The Ultimate Guide to Liquid Mixing Tanks: Single, Double, and Three-Layer Models
Explore the different types of liquid mixing tanks: single, double, and three-layer models. Learn about their applications, benefits, and how to choose the right one for your needs.
- Understanding Liquid Mixing Tanks and Their Importance
- What is a Liquid Mixing Tank?
- Types of Liquid Mixing Tanks
- Single Layer Mixing Tank: Basic but Effective
- What is a Single Layer Mixing Tank?
- Applications of Single Layer Mixing Tanks
- Advantages of Single Layer Mixing Tanks
- Double Layer Mixing Tank: Added Heat Control
- What is a Double Layers Mixing Tank?
- Applications of Double Layers Mixing Tanks
- Advantages of Double Layer Mixing Tanks
- Three Layer Mixing Tank: Maximum Temperature Control and Insulation
- What is a Three Layers Mixing Tank?
- Applications of Three Layers Mixing Tanks
- Advantages of Three Layers Mixing Tanks
- Understanding the Thermal Insulation Layer
- Why is Thermal Insulation Necessary?
- Materials Used for Thermal Insulation
- How to Choose the Right Liquid Mixing Tank for Your Business
- Factors to Consider When Choosing a Mixing Tank
- Additional Features to Look For
- Benefits of Investing in the Right Liquid Mixing Tank
- Conclusion
- FAQs
Understanding Liquid Mixing Tanks and Their Importance
Liquid mixing tanks are essential equipment in various industries, ranging from food production to pharmaceuticals and chemicals. These tanks are designed to blend, mix, and homogenize liquids, ensuring consistent product quality. Depending on your needs, different types of liquid mixing tanks, such as single layer, double layers, and three layers, offer unique advantages in terms of performance, heat control, and mixing efficiency.
In this comprehensive guide, we will explore the various types of liquid mixing tanks, their functions, applications, and how to choose the right one for your operation.
What is a Liquid Mixing Tank?
A liquid mixing tank is a vessel used to mix different liquid ingredients into a homogeneous solution. This process is crucial in industries where precise mixing of liquids is required, such as cosmetics, chemicals, food, and beverage manufacturing.
Liquid mixing tanks come in various designs and capacities, and their primary goal is to ensure that the liquids within are mixed uniformly. They often feature mixing mechanisms such as paddles, impellers, or agitators to facilitate the mixing process.
Types of Liquid Mixing Tanks
There are primarily three types of liquid mixing tanks based on the number of layers that make up their construction:
Single Layer Mixing Tank
Double Layers Mixing Tank
Three Layers Mixing Tank
Each type offers different features and benefits depending on the requirements of the application. Let’s delve into the specifics of each.
Single Layer Mixing Tank: Basic but Effective
What is a Single Layer Mixing Tank?
A single layer mixing tank is the simplest form of a mixing tank, consisting of a single layer of material (usually stainless steel). These tanks are typically used for applications that do not require temperature control or advanced mixing techniques. There are some supplier may directly insert an electric tube into tank from bottom, which is dangerous.
Applications of Single Layer Mixing Tanks
Single layer mixing tanks are ideal for less complex mixing processes, such as:
Small-scale production: Perfect for small batches of liquid products.
Basic chemical formulations: Used where only basic mixing is required.
Cosmetic products: Such as shampoos, lotions, and other personal care items.
Non-sensitive products: For mixtures that do not need to be kept at a specific temperature.
Advantages of Single Layer Mixing Tanks
Cost-effective: Single-layer tanks are generally more affordable than their double or triple-layer counterparts.
Simple design: Easy to operate and maintain.
Versatile: Suitable for a wide range of industries, including food and beverage, cosmetics, and pharmaceuticals.
Double Layer Mixing Tank: Added Heat Control
What is a Double Layers Mixing Tank?
A double layers mixing tank consists of two layers, thus forming a jacket in the middle. The jacket is typically used to circulate heating or cooling fluids, which allows better temperature control during the mixing process. This is particularly useful in industries where temperature-sensitive products are being mixed.
It is quite often recommend just to use double layer for cooling purpose, not for heating purpose, because staff tend to be hurt by the outer layer.
Applications of Double Layers Mixing Tanks
Double layer mixing tanks are essential in situations where maintaining the correct temperature is crucial. They are commonly used in:
Food and beverage production: For mixing ingredients that need to be heated or cooled to specific temperatures, like sauces, syrups, and liquid-based foods.
