do i really need a capping machine | YUANYANG Expert Guide
- Do You Really Need a Capping Machine for Your Industrial Production Line?
- Is Manual Capping Still a Viable Option for My Growing Production?
- What Tangible Benefits Can a Capping Machine Bring to My Bottom Line?
- Which Type of Capping Machine is Best Suited for My Mixer's Product Output?
- How Do I Calculate the Return on Investment (ROI) for a Capping Machine?
- How Seamlessly Will a Capping Machine Integrate with My Existing Industrial Mixer Line?
- YUANYANG: Your Partner in Integrated Production Solutions
Do You Really Need a Capping Machine for Your Industrial Production Line?
For businesses in the industrial mixer sector, producing high-quality liquid, cream, or paste products is just one part of the journey. The next critical step is packaging – specifically, sealing. You’ve invested in robust industrial mixers to achieve perfect consistency and blend quality. But what about the final seal? The question, Do I really need a capping machine? is more relevant than ever for companies looking to scale, improve efficiency, and maintain product integrity.
Let's explore the five most common questions that arise when considering this crucial investment.
Is Manual Capping Still a Viable Option for My Growing Production?
While manual capping might seem cost-effective for startups or very low-volume production, its limitations quickly become apparent as your business grows. Manual operations are inherently slow, prone to inconsistencies, and labor-intensive. Typically, a skilled worker can manually cap anywhere from 5 to 15 bottles per minute. In contrast, even a semi-automatic capping machine can achieve 20-40 bottles per minute, and fully automatic systems can easily exceed 60-300+ bottles per minute, with high-speed lines reaching over 600 BPM. For operations that utilize industrial mixers to produce hundreds or thousands of liters daily, relying on manual capping creates a significant bottleneck, drives up labor costs, and makes scaling incredibly difficult. Moreover, human fatigue leads to inconsistent torque, increasing the risk of leaks or damaged caps, directly impacting product quality and shelf life.
What Tangible Benefits Can a Capping Machine Bring to My Bottom Line?
Investing in a capping machine offers numerous advantages that directly impact your profitability and brand reputation:
- Increased Throughput: Dramatically higher speeds mean more products packaged per hour, directly boosting your production capacity.
- Consistent Quality: Automated systems apply precise and repeatable torque, ensuring every cap is sealed correctly, reducing leaks, spills, and product waste. This consistency is vital for maintaining product integrity, especially for viscous materials prepared by industrial mixers.
- Reduced Labor Costs: Automation minimizes the need for manual labor on the packaging line, allowing you to reallocate staff to more value-added tasks. This can lead to significant long-term savings.
- Improved Product Presentation: Uniformly capped products look more professional and appealing on shelves, enhancing brand image.
- Enhanced Compliance: Many industries (food, pharmaceutical, cosmetic) have stringent regulations for sealing and tamper-evidence. Automated cappers can reliably meet these standards, including applying child-resistant or tamper-evident seals.
- Reduced Product Spoilage: A consistent, tight seal prevents oxygen ingress and product evaporation, extending shelf life and reducing costly returns due to spoilage.
Which Type of Capping Machine is Best Suited for My Mixer's Product Output?
The choice of capping machine depends on your product's viscosity (from your industrial mixer), bottle type, cap type, and desired speed. Here are common types:
- Spindle Cappers (Continuous Motion): Ideal for screw caps on a wide range of bottle types. They use spinning discs to apply and tighten caps as containers move along a conveyor. Highly versatile for products like sauces, oils, and detergents.
- Chuck Cappers (Intermittent Motion): These machines pick up a cap, place it on the bottle, and apply torque using a chuck head. Excellent for delicate caps, irregular cap shapes, or applications requiring very precise torque control, such as cosmetics or pharmaceuticals.
- Snap Cappers: Designed for caps that simply snap on, common for certain food containers or health supplements.
- ROPP Cappers (Roll-On Pilfer-Proof): Form a thread on a blank aluminum cap directly onto the bottle neck, creating a tamper-evident seal. Popular for beverages, spirits, and some pharmaceutical products.
- Induction Sealers: While not a capping machine itself, an induction sealer is often integrated *after* capping to create a hermetic seal under the cap, crucial for food, beverage, and pharmaceutical products to prevent leaks and extend shelf life.
Considering the viscosity and density of products handled by industrial mixers – from thin liquids to thick pastes – understanding the cap type (screw, snap, pump, trigger) and bottle material is crucial for selecting the right capping technology.
How Do I Calculate the Return on Investment (ROI) for a Capping Machine?
Calculating ROI involves comparing the initial investment (machine cost, installation, training) against the savings and increased revenue generated. Key factors to consider:
- Labor Savings: Calculate the hourly cost of manual labor vs. the operational cost of the machine. For instance, replacing 2-3 full-time manual cappers with one automatic machine can yield significant annual savings.
