A Complete Guide to the Liquid Soap Production Line: Equipment, Process, and Key Considerations
Learn about the essential equipment, production process, and best practices for optimizing your liquid soap production line. Boost your efficiency today!
- Introduction to the Liquid Soap Production Line
- What is a Liquid Soap Production Line?
- Key Components of a Liquid Soap Production Line
- 1. Raw Material Handling and Preparation
- 2. Mixing and Blending Equipment
- 3. Heating and Cooling Systems
- 4. Transfer Pumps for Consistent Flow
- The Liquid Soap Filling and Packaging Process
- 1. Filling Machines
- 2. Capping Machines
- 3. Labeling Machines
- 4. Packaging Machines
- Quality Control in Liquid Soap Production
- Factors to Consider When Setting Up a Liquid Soap Production Line
- 1. Scale of Production
- 2. Production Efficiency
- 3. Cost of Equipment and Maintenance
- 4. Compliance with Regulations
- Conclusion
- FAQs
Introduction to the Liquid Soap Production Line
The liquid soap production line is an essential part of modern manufacturing processes in the personal care industry. With the growing demand for liquid soap products globally, manufacturers are increasingly investing in advanced production lines to streamline operations, enhance product quality, and meet market demand efficiently. This comprehensive guide will walk you through the necessary components of a liquid soap production line, from mixing and formulation to packaging and quality control.
What is a Liquid Soap Production Line?
A liquid soap production line refers to the automated system used to manufacture liquid soap products on a large scale. It consists of various machines and equipment that work in tandem to mix ingredients, produce the soap mixture, and package it for retail or commercial use. The production process involves several stages, including formulation, mixing, heating, cooling, filling, capping, labeling, and packaging.
Key Components of a Liquid Soap Production Line
1. Raw Material Handling and Preparation
The initial phase of liquid soap production begins with raw material preparation. Common ingredients in liquid soap formulations include surfactants (such as sodium lauryl sulfate), water, fragrances, and preservatives. These raw materials must be carefully handled, stored, and weighed before being added to the production system.
Storage tanks and hopper feeders are typically used to manage raw materials. They should be built from corrosion-resistant materials, such as stainless steel, to ensure product purity.
2. Mixing and Blending Equipment
Once the raw materials are prepared, they are transferred to mixing and blending tanks. These tanks are equipped with high-shear mixers to ensure that all ingredients blend into a smooth, uniform soap mixture.
The key to high-quality liquid soap production lies in the consistency of the mixture, and high-shear mixing technology helps break down the raw materials into smaller particles, ensuring they combine seamlessly. This also prevents the formation of air bubbles that could affect the soap’s texture.
3. Heating and Cooling Systems
Certain ingredients in liquid soap require heating to dissolve or activate. In these cases, the production line is equipped with heating systems such as steam jackets or electric heating elements. The temperature is carefully monitored to ensure that the soap mixture does not overheat, which could degrade the product quality.
After the soap mixture has been heated, it is typically cooled in a controlled cooling system to bring it to the optimal temperature for packaging.
4. Transfer Pumps for Consistent Flow
Transfer pumps play a crucial role in maintaining a steady flow of materials from one stage of the production line to the next. Whether you’re moving raw materials to the mixing tank or transferring the finished soap to filling stations, these pumps ensure that the liquid soap flows smoothly and without interruption.
Centrifugal and diaphragm pumps are the most commonly used in liquid soap production lines. These pumps need to be carefully selected based on the viscosity of the soap and the desired flow rate.
The Liquid Soap Filling and Packaging Process
1. Filling Machines
Once the liquid soap has been thoroughly mixed and cooled, it is ready for filling into bottles, pouches, or other containers. The filling machine automatically dispenses the right amount of liquid soap into containers, ensuring uniformity and minimizing waste.
There are several types of filling systems available, including volumetric fillers and weight-based fillers. Volumetric fillers are often used in high-volume production lines, while weight-based fillers provide more accuracy in measuring liquid soap.
