive or viscous products.
Why is stainless steel preferred for double jacket mixers?
Stainless steel, particularly grades 304 and 316L, offers high corrosion resistance, easy cleaning, and compliance with hygiene standards, making it ideal for food, cosmetic, and pharmaceutical applications.
How does a double jacket mixer control temperature?
Thermal media (such as steam, water, or oil) circulated within the outer jacket enables rapid heating or cooling of the mix, controlled automatically via integrated sensors and PLC systems.
Is the double jacket mixer suitable for high-viscosity products?
Yes, especially when equipped with high shear or vacuum homogenizer systems. The robust agitators and thermal control ensure efficient mixing of viscous materials like creams, gels, or pastes.
Does YUANYANG provide turnkey services for industrial mixers?
Absolutely. YUANYANG supports customers with free technical training, on-site installation, commissioning, and after-sales support for complete turnkey production lines.
What certifications do YUANYANG double jacket mixers have?
Our mixers bear CE certificates, certifying compliance with European safety and health regulations, an essential mark for exporting and operating within the EU.
Can the mixer be customized for my process?
Yes, YUANYANG specializes in tailored solutions. We can adjust tank size, agitation type, control systems, and other features according to your specific process requirements.
How do I get technical help or training?
YUANYANG provides comprehensive user manuals, free technical training at our factory or your site, and 24/7 customer support for troubleshooting and optimal equipment use.
Contact YUANYANG today for more details on our double jacket mixer manufacturing expertise, and let us help you upgrade your production capabilities!
How to Choose Right continuous powder mixer manufacturer and supplier in America?
How to start a water bottle cap sealing machine business in UK
OEM/ODM vacuum mixer homogenizer Manufacturers and Suppliers
Top 10 china vacuum emulsifying mixer Manufacturers and Supplier Brands in Africa
Vacuum Homogneizer
Is there any safety devices for the homogenizer tank?