- Increased Throughput: Estimate the additional units you can produce and sell per day/month.
- Reduced Waste & Rework: Quantify savings from fewer rejected products due to inconsistent sealing or spills. Automated systems can reduce waste by 5-15% compared to manual processes.
- Improved Product Quality/Shelf Life: Less spoilage means fewer returns and higher customer satisfaction.
- Initial Cost: Semi-automatic cappers can range from $5,000 to $30,000+. Fully automatic inline systems typically start from $30,000 and can go up to $150,000+, with high-speed rotary systems potentially exceeding $500,000. Many businesses see a full ROI within 1-3 years, depending on their production volume and current labor costs.
How Seamlessly Will a Capping Machine Integrate with My Existing Industrial Mixer Line?
Modern capping machines are designed for seamless integration into existing packaging lines. The primary consideration is ensuring a smooth flow from your filling machine (which follows your industrial mixer) to the capper. This involves:
- Conveyor Compatibility: Ensuring bottle sizes and speeds are compatible between your filler and the capper.
- Synchronization: Integrating control systems so the filler and capper operate in harmony, preventing backlogs or dry runs.
- Space Requirements: Assessing the physical footprint needed for the new machine within your current production layout.
- Product Handling: For viscous or sensitive products prepared by industrial mixers, ensure the capping machine can handle the specific container and cap type without spillage or damage. For example, some products might require specific cap feeding mechanisms or gentle handling.
A well-integrated capping machine transforms your production from a series of disjointed steps into a fluid, efficient, and automated process, ensuring your precisely mixed products are perfectly sealed and ready for market.
YUANYANG: Your Partner in Integrated Production Solutions
