How to manufacturing bottle filling capping machine in Europe
- How to Manufacture a Bottle Filling and Capping Machine: A Comprehensive Guide
- 1. Design and Engineering: The Blueprint for Success
- 2. Component Selection: Choosing the Right Parts
- 3. Assembly and Integration: Bringing It All Together
- 4. Testing and Quality Control: Ensuring Performance
- 5. Final Adjustments and Deployment
- YUANYANG: Your Partner in Complete Production Line Solutions
- Frequently Asked Questions (FAQs)
- Q: What are the key factors to consider when choosing a filling mechanism for my bottle filling capping machine?
- Q: How can I ensure the safety of operators during the operation of my bottle filling capping machine?
- Q: What type of materials are best suited for a bottle filling capping machine?
- Q: What are the advantages of a modular design for a bottle filling capping machine?
- Q: How can I optimize the performance of my bottle filling capping machine?
- Q: Where can I find reliable suppliers for components for my bottle filling capping machine?
- Q: What support does YUANYANG provide after the sale of equipment?
How to Manufacture a Bottle Filling and Capping Machine: A Comprehensive Guide
Choosing to manufacture your own bottle filling and capping machine is a significant undertaking, requiring careful planning and execution. This detailed guide will walk you through the essential steps, providing insights into the process from initial design to final testing. While YUANYANG specializes in industrial mixers and provides complete production lines, understanding the intricacies of bottle filling and capping machine manufacturing is vital for integrating such equipment seamlessly into your operation.
1. Design and Engineering: The Blueprint for Success
The initial phase focuses on designing a bottle filling and capping machine tailored to your specific needs. This necessitates a thorough understanding of your production capacity, bottle types, and desired output. Key design considerations include:
* Bottle Handling System: This system must efficiently handle a range of bottle sizes and shapes without damage. Consider using conveyors, robotic arms, or a combination thereof. The choice influences the overall design and cost of your bottle filling capping machine.
* Filling Mechanism: Several filling methods exist, including gravity filling, volumetric filling, and pressure filling. The optimal choice depends on the viscosity and characteristics of your product. A poorly chosen filling mechanism directly impacts your machine’s efficiency and accuracy. Each method presents different challenges and advantages. Choosing correctly is paramount to a well-functioning bottle filling and capping machine.
* Capping Mechanism: Similar to the filling mechanism, various capping methods exist, such as screw capping, press-on capping, and crimp capping. The selection must align perfectly with your bottle design and desired sealing integrity.
* Control System: A robust control system is essential for precise operation and monitoring. Programmable Logic Controllers (PLCs) are often used to manage the entire process, ensuring consistent filling and capping. Your control system should allow for easy monitoring and adjustments to ensure optimum performance for your bottle filling capping machine.
* Safety Features: Incorporate comprehensive safety features to protect operators from potential hazards. This includes emergency stops, safety guards, and interlocks. A properly designed and implemented safety system is not just a matter of compliance but also of ensuring the safety of your workers and protecting your investment in your bottle filling capping machine.
2. Component Selection: Choosing the Right Parts
Once the design is finalized, you must carefully select the components for your bottle filling and capping machine. The quality of components directly impacts the machine's reliability and lifespan. Key considerations include:
* Material Selection: Choose materials resistant to corrosion and wear, particularly for parts in contact with your product. Stainless steel is a common choice for its durability and hygiene. The correct choice of material prevents contamination and ensures the longevity of your bottle filling capping machine.
* Motor Selection: The motors must provide sufficient torque and speed for reliable operation. Consider factors like power requirements, efficiency, and maintenance requirements. The correct motor selection is essential for optimal performance in your bottle filling capping machine.
* Sensors and Actuators: Sensors are crucial for monitoring various parameters and providing feedback to the control system. Actuators translate control signals into physical actions. Reliable sensors and actuators are critical for the consistent performance of your bottle filling capping machine.
3. Assembly and Integration: Bringing It All Together
The assembly process requires meticulous attention to detail. Ensure precise alignment of components and proper connections to prevent malfunctions. Consider the following:
* Modular Design: A modular design facilitates easier assembly, maintenance, and troubleshooting. This makes your bottle filling capping machine more adaptable to future changes.