Yes,there are safety valves for jacket pressure and vacuum pressure. When the pressure reaches the designed margin point, the safety valves can protect the machine by releasing the gas.
And circuit protection device is equipped in the control box, when the power supply of the factory is beyond the designed voltage of the machine, or occurs short circuit, it will operate self-protection system.
Liquid Soap Making Machine
Do you have PLC control panel for the soap mixing tank?
Yes, the control panel can be button control or with PLC touch screen. The standard is with button control, clients choose based on budget. we will customize upon requirements.
Homogenizer Mixing Tank with Circulation System
Do you have a water pump with flow meter installed for the shampoo mixer machine?
Yes, water pump with flow meter can be added upon requirements.
Hydraulic Lift Vacuum Mixer
What’s the feature of water tank and oil tank?
The water tank and oil tank are for pre-treatment for better mixing efficient when sucked into main emulsifying tank. The two tanks are often equipped with bottom dispersing plate or top mixing and double jackets for heating and insulation.
What’s the maximum height that the lid can lift up to? And how high it is when cover closed?
The dimension is different for different capacity. For example, the 500L height is 2.48m when cover closed, the height is 3.6m when cover lift up.
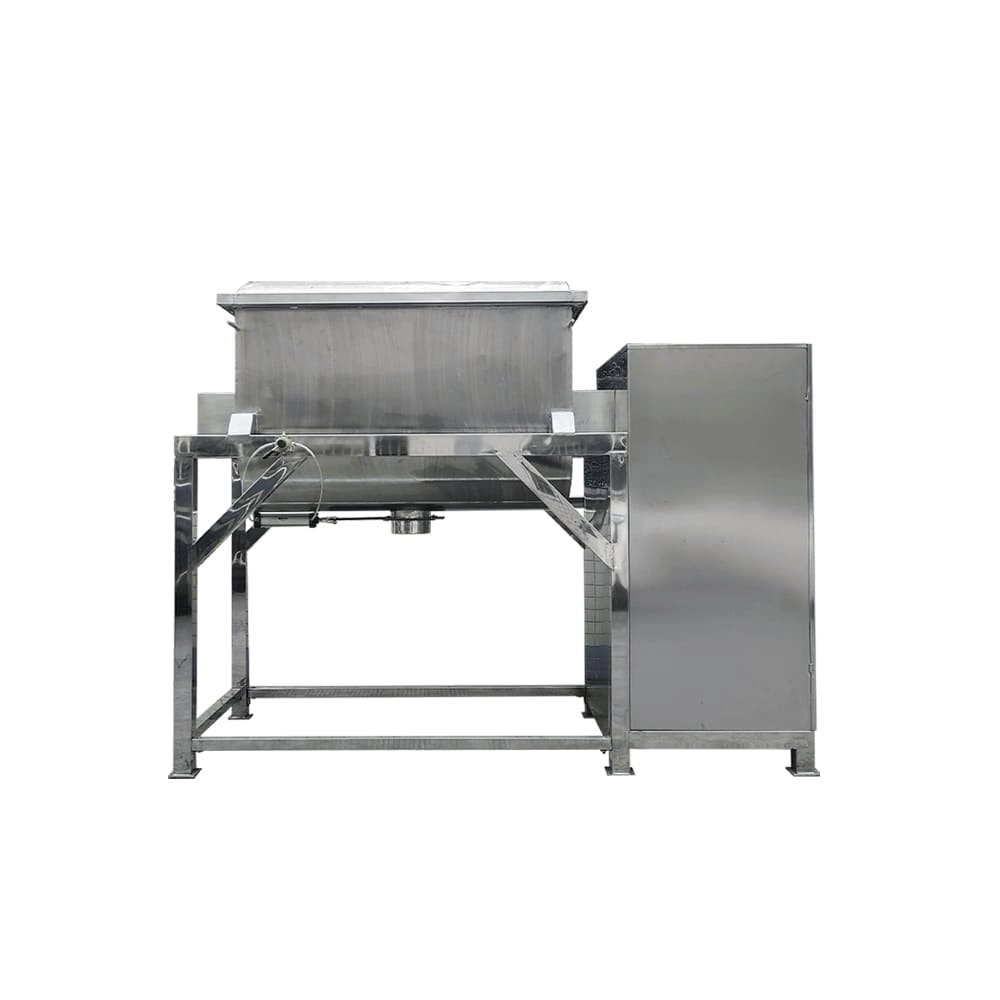
Detergent powder mixer for Sale
Yuanyang detergent powder mixer is also called a ribbon mixer, which is an industrial powder mixer machine applied to mix different kinds of raw powder together, especially used to produce detergent powder.
Feature:
-
⦁ Button control panel;
⦁ Food-grade materials;
⦁ U-shaped tank.
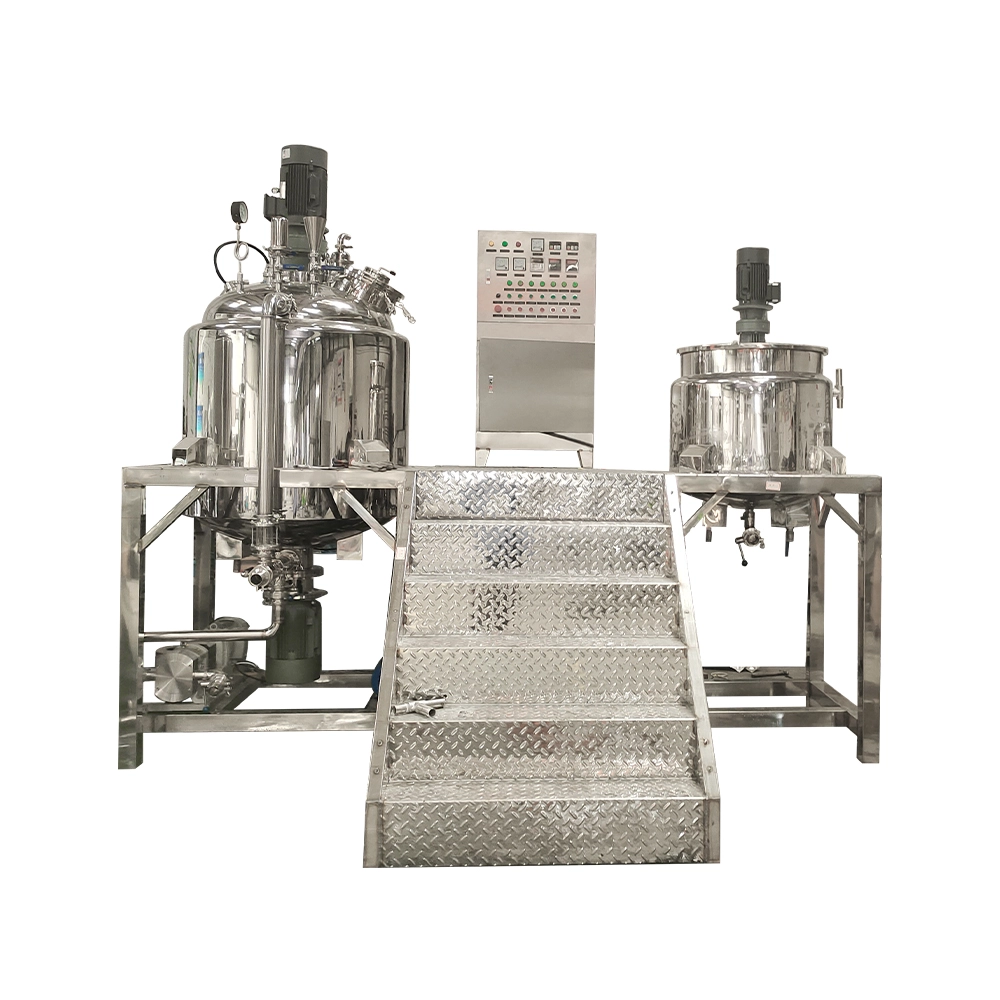
Vacuum Cosmetic Mixer with Water and Oil Tank for Sale
Yuanyang vacuum cosmetic mixer is a combined mixing equipment with a main vacuum homogenizer tank, water tank, and oil tank, which is an integrated equipment with a mixing, dispersing, homogenizing, emulsifying, and powder absorption system that is widely used in cosmetics, food, pharmaceutical, and chemical fields.