At YUANYANG, we understand the intricacies of industrial production, from precise mixing to efficient packaging. While our core expertise lies in providing state-of-the-art industrial mixers that deliver unparalleled product quality, we also recognize the critical need for seamless downstream processes like capping. We support our clients by offering expert advice on integrating packaging solutions that complement your YUANYANG mixer setup. Our commitment to quality, reliability, and technical support ensures that when you invest in a YUANYANG mixer, you're building a foundation for a fully optimized and highly efficient production line, ready to accommodate advanced packaging machinery and meet market demands with confidence.
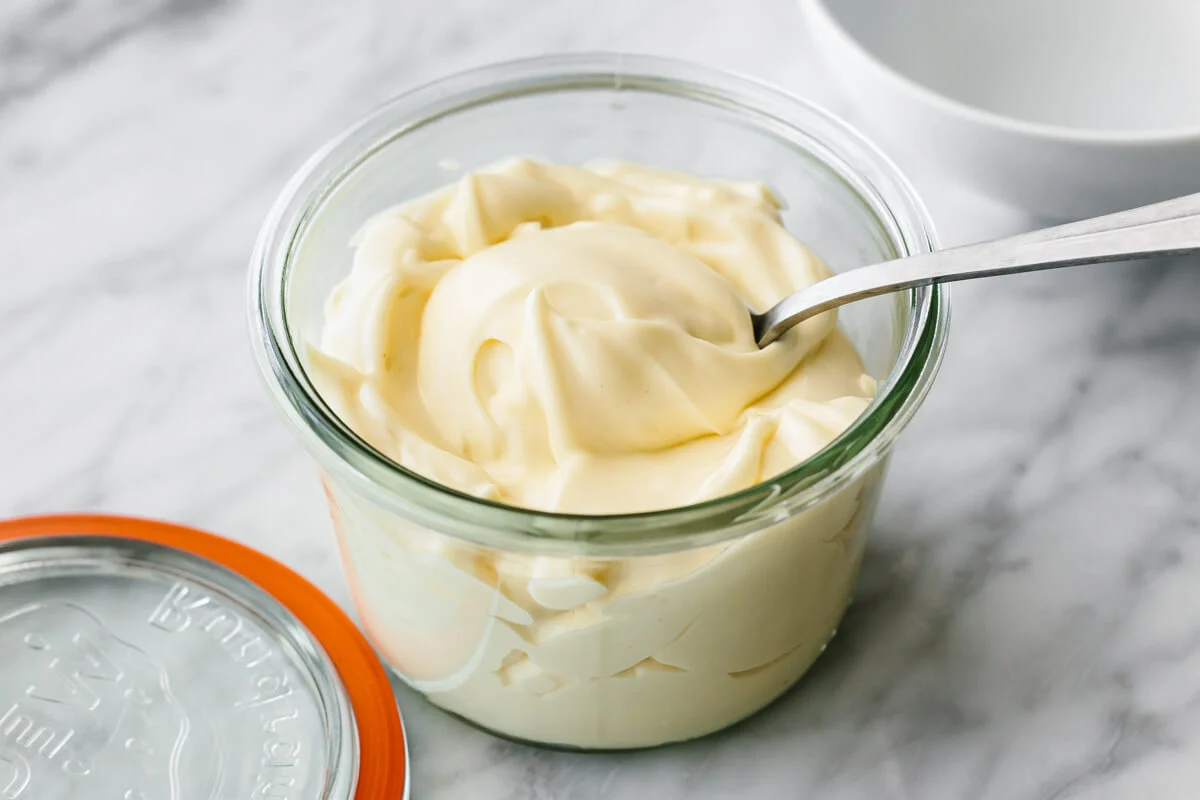
Mayonnaise Manufacturing Process Explained: How Factories Produce Mayonnaise

Water in Oil Emulsion: Meaning, Real-Life Examples, and How to Fix It
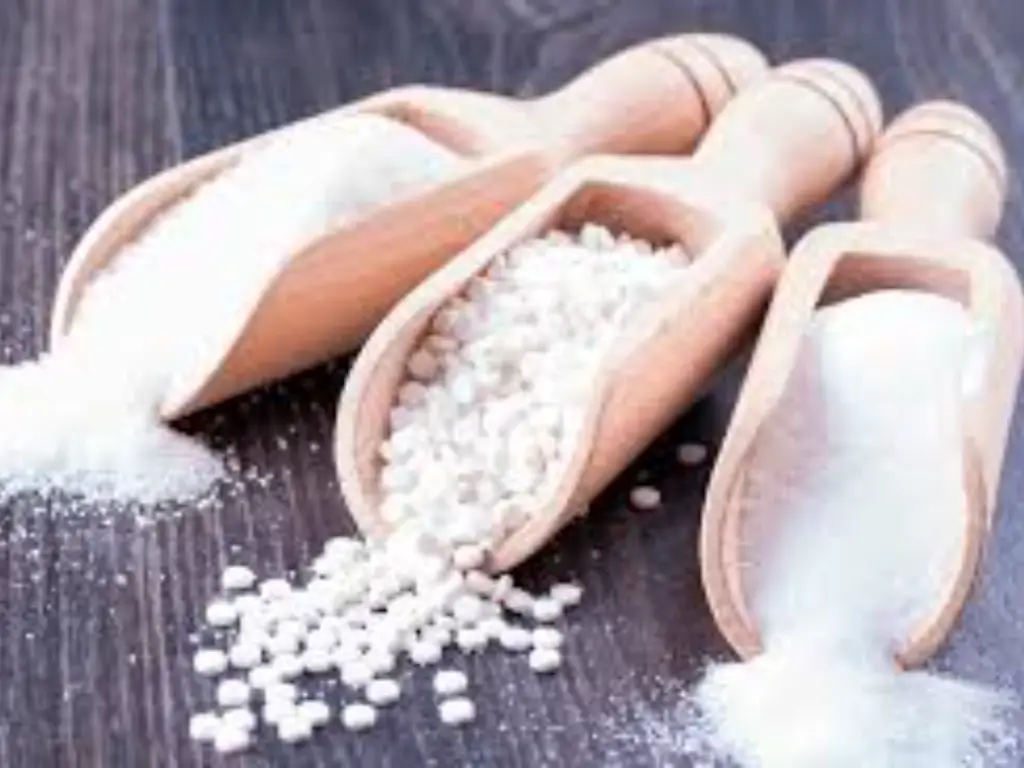
How Artificial Sweeteners Are Made: Inside the Manufacturing Process & Key Equipment
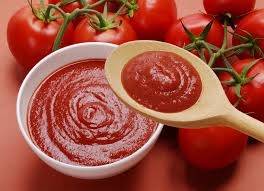
Ketchup Explained: From Ancient Origins to Modern Production Methods
How Lotion Is Made: Step-by-Step Guide for Home and Factory Production
Semi Automatic Capping Machine
Can it close glass bottles?
As long as the glass bottle has screw cap, the capping machine can close its cap, although the machine is often called plastic capping machine.
FAQs
What’s your payment term?
Generally, we take 30% of total amount as down payment, which should be wired by T/T. The 70% balance will be paid by T/T after you inspect your machines before shipment. We also accept letter of credit although it takes more expenses. But our bank should confirm your opening bank’s credit first.
Liquid Soap Mixer
Can you also provide the related production machines?
Yes, we supply the complete set of liquid soap production machines, such as filling machine,capping machine,labeling machine,sealing machine, and coding machine.
Aluminum Foil Sealing Machine
Can I put the lid sealer machine on the metal floor?
No, it is strictly prohibited to put the seal on the case or large area of metal, so as to avoid burning the power tube
Powder Sachet Packaging Machine
Is the length of bag-forming adjustable for this automatic packing machine?
Yes, the bag-forming length can be adjusted on the control panel within certain range of the model.
Leave a message
Have any questions or concerns about our products? Please leave us a message here, and our team will get back to you promptly.
Facebook
YouTube
LinkedIn
Whatsapp: +8613434139712
Guangzhou Yuanyang Machinery