* Testing and Calibration: Thoroughly test each component and subsystem before integrating it into the complete machine. Calibration ensures accurate filling and capping. This will guarantee the precise operation of your bottle filling capping machine.
* Safety Checks: Before commencing assembly, ensure you have all the necessary safety precautions in place, protecting against accidental injury or damage to the components.
4. Testing and Quality Control: Ensuring Performance
Rigorous testing is crucial to ensure the machine meets performance requirements and safety standards. This involves:
* Performance Testing: Evaluate filling accuracy, capping efficiency, and overall speed. This step guarantees that your bottle filling capping machine functions as designed.
* Safety Testing: Verify that all safety features function correctly, protecting operators from potential hazards. A robust safety testing process minimizes risk and maximizes safety.
* Durability Testing: Conduct stress tests to assess the machine's resilience and ability to withstand continuous operation. This process ensures the longevity of your bottle filling capping machine.
5. Final Adjustments and Deployment
Once testing is complete, make any necessary adjustments to optimize performance. Then, deploy the machine into your production line, ensuring proper integration with other equipment.
YUANYANG: Your Partner in Complete Production Line Solutions
While this guide provides a comprehensive overview of manufacturing a bottle filling and capping machine, the process can be complex. YUANYANG offers a complete range of industrial mixing and processing equipment, including integrated solutions that can streamline your entire production line. We can assist you in designing, selecting, and integrating the necessary components for efficient and effective bottling and capping. Our expertise extends beyond individual machines, offering support for the entire process.
Frequently Asked Questions (FAQs)
Q: What are the key factors to consider when choosing a filling mechanism for my bottle filling capping machine?
A: Key factors include the viscosity and characteristics of your product, desired filling accuracy, and production speed. Gravity filling is suitable for low-viscosity liquids, while volumetric and pressure filling are better for higher viscosity products or when precise filling is critical.
Q: How can I ensure the safety of operators during the operation of my bottle filling capping machine?
A: Incorporate safety features such as emergency stops, safety guards, and interlocks. Regular maintenance and operator training are also crucial. Comply with all relevant safety regulations and standards.
Q: What type of materials are best suited for a bottle filling capping machine?
A: Stainless steel is commonly preferred for its corrosion resistance, hygiene, and durability. However, the choice of material will depend on the specific product being filled and the operating environment.
Q: What are the advantages of a modular design for a bottle filling capping machine?
A: A modular design simplifies assembly, maintenance, and troubleshooting. It also allows for easier upgrades and modifications in the future, adapting to changing production needs and increasing the lifespan and efficiency of your bottle filling capping machine.
Q: How can I optimize the performance of my bottle filling capping machine?
A: Regular maintenance, proper calibration, and operator training are essential. Monitoring key performance indicators (KPIs) helps identify areas for improvement. Choose high-quality components and ensure proper integration within your production line.
Q: Where can I find reliable suppliers for components for my bottle filling capping machine?
A: YUANYANG can assist in connecting you with reliable suppliers for the high-quality components needed to build a robust and efficient bottle filling capping machine. We are your comprehensive resource for optimizing your entire production line.
Q: What support does YUANYANG provide after the sale of equipment?
A: YUANYANG provides comprehensive after-sales support, including installation assistance, training, and technical assistance. We are committed to the long-term success of our clients, and our after-sales services reflect this commitment. We are your one-stop shop for industrial mixer and complete production line solutions, providing seamless support and expertise throughout the entire process. Contact us today to learn more about how YUANYANG can assist you in building your ideal bottle filling and capping machine.
Top 10 dropper bottle capping machine Manufacturers and Supplier Brands in Europe
OEM/ODM screw feeder for powder Manufacturers and Suppliers
Why choose YUANYANG powder bottle filling machine manufacturer in Africa
What are the different types of bottle labeling machine?
Homogneizer mixer tank
Can I use city water to produce liquid detergent?