Features:
⦁ With a fixed lid, vacuum system, and electric control system.
⦁ Suitable for products of 10,000~50,000 cps viscosity.
⦁ Perfect particle size of 2 microns and evenly distributed.
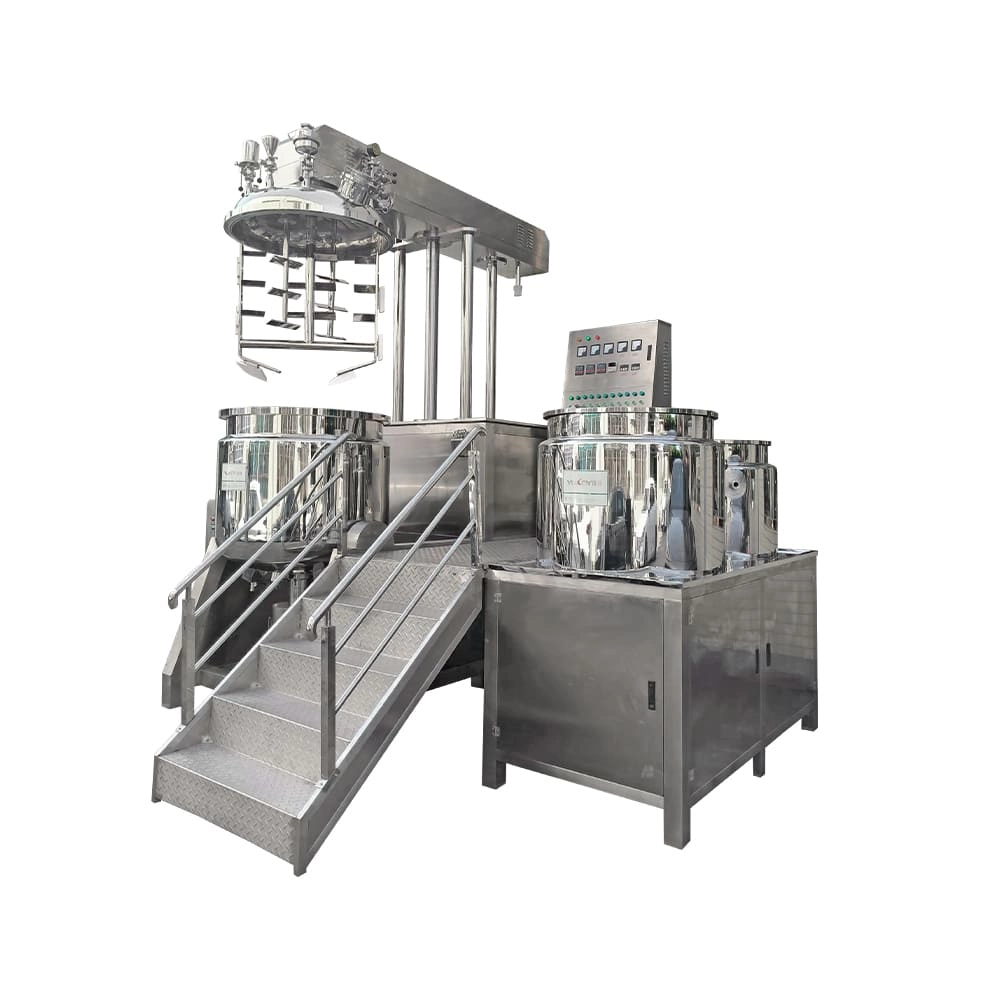
Hydraulic Lift Vacuum Mixer for Sale
Yuanyang hydraulic lift vacuum mixer is a kind of cosmetic mixing equipment, which is the core part of the cosmetic production line.