2. Capping Machines
After the containers are filled, they move to the capping station, where capping machines securely seal the bottles or containers. Depending on the type of cap (e.g., flip-top, pump, or screw cap), the machine will apply the cap and ensure that it is tightly sealed to prevent leakage during transport and storage.
Modern capping machines are equipped with sensors that automatically adjust the torque, ensuring that caps are neither too tight nor too loose.
3. Labeling Machines
Labeling is a vital step in the liquid soap production line, as it provides essential product information such as ingredients, usage instructions, and branding. Labeling machines are used to apply adhesive labels, shrink sleeves, or stretch sleeves to the containers.
Some advanced labeling systems are capable of applying multiple labels, such as front, back, and side labels, in a single pass, reducing production time and increasing efficiency.
4. Packaging Machines
After the soap has been filled, capped, and labeled, it moves on to the packaging stage. Packaging machines are used to place the filled and labeled containers into cartons, shrink wraps, or other secondary packaging. These machines help optimize the storage and transportation of the finished product, ensuring that it remains intact during shipping.
Packaging lines may also include carton sealing machines, which ensure that the product is securely packaged for retail distribution.
Quality Control in Liquid Soap Production
Maintaining consistent quality throughout the production line is essential for manufacturers. To achieve this, quality control (QC) checks are implemented at various stages of the production process.
Viscosity Testing: The soap mixture's viscosity is tested to ensure it matches the desired thickness for the end product.
pH Level Testing: Liquid soap’s pH is an important quality parameter, as it ensures the product is safe for use and is not too harsh on the skin.
Microbial Testing: Samples are taken from the production line for microbial analysis to ensure the soap is free from harmful bacteria or contaminants.
Factors to Consider When Setting Up a Liquid Soap Production Line
1. Scale of Production
The size and scope of your production line will depend on the scale of your operations. For smaller businesses, semi-automatic lines may be sufficient, while larger manufacturers may require fully automated production lines to handle high volumes.
2. Production Efficiency
Efficiency is key to maintaining profitability. A well-designed production line minimizes downtime and optimizes production rates while maintaining consistent product quality.
3. Cost of Equipment and Maintenance
Investing in high-quality equipment is crucial for maintaining a reliable production line. However, you must also consider the long-term maintenance costs, as regular upkeep is essential to ensure the smooth running of the system.
4. Compliance with Regulations
Manufacturers must ensure that their production lines comply with local and international regulations related to cosmetics and personal care products. This includes adhering to safety standards, labeling laws, and environmental regulations.
Conclusion
The liquid soap production line is a complex, multi-stage process that requires careful planning, efficient machinery, and attention to detail to ensure a high-quality final product. By understanding the essential components of the production line, such as mixing, heating, filling, and packaging, manufacturers can optimize their operations for both quality and efficiency. Additionally, implementing rigorous quality control measures throughout the production process will help maintain consistency and meet consumer expectations.
As the demand for liquid soap continues to rise, investing in an efficient and automated production line will be crucial for staying competitive in the market.
FAQs
1. What are the main ingredients used in liquid soap production?
The primary ingredients in liquid soap are surfactants, water, fragrances, and preservatives. Surfactants like sodium lauryl sulfate help create the soap’s cleansing properties, while preservatives ensure the product’s shelf life.
2. How do I ensure my liquid soap production line is efficient?
To ensure efficiency, optimize machine settings, maintain regular equipment upkeep, and streamline your workflow. Incorporating automated systems can significantly reduce manual labor and improve output.
3. What are the different types of filling machines used in liquid soap production?
Common filling machines include volumetric fillers, weight-based fillers, and piston fillers. Volumetric fillers are popular for high-volume production, while weight-based fillers are used for precise measurements.
4. What safety standards should be followed in liquid soap production?
Safety standards vary by region but typically include guidelines for handling chemicals, hygiene practices, and machinery safety. Ensure compliance with local regulations, such as GMP (Good Manufacturing Practices) and ISO certifications.