Pharmaceuticals: To ensure the right temperature for chemical reactions or sensitive drug formulations.
Cosmetics: For emulsifying ingredients that require controlled heat, such as creams and lotions.
Advantages of Double Layer Mixing Tanks
Improved heat control: The second layer allows for better temperature regulation, ensuring a more consistent mixture.
Higher efficiency: Reduces the risk of overheating or overcooling the product.
Versatile for sensitive products: Perfect for applications that require precise temperature adjustments.
Three Layer Mixing Tank: Maximum Temperature Control and Insulation
What is a Three Layers Mixing Tank?
A three layers mixing tank offers the most advanced construction, with three layers—forming one inner jacket for heating or cooling purpose, and an outer jacket works as thermal insulation and safety protection (prevent staff being hurt and get injured). This type of tank is ideal for highly sensitive and complex applications where temperature regulation is critical for the integrity of the product.
Applications of Three Layers Mixing Tanks
Three-layer tanks are suitable for more demanding applications, such as:
High-end food processing: Where exact temperatures are needed to prevent flavor degradation or nutrient loss.
Pharmaceutical industry: For high-precision formulations that must be mixed at exact temperatures.
Cosmetic and skincare formulations: Where precise control over mixing and heating ensures consistent quality.
Advantages of Three Layers Mixing Tanks
Exceptional temperature control: The three-layer design provides superior insulation, allowing for fine-tuned temperature regulation.
Energy efficiency: The double-insulated layers help to reduce energy consumption while maintaining temperature.
Perfect for high-quality, sensitive products: Ensures the integrity and quality of complex products during the mixing process.
Understanding the Thermal Insulation Layer
The thermal insulation layer is just as crucial as the heating conducting layer, although it serves a different function. This layer helps prevent the heat from escaping the jacket mixer, ensuring that the heat energy is used efficiently and does not dissipate into the surrounding environment.
Why is Thermal Insulation Necessary?
In many industrial applications, precise temperature control is essential to achieving desired chemical reactions, preventing overcooking, or maintaining product quality. Without an adequate thermal insulation layer, much of the heat applied through the heating conducting layer could be lost, making the process less energy-efficient and potentially leading to temperature imbalances.
Materials Used for Thermal Insulation
Common materials used for the thermal insulation layer include rock wool, fiberglass, and ceramic fiber. These materials are selected for their ability to withstand high temperatures while minimizing heat loss. Additionally, they are lightweight and flexible, allowing for easy installation around the jacket mixer.
How to Choose the Right Liquid Mixing Tank for Your Business
Factors to Consider When Choosing a Mixing Tank
Nature of the Product: Consider whether your product is temperature-sensitive. For basic mixing, a single layer tank may suffice, but for sensitive or complex mixtures, a double or three-layer tank may be required.
Batch Size: The size of your production batch will determine the capacity you need. Larger batches often require more advanced tanks with enhanced temperature control and mixing capabilities.
Material Composition: Depending on the ingredients you need to mix, the material of the tank (usually stainless steel) should be resistant to corrosion or contamination.
Budget: Single layer mixing tanks are the most affordable, while double and three-layer models come at a higher cost due to the added features such as temperature control.
Compliance: Ensure that the tank meets industry standards and regulations, especially in sensitive sectors like food and pharmaceuticals.
Additional Features to Look For
Agitation Mechanism: The type of mixer (impellers, paddles, etc.) can influence the efficiency of the mixing process.
Ease of Maintenance: Choose tanks that are easy to clean and maintain to ensure longevity and hygiene standards.
Automation: Advanced models may come with automated controls for temperature, mixing speed, and other parameters, which can improve operational efficiency.
Benefits of Investing in the Right Liquid Mixing Tank
Choosing the right liquid mixing tank can result in a more efficient production process, improved product quality, and reduced operational costs. By investing in the appropriate tank for your needs, you can ensure:
Consistency: A well-mixed product that meets quality standards every time.
Time efficiency: Faster mixing processes that reduce overall production time.
Cost savings: Energy-efficient models (especially double and triple-layer tanks) help lower operational costs over time.
Conclusion
Liquid mixing tanks, whether single, double, or three layers, are indispensable tools across various industries that require precise blending of liquids. The choice between these models depends on factors such as the sensitivity of the products, temperature control requirements, and your budget.
Understanding the advantages and applications of each type will help you select the most suitable tank for your business, ensuring that your mixing processes are efficient, cost-effective, and capable of producing high-quality products.