As you know, water takes 70-99% proportion of raw materials for liquid detergent production. So the quality of water is quite important to produce qualified liquid cleaning products. The raw water should be treated before taking into tank.
High shear homogneizer
Can the working head parts be dismountable?
Yes, the homogenizer head is dismountable. If there is any problem of the working head, just disassemble it and check. Videos is provided.
Homogenizer Mixing Tank with Circulation System
Can you add load cell system also for the liquid detergent making machine?
Yes, we add load cell upon requirements. Each mixer with 3 sets of load cell, and signal box, and display panel.
Semi Automatic Double Sides Labeling Machine
What’s the operation process?
Operation process: put the bottle on track- > step on the foot switch - > automatically taking the bottle in - > Automatically labeling - > Automatically taking the labeled bottle out.
Liquid Mixing Tank
Can the agitator speed be adjustable with VFD?
Yes,the agitator mixer is equipped with frequency converter. Speed can be variable by adjusting the speed regulation panel. If you want to save cost, or not variable speed is needed, there is no need to add VFD device.
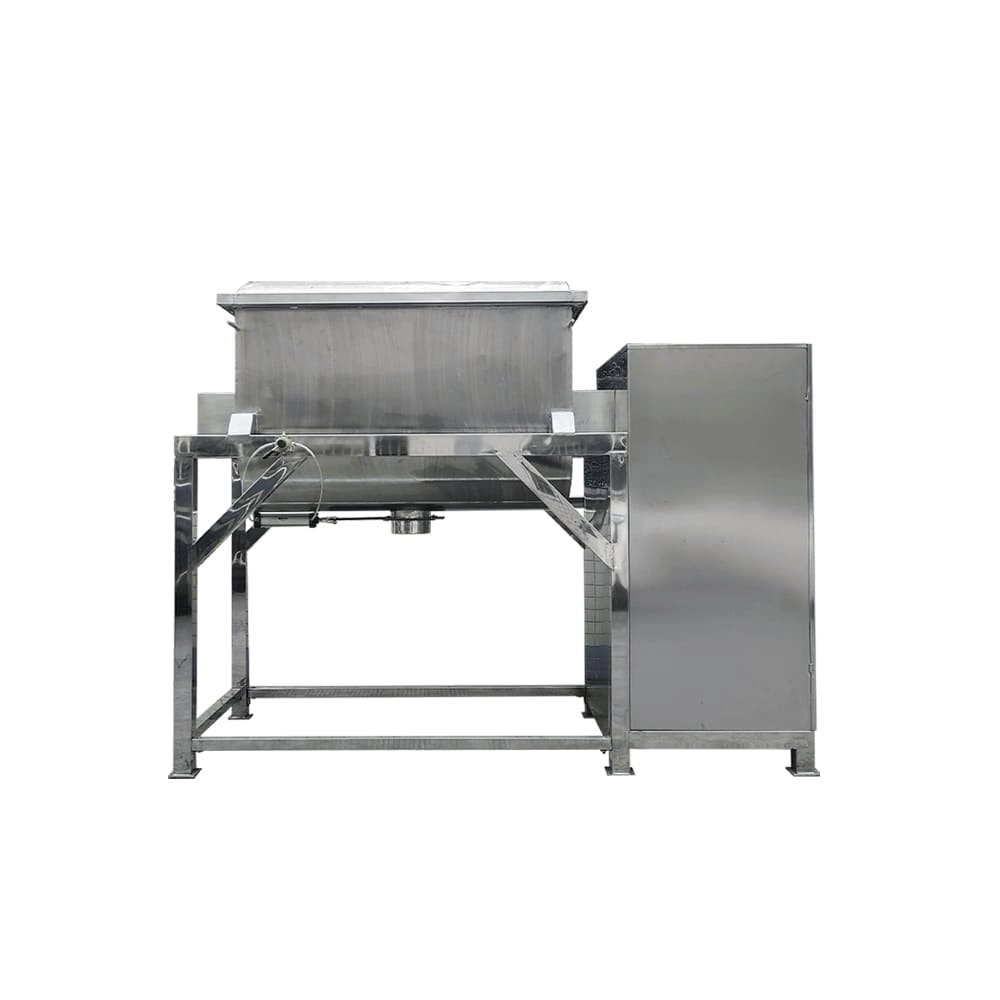
Detergent powder mixer for Sale
Yuanyang detergent powder mixer is also called a ribbon mixer, which is an industrial powder mixer machine applied to mix different kinds of raw powder together, especially used to produce detergent powder.
