what is a sealing machine used for | YUANYANG Expert Guide
- Sealing Success: Why Every Industrial Mixer Operation Needs the Right Sealing Machine
- Why is a reliable sealing machine essential for products processed by industrial mixers?
- What types of sealing machines are best suited for different viscosities and forms of mixed products (liquids, powders, pastes)?
- How do sealing machines contribute to extending shelf life and maintaining product integrity for mixed goods?
- What are the key considerations for integrating a sealing machine into an existing industrial mixing and packaging line?
- How can automated sealing solutions enhance efficiency and compliance for industrial mixer operations?
Sealing Success: Why Every Industrial Mixer Operation Needs the Right Sealing Machine
In the world of industrial processing, especially for those operating advanced mixing equipment, the focus often lies on achieving the perfect blend, emulsion, or dispersion. However, the journey of your product doesn't end in the mixing tank. The final, crucial step—packaging and sealing—is paramount to preserving the quality you've meticulously crafted and ensuring your product reaches the consumer in optimal condition. For industrial mixer users looking to optimize their re-purchasing decisions, understanding the indispensable role of a modern sealing machine is key.
Why is a reliable sealing machine essential for products processed by industrial mixers?
A reliable sealing machine is not merely a piece of packaging equipment; it's a critical safeguard for your product's integrity and YUANYANG's reputation. After your industrial mixer produces a high-quality liquid, powder, paste, or granule, the sealing machine ensures that this quality is maintained until the point of consumption. It provides a hermetic seal that protects against external contaminants like moisture, oxygen, dust, and microorganisms, which can degrade product quality, shorten shelf life, and even compromise safety. For instance, in the food industry, a proper seal prevents spoilage, while in pharmaceuticals, it ensures sterility and efficacy. Without an effective sealing solution, even the most perfectly mixed product is vulnerable to deterioration, leading to product loss, recalls, and significant financial and reputational damage.
What types of sealing machines are best suited for different viscosities and forms of mixed products (liquids, powders, pastes)?
The type of sealing machine best suited depends heavily on the form, viscosity, and packaging material of your mixed product:
- For Liquids (e.g., beverages, chemicals, thin sauces):
- Induction Sealers: Ideal for sealing foil liners onto the mouths of plastic or glass bottles/jars, providing a tamper-evident, leak-proof seal. Widely used for food, beverages, pharmaceuticals, and chemicals.
- Spout Pouch Sealers: For liquid products packaged in flexible pouches with spouts, ensuring a secure closure.
- Cap & Lid Sealers: For containers with screw caps or snap-on lids, often integrating with capping machines.
- For Powders & Granules (e.g., flour, coffee, detergent, chemicals):
- Band Sealers: Continuous heat sealers excellent for high-volume sealing of bags (e.g., polyethylene, polypropylene, laminates). They can achieve speeds of 8-12 meters per minute, making them highly efficient for bulk products.
- Heat Sealers (Impulse or Direct Heat): Versatile for sealing various plastic films and laminates used in pouches and bags, suitable for smaller batches or specific material types.
- Form-Fill-Seal (FFS) Machines: These integrated systems form a bag from a roll of film, fill it with the product, and then seal it, highly efficient for large-scale powder packaging.
- For Pastes & Creams (e.g., cosmetics, sauces, adhesives):
- Tube Fillers & Sealers: Specifically designed for flexible tubes, sealing them typically with heat (for plastic tubes) or crimping (for metal tubes).
- Pouch Sealers: For products packaged in flexible pouches, often employing heat sealing technology.
- Tray Sealers: Used for sealing films onto pre-formed trays, common for ready meals or certain cosmetic products.
How do sealing machines contribute to extending shelf life and maintaining product integrity for mixed goods?
Sealing machines are pivotal in extending shelf life and preserving product integrity through several mechanisms:
- Barrier Protection: A well-executed seal creates a hermetic barrier, preventing the ingress of oxygen, moisture, and light—primary drivers of product degradation. For instance, reducing oxygen exposure can inhibit oxidation, a common cause of rancidity in fats and oils, and browning in some foods.