FAQs
1. What is the difference between a single layer mixing tank, a double layer mixing tank and a three-layer mixing tank?
A single layer mixing tank consists of one layer of material, making it simple and cost-effective for non-temperature-sensitive applications. A double-layer mixing tank forms a jacket allowing for temperature control, which is important for products that need heating or cooling during the mixing process.
A three-layer mixing tank forms double jackets. The inner jacket is used to circulate heating or cooling fluids, ensuring the product inside is kept at the required temperature. The outer jacket is designed for insulation and protection purpose.
The recommendation for client is to choose 1 layer for no heating or cooling purpose, and 2 layers for cooling, 3 layers for heating with insulation.
2. What industries use liquid mixing tanks?
Liquid mixing tanks are used in a wide range of industries, including food and beverage, pharmaceuticals, cosmetics, chemicals, and bioengineering.
3. How do I maintain a liquid mixing tank?
Maintenance typically involves regular cleaning, inspection of mixing components, ensuring proper sealing, add lubricate oil regularly and checking for any wear and tear. It’s essential to follow the manufacturer's maintenance guidelines to ensure optimal performance.
4.What’s materials of the mixing tank?
The mixing tank is made of stainless steel 304 and 316L. Normally, the single layer mixing tank contact layer is stainless steel 316, the double layer mixing tank, the inner contact layer is made of 316.
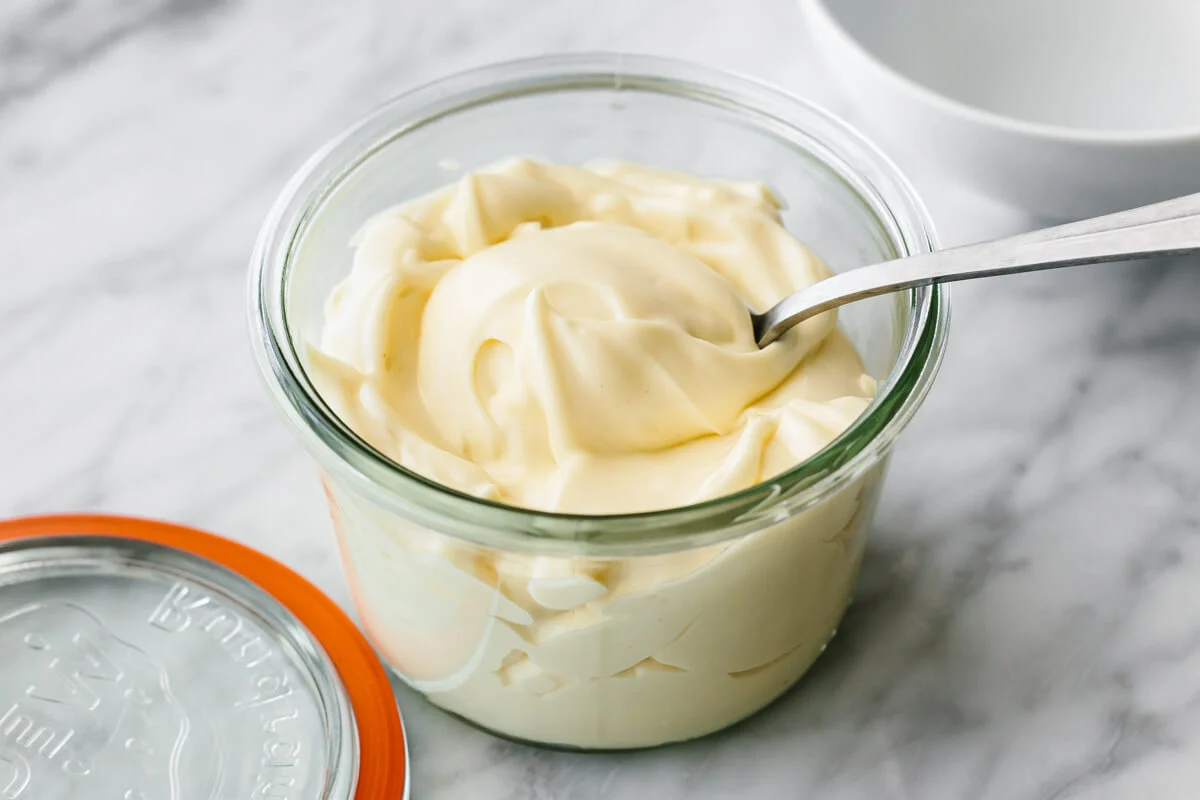
Mayonnaise Manufacturing Process Explained: How Factories Produce Mayonnaise