The hydraulic type is the most popular cosmetic production equipment for making cream, skin-care products, ointment, paste, emulsions, and so on.
Features:
⦁ Composed of a main emulsifying pot, a water pot, and an oil pot.
⦁ With a hydraulic lifting system, vacuum system, and electric control system.
⦁ Suitable for products of 10,000~50,000 cps viscosity.
⦁ Perfect particle size of 2 microns and evenly distributed.
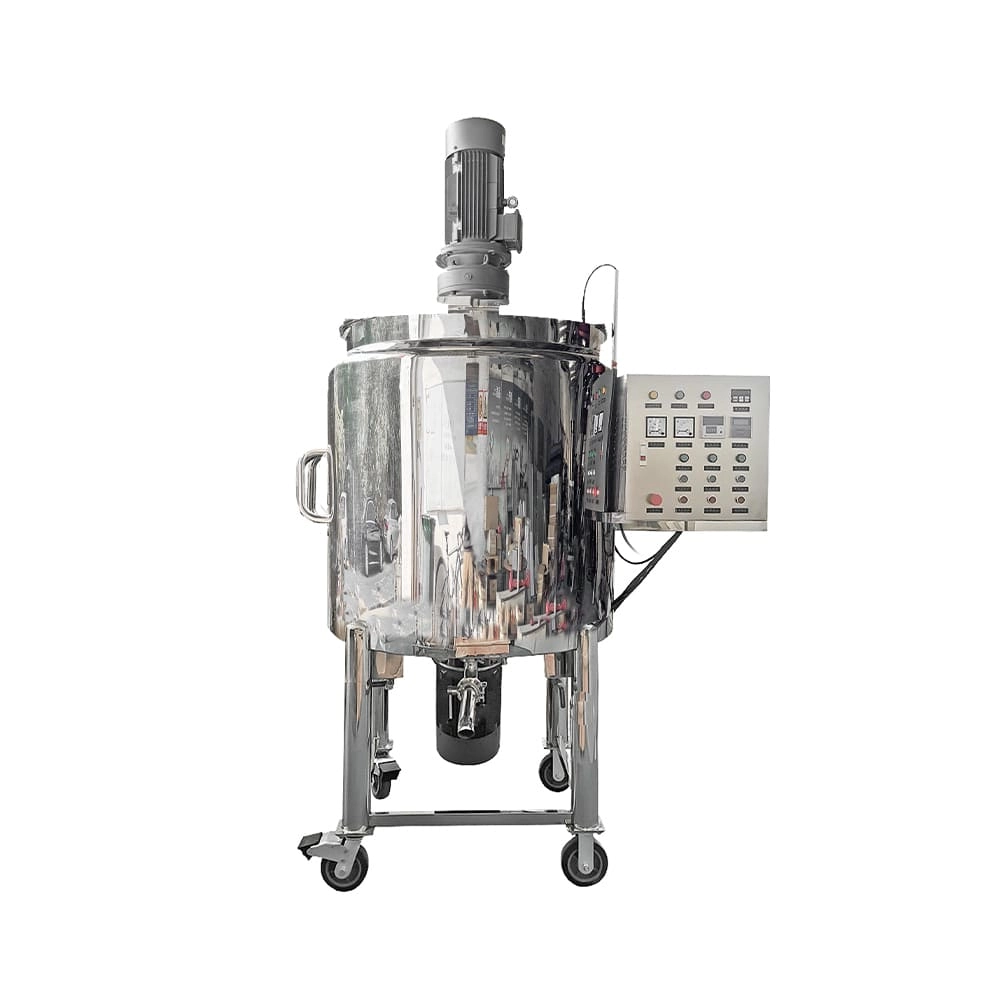
Homogenizing Mixer for Sale
Yuanyang homogenizing mixer is a liquid mixing tank with a high-shear homogenizer. The homogeneous mixing machine is the core part for the liquid soap production line for shampoo, body wash, laundry detergent, dish soap, hand sanitizer, and other thick liquids.
Features:
⦁ Flat top half-open lid, electric control system.
⦁ Suitable for various liquid cleaning products and sauces.
⦁ PTFE wall scrapers stirring at top, high shear homogenizer at bottom.
Facebook
YouTube
LinkedIn
Whatsapp: +8613434139712
Guangzhou Yuanyang Machinery