Feature:
-
⦁ Button control panel;
⦁ Food-grade materials;
⦁ U-shaped tank.
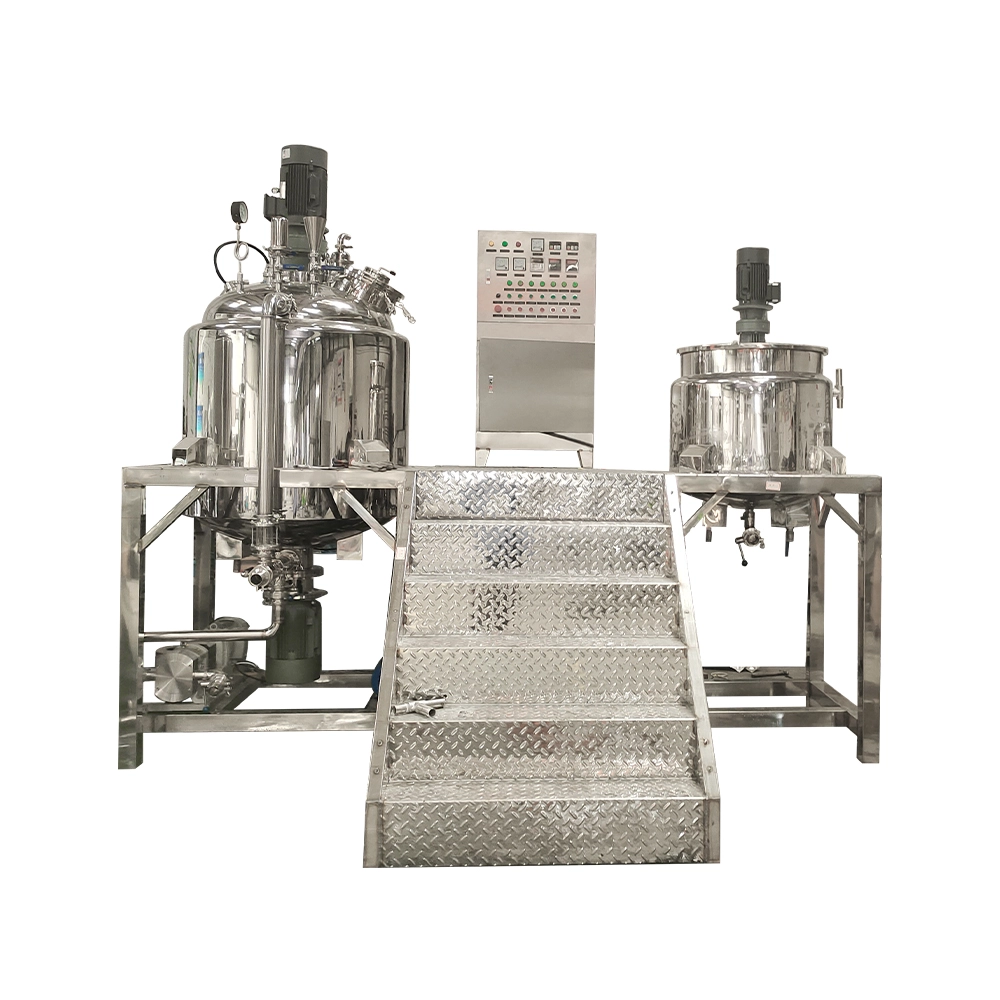
Vacuum Cosmetic Mixer with Water and Oil Tank for Sale
Yuanyang vacuum cosmetic mixer is a combined mixing equipment with a main vacuum homogenizer tank, water tank, and oil tank, which is an integrated equipment with a mixing, dispersing, homogenizing, emulsifying, and powder absorption system that is widely used in cosmetics, food, pharmaceutical, and chemical fields.