5. How do I choose the right packaging machine for liquid soap?
Consider the type of container you plan to use (e.g., bottles, pouches), the speed of production, and the required level of automation. Choose machines that are compatible with your production volume and can handle your specific packaging needs.
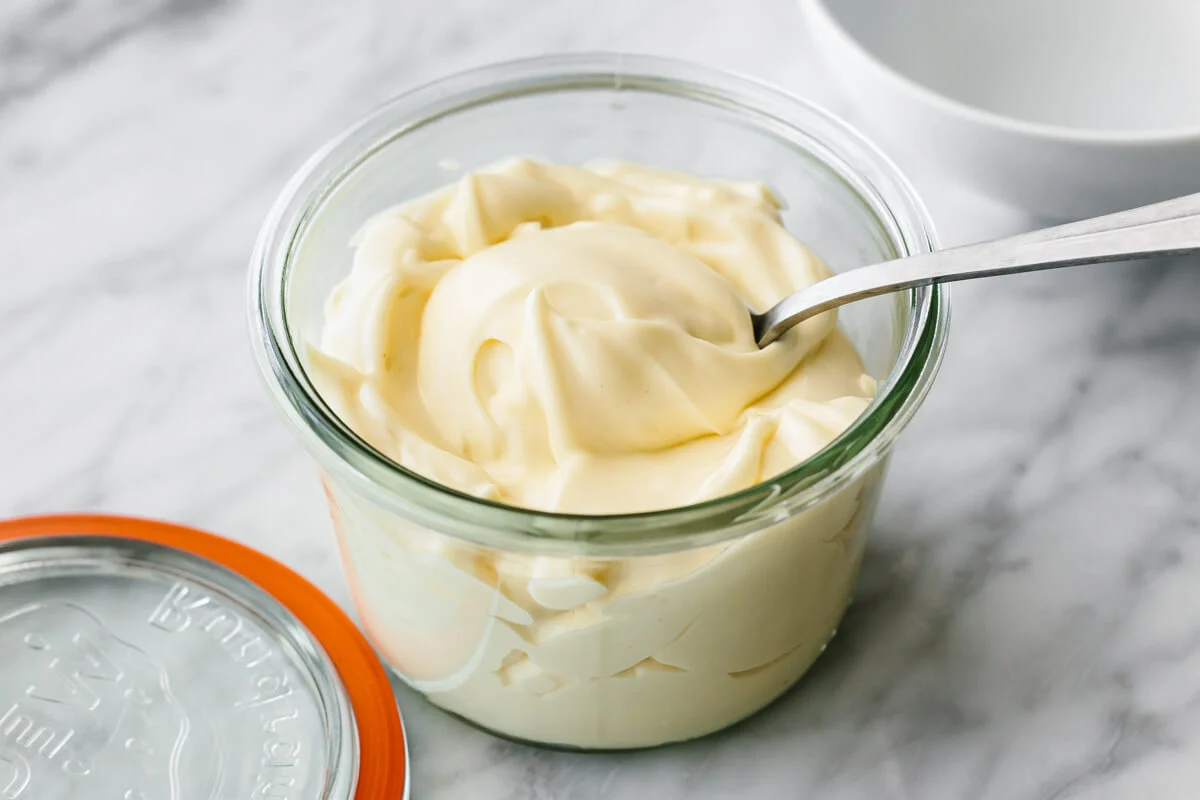
Mayonnaise Manufacturing Process Explained: How Factories Produce Mayonnaise

Water in Oil Emulsion: Meaning, Real-Life Examples, and How to Fix It
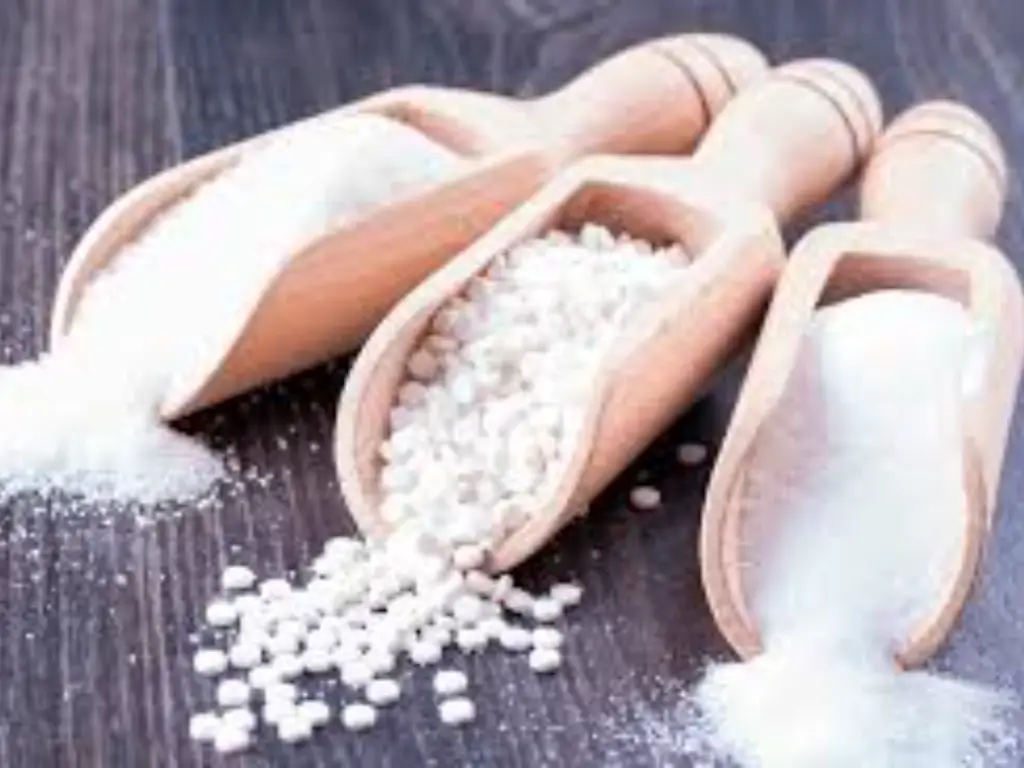
How Artificial Sweeteners Are Made: Inside the Manufacturing Process & Key Equipment
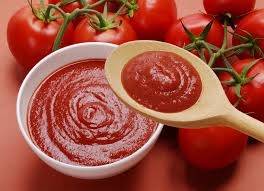
Ketchup Explained: From Ancient Origins to Modern Production Methods
How Lotion Is Made: Step-by-Step Guide for Home and Factory Production
Aluminum Foil Sealing Machine
Is the plastic bottle sealing machine also suitable for metal cap?
No, It is not suitable for metal cap, because the heat can’t go through the metal, the sealing won’t be achieved.
Single Layer Agitator Tank
What capacity do you provide for the mixing tank with agitator?
The steel tank with agitator has different capacity from 50L to 5000L.
Vacuum Homogneizer
What capacity do you recommend for a new factory?
Vacuum homogenizer is a little expensive, and the dimension is big,compared with non-vacuum type. As a start, small capacity from 50-500L is recommended if client has limit budget. Later bigger capacity 500-5000L is considered to expand business.
For easy shipment,50-1000L is often recommended for vacuum type.
Liquid Mixing Tank
Can you explain the heating principle? How does it achieve heating purpose?
The jacket tank transmits heat to the liquid through the principle of heat conduction, and the heat medium in circulation between the inner wall and the jacket is responsible for conducting heat and transferring the temperature of the jacket heat medium to the liquid product.
Detergent powder mixer
Do you also provide formula of detergent powder if I purchase the detergent powder mixer machine?
Yes, Yuany offers technical support to help optimize formulas and adjust production processes, ensuring product stability and performance.
Leave a message
Have any questions or concerns about our products? Please leave us a message here, and our team will get back to you promptly.
Facebook
YouTube
LinkedIn
Whatsapp: +8613434139712
Guangzhou Yuanyang Machinery