Water in Oil Emulsion: Meaning, Real-Life Examples, and How to Fix It
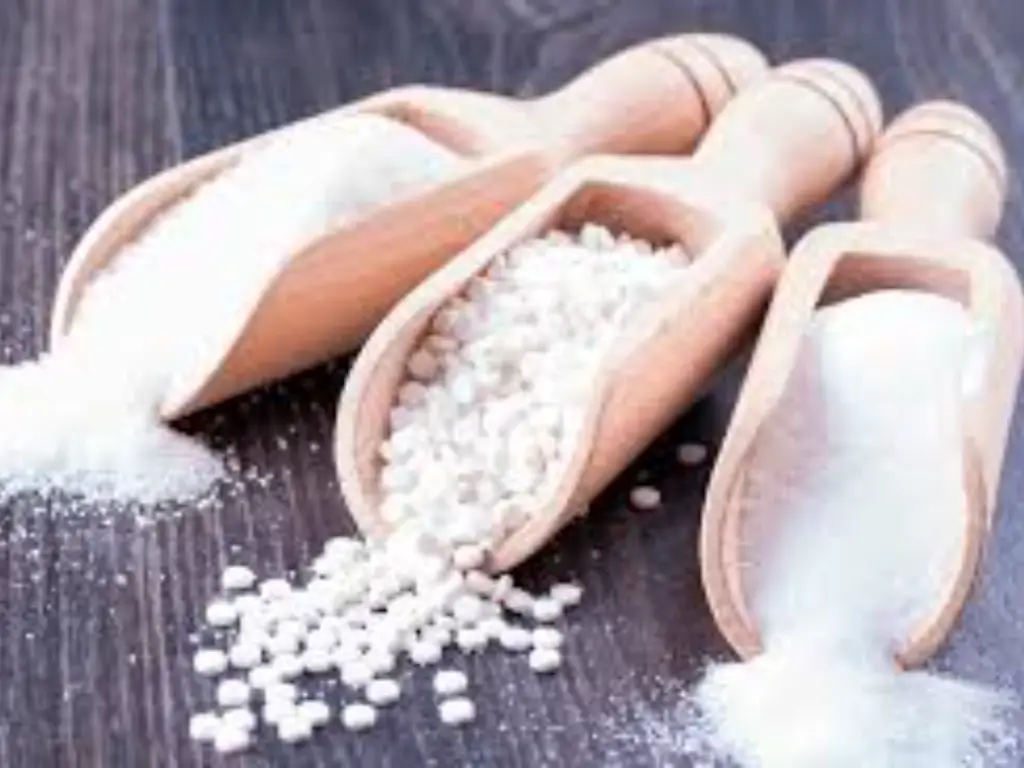
How Artificial Sweeteners Are Made: Inside the Manufacturing Process & Key Equipment
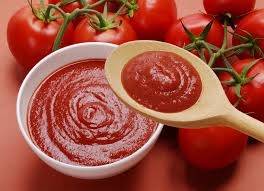
Ketchup Explained: From Ancient Origins to Modern Production Methods
How Lotion Is Made: Step-by-Step Guide for Home and Factory Production
Medicine
Can I customize the equipment to meet specific production needs?
Absolutely. Yuanyang offers customized equipment solutions, adjusting the functionality, size, or processes based on your production requirements to meet your unique needs.
Vertical Filling Machine
The power supply is 220v 60hz, can I use this paste filling machine?
Sure, the machine is only pneumatic drive, you just use local air compress to connect to it. There is no need to worry about power supply.
Homogenizing Mixer
What’s the rotation speed of the bottom homogenizer head of the liquid detergent mixer?
The standard homogenizer is with high speed 3000 rpm, we can customize other bigger speed according to actual needs.
Vibrating sieving machine
Can you add more layer to filter different sizes for the industrial shaker machine?
Yes, we can customize 1-5 layers according to needs.
Desktop Labeling Machine
Is the supporting table in the pictures be sold together with automatic bottle labeling machine?
Yes, the regular quote does not include the supporting table which is optional, but we will provide if clients need, the table on wheels.
Leave a message
Have any questions or concerns about our products? Please leave us a message here, and our team will get back to you promptly.
Facebook
YouTube
LinkedIn
Whatsapp: +8613434139712
Guangzhou Yuanyang Machinery