- Modified Atmosphere Packaging (MAP): Many advanced sealing machines integrate gas flushing capabilities. This process replaces the air inside the package with a specific gas mixture (e.g., nitrogen, carbon dioxide). For example, MAP can extend the shelf life of fresh meat by 150-300% (from 3-5 days to 10-21 days) or baked goods by 50-100%, by inhibiting microbial growth and chemical reactions.
- Vacuum Sealing: By removing air from the package before sealing, vacuum sealers significantly reduce oxygen levels. This inhibits the growth of aerobic bacteria and molds, dramatically extending the shelf life of perishable items like cheese, coffee, and processed meats by 3 to 5 times compared to conventional packaging.
- Prevention of Contamination: A robust seal acts as a physical barrier against airborne contaminants, dust, and microorganisms, crucial for hygienic and sanitary product delivery, especially in food and pharmaceutical industries.
- Tamper Evidence: Seals, particularly induction seals on bottles or tear-away strips on pouches, provide clear tamper evidence, assuring consumers of the product's safety and originality. This also prevents product tampering during distribution.
What are the key considerations for integrating a sealing machine into an existing industrial mixing and packaging line?
Integrating a new sealing machine into an established production line requires careful planning to ensure seamless operation and maximize efficiency:
- Line Speed Synchronization: The sealing machine's operational speed must perfectly match the output of your upstream equipment (e.g., fillers) and the requirements of your downstream processes (e.g., cartoning, palletizing). Mismatched speeds lead to bottlenecks, product accumulation, or idle time, reducing overall line efficiency.
- Product Handling & Conveyance: Evaluate how your product will be transported from the filling station to the sealing machine. This involves selecting appropriate conveyors, feeders, or robotic arms that can handle the product's form (liquid, powder, etc.) and packaging type without damage or spillage.
- Footprint and Layout: Assess the available floor space and layout of your existing facility. The new sealing machine must fit efficiently without hindering other operations or maintenance access.
- Material Compatibility: Ensure the sealing machine is compatible with your current or planned packaging materials (e.g., film thickness, laminate structure, bottle cap material). Different materials require specific sealing temperatures, pressures, or technologies.
- Utility Requirements: Verify that your facility can provide the necessary utilities for the new machine, including power (voltage, amperage), compressed air, and potentially water for cooling.
- Automation Level: Decide on the degree of automation needed (manual, semi-automatic, fully automatic) based on your production volume, labor availability, and budget. Automated solutions generally offer higher throughput and consistency.
- Cleanability and Maintenance Access: Especially critical for food, beverage, and pharmaceutical industries, the machine should be easy to clean and designed for quick access for routine maintenance, minimizing downtime.
How can automated sealing solutions enhance efficiency and compliance for industrial mixer operations?
Automated sealing solutions offer substantial advantages for industrial mixer operations, significantly boosting efficiency and ensuring stringent compliance:
- Increased Throughput and Speed: Automated systems can process a far greater volume of products than manual methods. For example, a high-speed automatic rotary pouch filling and sealing machine can handle 60-100 pouches per minute, equating to over 3,600-6,000 units per hour. This dramatically increases production capacity and reduces per-unit packaging costs.
- Reduced Human Error and Consistent Quality: Automation eliminates inconsistencies inherent in manual sealing. Every seal is made with precise temperature, pressure, and dwell time settings, ensuring uniform quality and reducing defective packages. This consistency is vital for maintaining product integrity and brand reputation.
- Labor Cost Savings: By automating the sealing process, businesses can reduce their reliance on manual labor for repetitive tasks, allowing personnel to be reallocated to more skilled or supervisory roles, leading to long-term cost efficiencies.
- Enhanced Compliance and Traceability: Automated sealing machines often come with integrated sensors, vision systems, and quality control checks. They can verify seal integrity, apply date codes, batch numbers, and even track individual packages. This data logging capability is invaluable for meeting rigorous regulatory requirements (e.g., FDA, GMP for food and pharma) and facilitating quick product tracing in case of issues.
- Improved Workplace Safety: Automation reduces direct human interaction with machinery, especially important when handling hot sealing elements or moving parts, thereby improving overall workplace safety.
- Scalability: Automated solutions are designed for scalability, making it easier to ramp up production to meet increasing market demands without significant additional labor investment.