Features:
⦁ With a fixed lid, vacuum system, and electric control system.
⦁ Suitable for products of 10,000~50,000 cps viscosity.
⦁ Perfect particle size of 2 microns and evenly distributed.
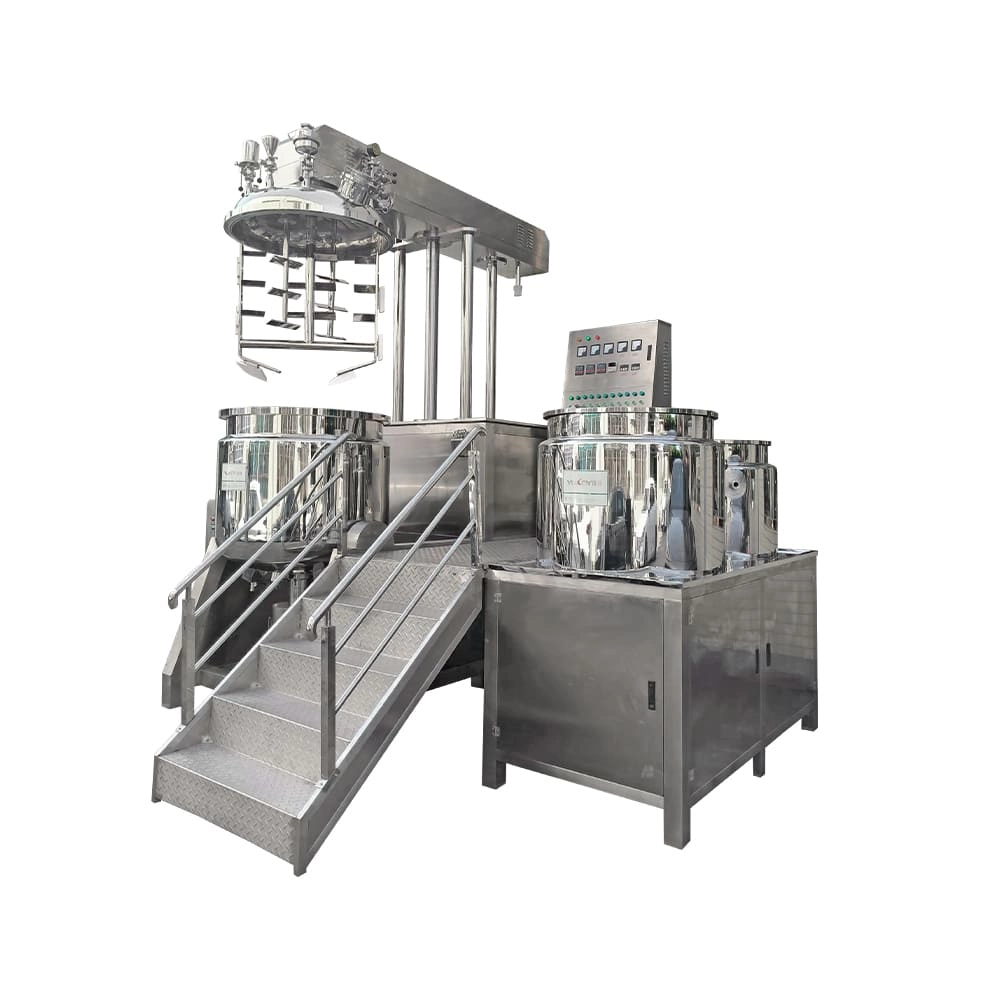
Hydraulic Lift Vacuum Mixer for Sale
Yuanyang hydraulic lift vacuum mixer is a kind of cosmetic mixing equipment, which is the core part of the cosmetic production line.
The hydraulic type is the most popular cosmetic production equipment for making cream, skin-care products, ointment, paste, emulsions, and so on.
Features:
⦁ Composed of a main emulsifying pot, a water pot, and an oil pot.