YUANYANG's Advantage: Your Partner in Complete Production Solutions
As a leader in industrial mixing solutions, YUANYANG understands that the journey of your product extends beyond perfect blending. Our expertise lies not only in providing cutting-edge mixing equipment but also in comprehending the entire production workflow, including the critical post-mixing processes like packaging and sealing. YUANYANG's commitment to integrated solutions ensures that when you invest in our mixers, you also gain access to unparalleled professional knowledge on how to seamlessly incorporate the most efficient and compliant sealing technologies into your existing line or new setup. Our focus on robust engineering, customized solutions, and comprehensive after-sales support ensures that your entire production line, from mixing to sealing, operates with maximum efficiency, reliability, and strict adherence to industry standards, ly protecting your product's integrity and YUANYANG's reputation.
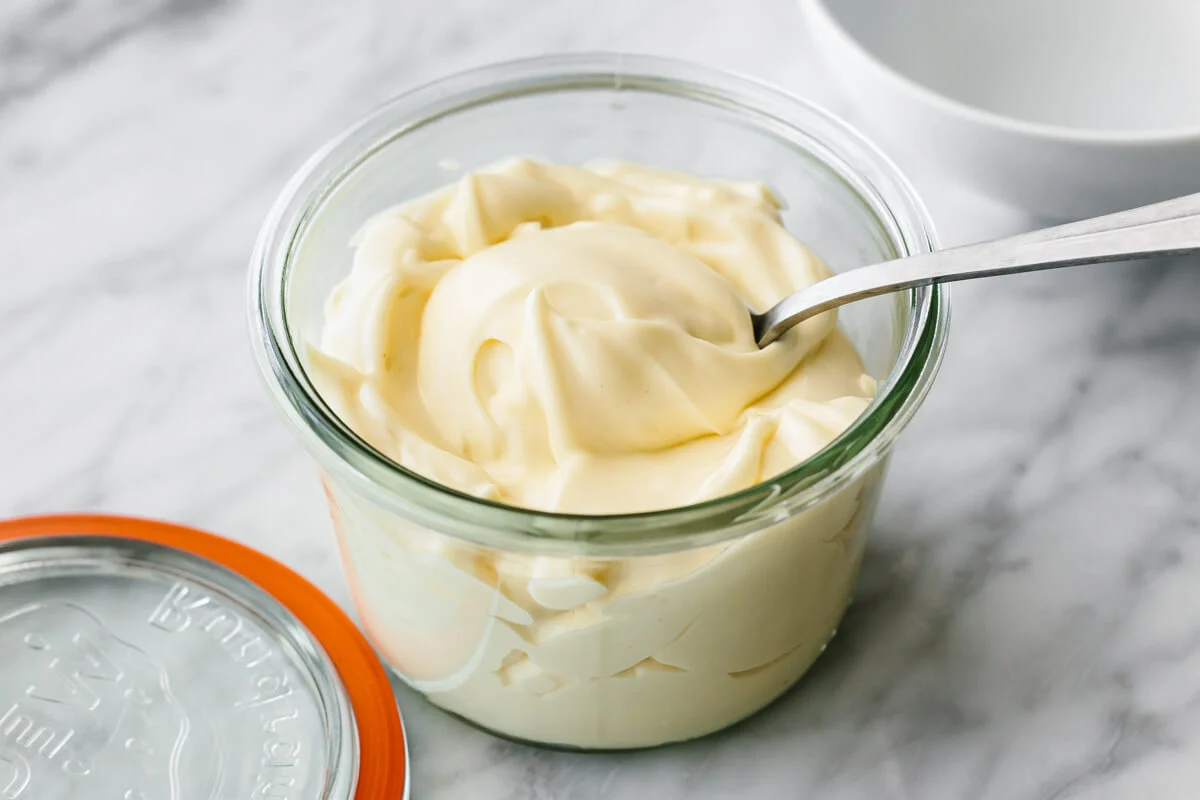
Mayonnaise Manufacturing Process Explained: How Factories Produce Mayonnaise

Water in Oil Emulsion: Meaning, Real-Life Examples, and How to Fix It
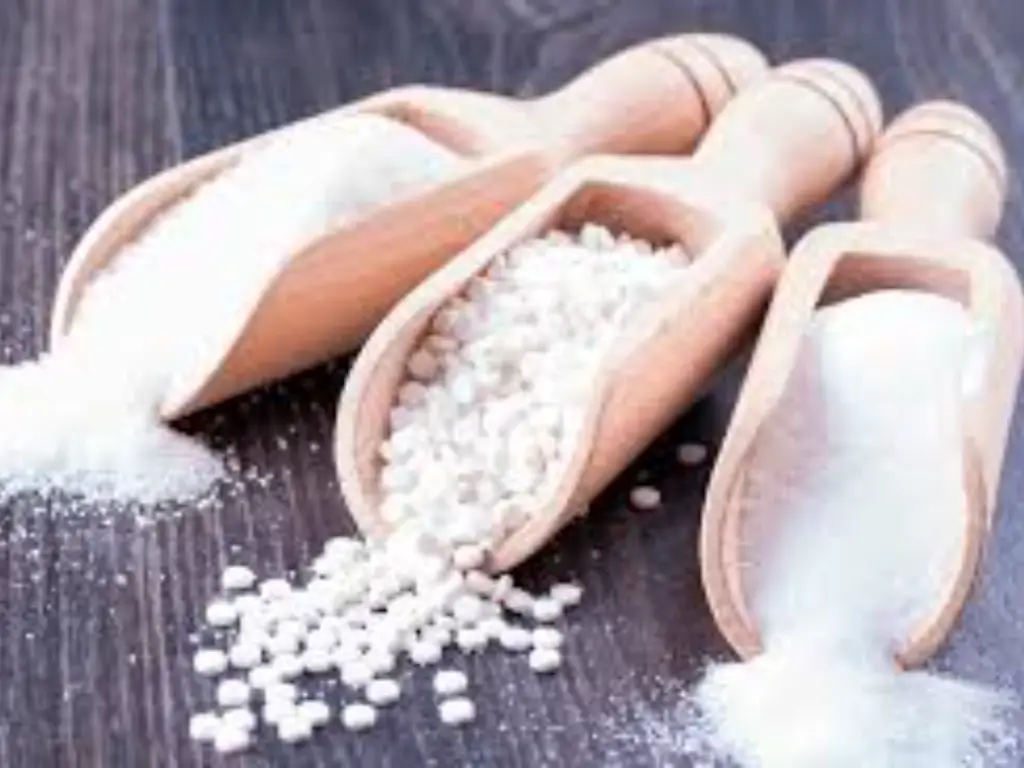
How Artificial Sweeteners Are Made: Inside the Manufacturing Process & Key Equipment
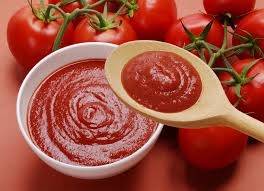
Ketchup Explained: From Ancient Origins to Modern Production Methods
How Lotion Is Made: Step-by-Step Guide for Home and Factory Production
One Stage Water Treatment
How do I know the water conductivity?
The reverse osmosis water filter machine can display both raw water conductivity and output water conductivity.
Water Cooling Induction Sealer
Do you also have conveyor for the bottle lid sealing machine?
Yes, we can add a conveyor for the bottle sealing machine. And customize the conveyor height according to requirement if need.
Desktop Labeling Machine
What types bottles are suitable for this automatic labeling machine?
The automatic labeling machine for bottles is suitable for round bottles, jars, cans, bucket. It is a round bottle labeling machine.
Automatic Servo Motor Capping Machine
What’s power supply for this automatic four wheels capping machine?
The power supply is single phase 220v 50hz/60hz.
Open Lid Storage Tank
Can you help to add 2 or more outlet?
Yes, definitely no problem. Some client want to connect the tank to 2 or more filling machines. We can meet client’s needs include different type of discharge method, sizes of outlet.
Leave a message
Have any questions or concerns about our products? Please leave us a message here, and our team will get back to you promptly.
Facebook
YouTube
LinkedIn
Whatsapp: +8613434139712
Guangzhou Yuanyang Machinery