⦁ With a hydraulic lifting system, vacuum system, and electric control system.
⦁ Suitable for products of 10,000~50,000 cps viscosity.
⦁ Perfect particle size of 2 microns and evenly distributed.
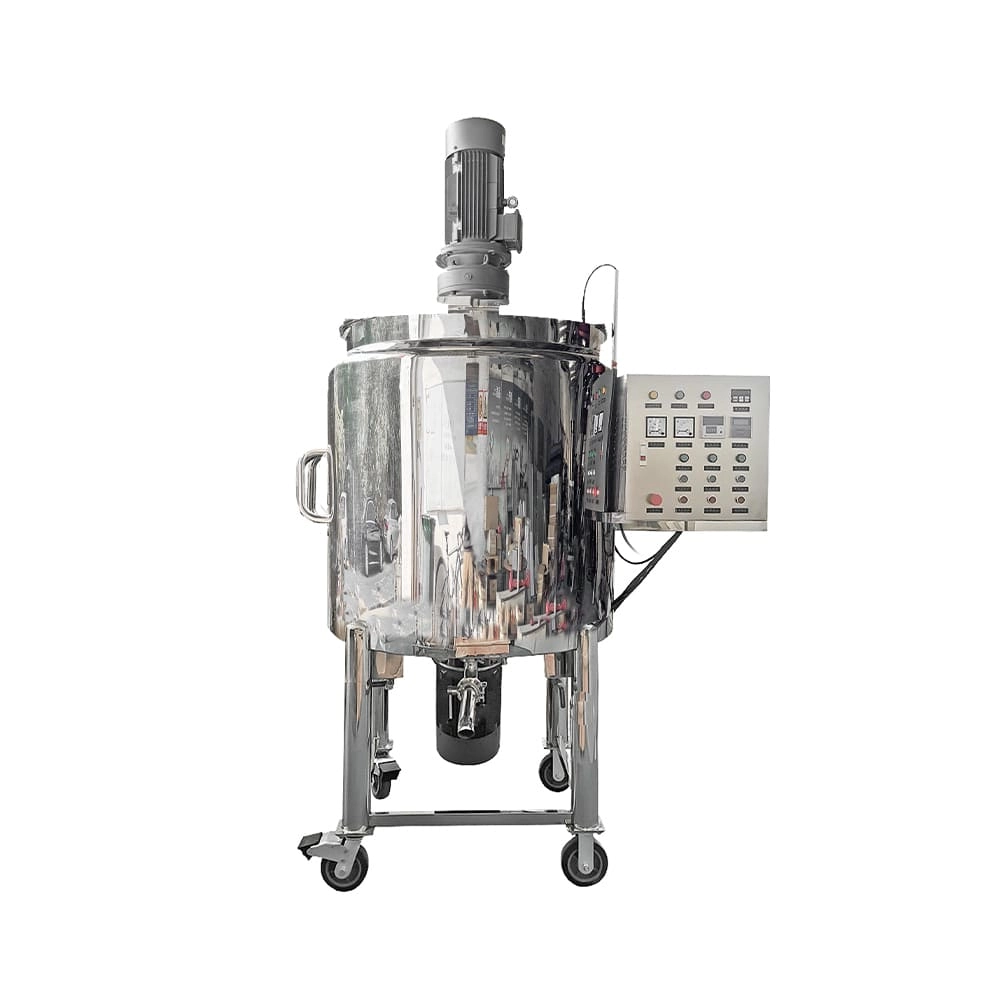
Homogenizing Mixer for Sale
Yuanyang homogenizing mixer is a liquid mixing tank with a high-shear homogenizer. The homogeneous mixing machine is the core part for the liquid soap production line for shampoo, body wash, laundry detergent, dish soap, hand sanitizer, and other thick liquids.
Features:
⦁ Flat top half-open lid, electric control system.
⦁ Suitable for various liquid cleaning products and sauces.
⦁ PTFE wall scrapers stirring at top, high shear homogenizer at bottom.
Facebook
YouTube
LinkedIn
Whatsapp: +8613434139712
Guangzhou Yuanyang Machinery